Furan Resin Sand Casting An Overview
Furan resin sand casting is a sophisticated and efficient method used in the production of metal components, especially when high precision and surface finishes are required. This technique employs furan resin, a phenolic resin derived from furfuryl alcohol, which serves as a binder in the creation of sand molds. With several advantages over traditional methods, furan resin sand casting has become increasingly popular in the manufacturing industry.
The Process
The furan resin sand casting process begins with the preparation of the sand mixture. The foundry sand, usually silica sand, is mixed with furan resin and a curing agent. This mixture is then shaped into a mold that has the negative impression of the desired component. The furan resin binds the sand particles together, allowing for intricate designs and configurations that can capture fine details.
Once the mold is formed, it is cured at room temperature or slightly elevated temperatures. The curing process is essential as it ensures that the mold maintains its shape and structural integrity. After curing, the mold halves are assembled, and molten metal is poured into the cavity. The properties of furan resin permit quicker curing times compared to other resin systems, which can lead to increased productivity in manufacturing.
Advantages of Furan Resin Sand Casting
1. High Dimensional Accuracy Furan resin provides excellent dimensional stability, which is crucial for applications requiring tight tolerances. This accuracy makes it suitable for intricate designs and complex geometries.
2. Excellent Surface Finish Components produced via furan resin sand casting exhibit superior surface quality. This characteristic minimizes the need for extensive post-casting finishing processes, saving time and reducing costs.
3. High Thermal Stability Furan resin can withstand high temperatures, making it ideal for casting metals with high melting points. This quality ensures that the mold retains its shape and integrity during the pouring of molten metals.
furan resin sand casting
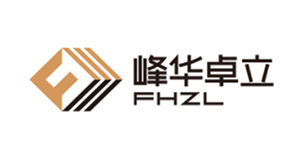
4. Reduced Environmental Impact Compared to traditional sand casting methods that use phenolic resins, furan resin casting generates fewer volatile organic compounds (VOCs). This aspect aligns with the increasing emphasis on sustainable production practices in the foundry industry.
5. Quick Turnaround The rapid curing time associated with furan resin allows for faster mold production, leading to shorter lead times and increased responsiveness to customer demands.
Applications
Furan resin sand casting is widely used in various industries, including automotive, aerospace, and heavy machinery. Applications commonly include engine components, turbine parts, and intricate housings that require precise tolerances and durability. The process is particularly beneficial in situations where custom and low-volume production runs are necessary.
Challenges and Considerations
Despite its many advantages, furan resin sand casting is not without challenges. The cost of furan resin tends to be higher than traditional sand-binding materials, which can impact the overall production costs. Additionally, foundries must ensure that their equipment is compatible with the specific curing and mixing requirements of the resin to avoid operational inefficiencies.
Conclusion
In conclusion, furan resin sand casting represents a significant advancement in casting technology, offering numerous benefits such as high dimensional accuracy, superior surface finishes, and quick turnaround times. As industries strive for higher efficiency and reduced environmental impact, this innovative casting method continues to gain traction. By harnessing the capabilities of furan resin, manufacturers can produce high-quality metal components tailored to the exacting demands of modern applications. As the foundry industry evolves, the role of furan resin sand casting will undoubtedly expand, driving further innovation and excellence in metal casting processes.
Post time:Δεκ . 19, 2024 18:10
Next:what type of sand is used for sand casting