The Sand Casting Industry A Cornerstone of Manufacturing
Sand casting, a process that has been utilized for thousands of years, remains a fundamental method in the manufacturing sector, particularly in the production of metal components. This technique, characterized by its simplicity and adaptability, continues to thrive in various industries ranging from automotive to aerospace, and even in art. In this article, we’ll delve into the intricacies of the sand casting industry, exploring its process, benefits, applications, and future prospects.
Understanding the Sand Casting Process
The sand casting process involves several key steps that transform raw materials into finished metal products. Initially, a pattern, typically made of metal or plastic, is created to serve as a model for the final object. This pattern is then placed in a container filled with a sand mixture, which usually consists of silica sand, a bonding agent, and water. The sand is compacted around the pattern to form a mold. After the mold has set, the pattern is removed, resulting in a cavity that replicates the shape of the intended object.
Next, molten metal is poured into the mold, filling the cavity and taking on its shape. Once the metal has cooled and solidified, the sand mold is broken apart to reveal the cast part. The final step involves removing any excess material, grinding, and finishing the product to meet specific tolerances and surface qualities.
Advantages of Sand Casting
Sand casting has several distinct advantages that make it a popular choice among manufacturers
1. Cost-Effectiveness One of the most appealing aspects of sand casting is its affordability, especially for small to medium production runs. The materials required for sand casting, such as sand and metal, are relatively inexpensive, and the process can be efficiently adapted for various designs without significant cost increases.
2. Versatility This method can accommodate a wide range of alloys and is suitable for both ferrous and non-ferrous metals. Sand casting can produce intricate designs, complex geometries, and large parts, which makes it widely applicable in diverse industries.
3. Simplicity The sand casting process is relatively straightforward, allowing for quick adjustments and modifications to the molds and patterns. This flexibility caters to the evolving needs of manufacturers, enabling rapid prototyping and development.
sand cast industries
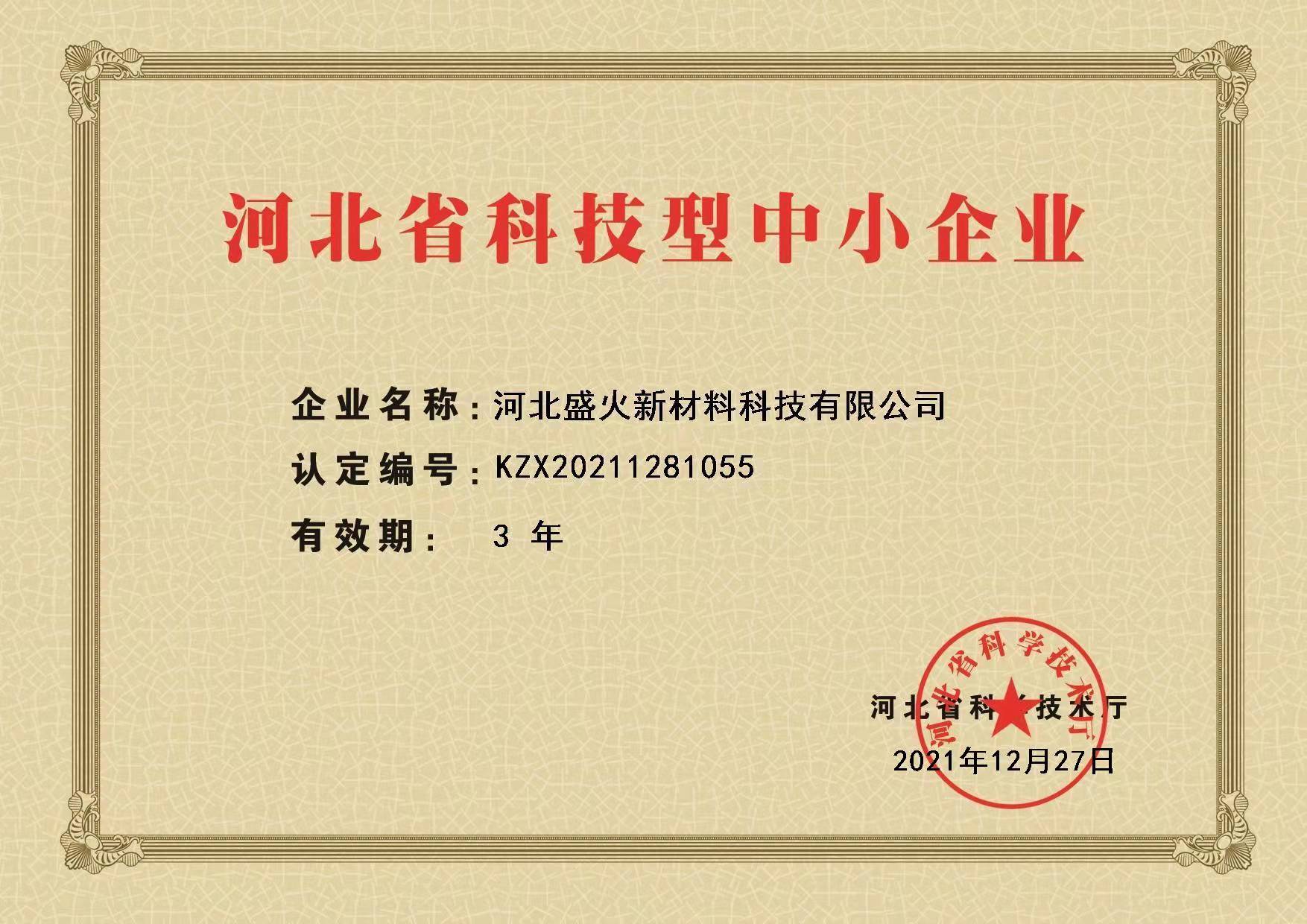
4. Large Component Production Sand casting is particularly well-suited for producing large components that are often challenging to manufacture using other methods. Industries such as construction and heavy machinery frequently rely on sand casting for parts like engine blocks, pump housings, and more.
Applications Across Industries
The versatility and cost-effectiveness of sand casting make it applicable in a variety of sectors. In the automotive industry, for instance, numerous engine components, transmission housings, and various brackets are produced using sand casting techniques. The aerospace sector also utilizes sand casting for producing parts that require lightweight yet durable materials, such as landing gear components and structural frames.
In addition to these traditional sectors, the art world also benefits from sand casting. Artists and sculptors often use this method to create stunning bronze sculptures and other decorative items, showcasing the aesthetic potential of cast metalwork.
The Future of Sand Casting
While the sand casting industry is steeped in tradition, it is not immune to technological advancements. Innovations such as 3D printing are beginning to make an impact on the sand casting process, allowing for more intricate mold designs and faster production times. Additionally, the integration of smart technologies and automation can enhance efficiency and reduce waste.
As the demand for sustainable practices grows, the sand casting industry is also adapting to reduce its environmental footprint. Research and development are focused on creating eco-friendly binders and recycling sand materials to lessen waste and promote sustainability.
Conclusion
Sand casting continues to be a vital component of the manufacturing landscape. Its cost-effectiveness, versatility, and ability to produce large components make it indispensable across numerous industries. With the integration of modern technologies and a growing emphasis on sustainability, the sand casting industry is poised for innovation and growth. As we look to the future, one thing remains clear sand casting will remain a pillar of manufacturing, demonstrating the enduring power of this age-old technique in a rapidly evolving world.
Post time:Νοέ . 24, 2024 18:34
Next:what type of sand is used for sand casting