Introduction to Resin Sand Casting
Resin sand casting is a modern manufacturing process that combines the versatility of sand casting with the technological advantages of synthetic resins. This method is widely used in various industries, including automotive, aerospace, and general engineering, due to its ability to produce high-quality, intricate castings with remarkable precision. In essence, resin sand casting is an innovative solution that addresses the limitations of traditional sand casting methods.
The Process of Resin Sand Casting
The resin sand casting process begins with the preparation of the sand mixture. This typically consists of silica sand, which is combined with a thermosetting resin and a curing agent. The proportion of these materials can be adjusted based on the specific requirements of the casting, such as strength, thermal stability, and surface finish.
Once the sand mixture is prepared, the next step involves molding. In resin sand casting, two mold halves are created, which are then assembled together to form a cavity that defines the shape of the desired casting. The use of resin in the mixture allows for the molds to cure without the need for water, resulting in a faster hardening time. This quick curing process not only speeds up production but also enhances the dimensional accuracy of the molds.
After the molds have sufficiently cured, they are ready for the pouring stage. Molten metal is heated to a specific temperature depending on its type and poured into the mold cavity. The resin bonds the sand particles together tightly, ensuring that the mold retains its shape during the pouring process. As the metal cools and solidifies, the casting takes on the intricate details of the mold, leading to high-quality finishes.
Once the metal has cooled sufficiently, the mold is broken apart to reveal the casting. The use of resin in the sand mixture results in a smoother surface finish and finer details compared to traditional sand casting methods. The castings may then undergo further processes such as machining, coating, and assembly, depending on their intended application.
resin sand casting
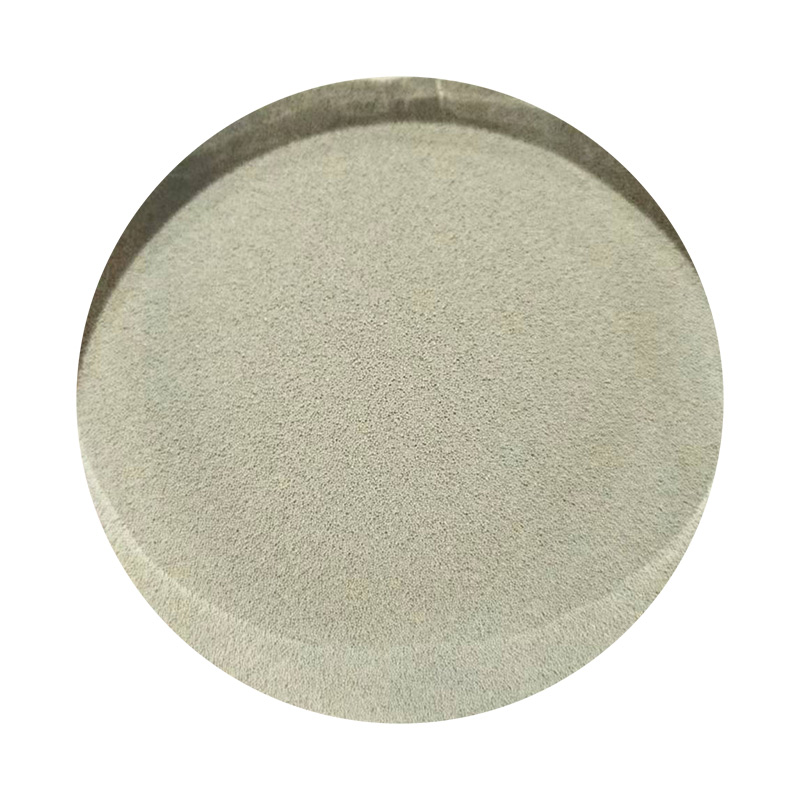
Advantages of Resin Sand Casting
One of the most significant advantages of resin sand casting is its ability to produce complex geometries with high dimensional accuracy. The resin's properties allow for thinner sections and intricate designs that were previously difficult to achieve. Additionally, the process significantly reduces the likelihood of defects such as mold shifting and distortion, which can occur with traditional sand molds.
Moreover, the surface finish of resin sand castings is superior due to the fine grain structure of the cured resin. This results in reduced post-processing requirements, saving both time and costs. The elimination of water from the mixture also makes resin sand casting more suitable for environments with strict humidity control, reducing the risks of defects related to moisture content.
Another advantage is the versatility of the resin sand casting process. It is compatible with a wide range of metals, including aluminum, iron, and copper alloys. This allows manufacturers to select the ideal material for their specific application, ensuring optimal performance of the final product.
Conclusion
In conclusion, resin sand casting stands out as a highly effective manufacturing process that merges traditional sand casting with modern technology. Its ability to produce high-quality, complex castings with improved surface finishes and dimensional accuracy makes it a preferred choice for various industries. As technology continues to advance, resin sand casting is likely to play an increasingly prominent role in the evolution of manufacturing practices, contributing to both efficiency and sustainability.
Post time:Δεκ . 20, 2024 03:24
Next:Exploring Innovative Applications of 3D Printing with Sand Materials in Modern Manufacturing