Lost Foam Castings A Modern Approach to Precision Metal Casting
In the realm of manufacturing, various casting techniques have evolved to meet the increasing demands for precision and efficiency. One such method gaining prominence is lost foam casting. This innovative process offers manufacturers an advanced solution for creating intricate metal components with high dimensional accuracy and minimal finishing work. In this article, we will explore the principles behind lost foam castings, its advantages, applications, and the future prospects of this casting technique.
Understanding Lost Foam Casting
The lost foam casting process involves creating a foam pattern that is coated in a thin layer of refractory material and subsequently used to produce cast metal components. The technique starts with the creation of a pattern made from a polystyrene foam material. This pattern is then coated with a fine sand mixture, which adheres to the surface due to the binder agents in the sand. Once the foam pattern is fully coated, it's placed in a mold, where molten metal is poured directly into the mold. As the hot metal enters, it vaporizes the foam pattern, allowing the metal to fill the cavity left behind.
This method is conceptually similar to the lost-wax casting technique but offers distinct advantages that contribute to its rising popularity in various industries. The foam patterns can be produced quickly and at a lower cost when compared to traditional metal patterns, resulting in significant time and cost savings during the production phase.
Advantages of Lost Foam Casting
1. Complex Shapes and Designs One of the most notable advantages of lost foam casting is its ability to reproduce complex geometries with high precision. The foam patterns can be manufactured into intricate designs that may be challenging or impossible to achieve with traditional casting methods. This capability makes it an ideal choice for industries that require detailed components, such as automotive and aerospace.
2. Cost-Efficiency The production of foam patterns is generally less expensive than manufacturing metal patterns, especially for short production runs. Additionally, lost foam casting minimizes the need for secondary machining processes, as the final cast components typically require less finishing work. This efficiency can lead to significant cost reductions over time.
lost foam castings
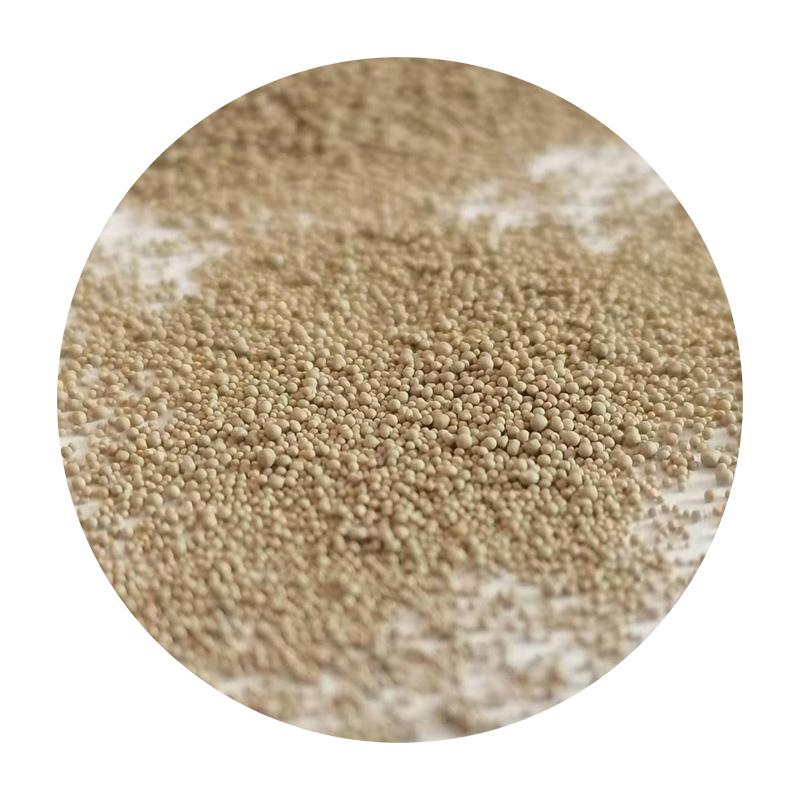
3. Reduced Material Waste In lost foam casting, the vaporization of the foam pattern means that there is no solid waste produced during the process. This eco-friendly aspect aligns with the growing emphasis on sustainability in manufacturing, making lost foam casting a more environmentally responsible option.
4. Improved Surface Finish The surface finish of components produced through lost foam casting is often superior to that of other casting methods. The fine sand coating contributes to a smoother surface, reducing the need for extensive post-casting machining and improving the overall aesthetic of the final product.
Applications of Lost Foam Casting
Lost foam casting finds applications in diverse industries due to its versatility and efficiency. The automotive sector frequently employs this technique for producing engine blocks, transmission housings, and other intricate components. In the aerospace industry, the need for lightweight and complex parts makes lost foam casting an appealing choice for manufacturing turbine blades and other critical components.
Additionally, the process is utilized in producing industrial machinery, HVAC components, and consumer products. The ability to create customized parts quickly and at a lower cost has made lost foam casting an indispensable tool for manufacturers seeking to innovate and improve their efficiencies.
Future Prospects
As technology advances, the potential for lost foam casting continues to expand. The integration of computer-aided design (CAD) and computer-aided manufacturing (CAM) is likely to refine the pattern-making process, allowing for even greater complexity and precision in the final products. Furthermore, the ongoing development of eco-friendly materials and processes will enhance the sustainability profile of lost foam casting, making it a more attractive option for environmentally conscious manufacturers.
In conclusion, lost foam casting is a promising metal casting technique that presents numerous advantages over traditional methods. Its capability to produce intricate designs with high precision, coupled with cost-efficiency and sustainability, makes it a valuable asset in various industrial applications. As manufacturing technologies continue to evolve, lost foam casting is poised to play a significant role in shaping the future of precision metal casting.
Post time:Νοέ . 11, 2024 05:15
Next:Incorporating Sand into Resin for Enhanced Texture and Durability in Crafts