Iron Sand Casting A Historical and Modern Perspective
Iron sand casting is a fascinating process that has been utilized for centuries, marrying tradition with modern technology. At its core, this method involves shaping molten iron, derived from iron sand, into specific forms through various mold techniques. This process is not only efficient but also environmentally sustainable, making it an appealing choice for many manufacturers today.
Historically, the use of iron sand dates back to ancient civilizations. Japan, for instance, has a rich heritage of iron sand casting, particularly through the traditional method known as tatara. This ancient technique involved smelting iron sand in a clay furnace, producing a high-quality iron called tatara iron. Artisans would then utilize this iron for various applications, including tools and weaponry. The remnants of these practices can still be seen in the production of traditional Japanese swords, which are revered for their strength and beauty.
In modern manufacturing, iron sand casting has gained traction due to its versatility and cost-effectiveness. The process begins with the collection of iron-rich sand, often found on beaches or riverbeds. This sand contains high concentrations of iron oxides, which can be transformed into molten iron. The casting process generally involves creating a mold made from sand, metal, or other materials. Once the mold is prepared, molten iron is poured into it, allowing it to cool and solidify into the desired shape.
iron sand casting
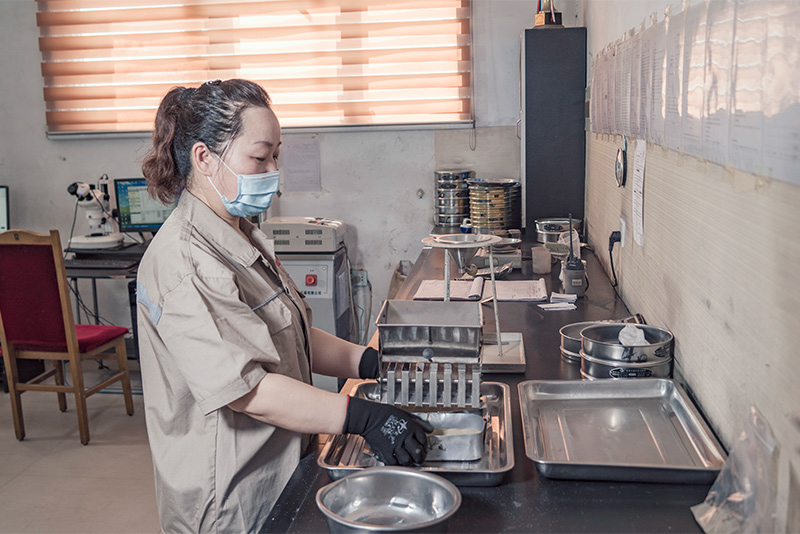
One of the significant advantages of iron sand casting is its ability to produce complex shapes with high accuracy. This makes it ideal for various industries, including automotive, aerospace, and construction. Additionally, the recycling aspect of iron sand is a notable benefit, as used sand can often be reused in the casting process, reducing waste and promoting sustainability.
However, like any manufacturing process, iron sand casting has its challenges. Controlling the quality of the iron and managing the cooling rates are critical to ensuring the final product meets specific standards. Advanced techniques such as computer-aided design (CAD) and simulation software have been integrated into the process to address these challenges, allowing for more precise molds and better quality control.
In conclusion, iron sand casting is a time-honored technique that continues to evolve in today’s technological landscape. Its historical significance, combined with modern innovations, ensures that it remains a relevant and effective method for producing high-quality metal components. As industries seek sustainable practices, the revival and enhancement of iron sand casting could play a vital role in the future of manufacturing, bridging the gap between ancient craftsmanship and contemporary engineering.
Post time:Οκτ . 31, 2024 15:51
Next:Effective Techniques for Smoothing Small 3D Prints for a Professional Finish