Materials Used for Sand Casting
Sand casting is one of the oldest and most widely used metal casting processes, primarily due to its versatility, low cost, and ability to produce complex shapes. The quality and characteristics of the final cast product heavily depend on the materials used in the sand casting process. Understanding these materials is essential for optimizing the casting environment and achieving desired results in terms of strength, durability, and surface finish.
1. Sand
The primary material used in sand casting is the molding sand, which serves as the mold for the metal being cast. The most commonly used type of sand is silica sand, primarily because of its high melting point and excellent thermal properties. Silica grains are typically mixed with a binder (like clay) and water to create a mold with sufficient strength to hold its shape during the metal pouring process. Other types of sand may include olivine sand, which is more resistant to thermal shock, and zircon sand, which offers superior dimensional stability.
2. Binders
Binders play a crucial role in sand casting, as they help to bind the sand grains together, forming a solid mold. The most common binder used is bentonite clay, known for its remarkable ability to absorb water and swell, which enhances the mold's strength. Organic binders, such as phenolic resins, are also used, particularly in modern casting applications, as they can provide better surface finishes and faster curing times. The choice of binder can significantly impact the casting quality and the ease of mold removal after casting.
materials used for sand casting
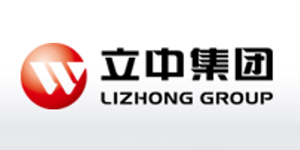
3. Metal Alloys
The type of metal alloy poured into the mold is equally important. Commonly used alloys in sand casting include aluminum, iron, and copper alloys. Aluminum alloys are favored for their lightweight properties and corrosion resistance, making them ideal for applications in automotive and aerospace industries. Cast iron, particularly gray cast iron, is praised for its excellent machinability and wear resistance, making it suitable for heavy machinery components. Copper alloys, including bronze and brass, are known for their superior mechanical properties and aesthetic appeal, often used in artistic applications and architectural features.
4. Additives
To improve specific properties of the casting, various additives may be utilized. These can include anti-foaming agents to reduce gas porosity, coloring agents for aesthetic purposes, and grain refiners to enhance the mechanical properties of the finished product.
Conclusion
In summary, the materials used in sand casting—sand, binders, metal alloys, and additives—are critical to achieving successful castings. Understanding these materials and their properties allows manufacturers to optimize the casting process, ensuring high-quality products that meet the requirements of various industries. With advancements in technology, the materials and methods used in sand casting continue to evolve, enhancing its effectiveness and efficiency.
Post time:Νοέ . 19, 2024 13:32
Next:sand casting foundry