Understanding Foundry Sand Its Meaning and Significance in Metal Casting
Foundry sand, a crucial element in the metal casting industry, plays an essential role in shaping the future of manufacturing. This specialized material is primarily composed of silica and is employed in various forms of casting processes to create metal parts and components. The quality, composition, and characteristics of foundry sand directly influence the outcomes of metal casting, making it essential to understand its meaning and applications.
At its core, foundry sand is used as a mold material in the casting process. When molten metal is poured into sand molds, it takes the shape of the cavity created by the sand, resulting in a solidified piece that can be further machined or treated as needed. Foundry sand is typically fine-grained and allows for excellent mold-making properties and dimensional accuracy, which are critical for ensuring that the final product meets required specifications.
Understanding Foundry Sand Its Meaning and Significance in Metal Casting
One of the key benefits of foundry sand is its recyclability. After the casting process, sand can often be reclaimed and reused, making it an environmentally friendly option in the manufacturing process. The recycling process involves removing any adhered materials, screening the sand, and preparing it for future use. This not only reduces waste but also lowers costs associated with raw material procurement, making foundry sand a sustainable choice for many foundries.
foundry sand meaning
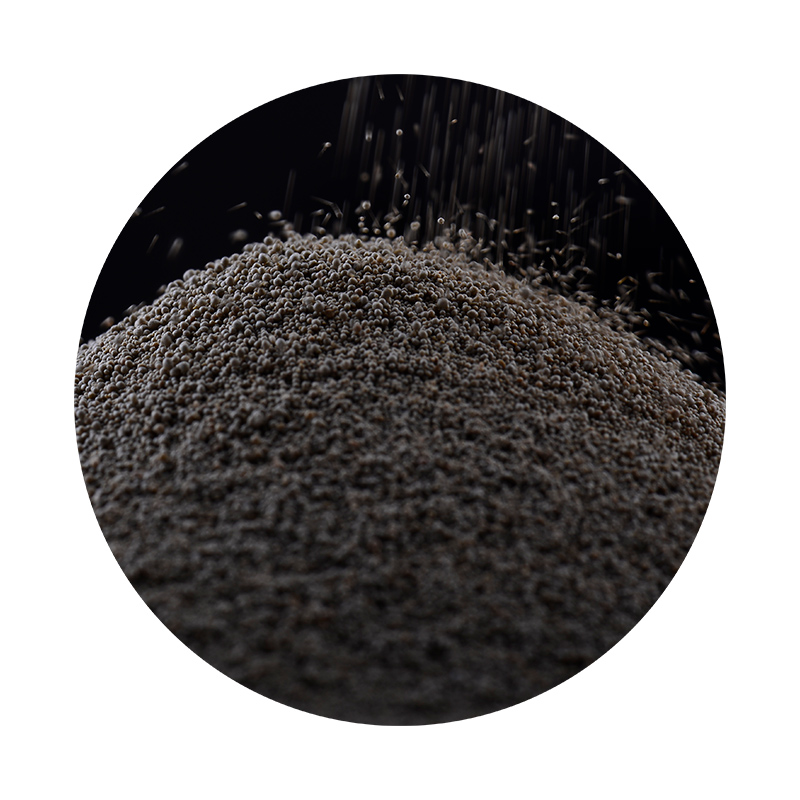
The effectiveness of foundry sand also hinges on its casting method. Different casting techniques, such as green sand casting, resin sand casting, and lost foam casting, utilize distinct types of foundry sand. Green sand, which is a mixture of sand, clay, and water, is widely used due to its flexibility and moisture content, which helps in forming molds. On the other hand, resin sand incorporates chemical binders that harden when heated, providing enhanced dimensional accuracy and surface finish for precision components.
Understanding the specific requirements of each casting application is vital for selecting the right type of foundry sand. Factors such as the type of metal being cast, desired surface finish, and dimensional tolerances play a significant role in determining the appropriate sand composition and grain size. Furthermore, certain industries may require unique properties, such as resistance to specific chemicals or high-temperature stability, prompting foundries to conduct thorough research and development in their material selection.
Foundry sand's significance extends beyond the technical aspects; it also contributes to the overall economy and job market. The casting industry, supported by the effective use of foundry sand, provides numerous employment opportunities in manufacturing, engineering, and research and development. As industries grow and evolve, the demand for high-quality foundry sand continues to increase, driving innovation in sand processing and application techniques.
In summary, foundry sand is not merely a raw material but a fundamental component that influences the efficiency and effectiveness of the metal casting process. Its unique properties, recyclability, and adaptability to various casting methods make it invaluable to the manufacturing sector. As we advance into a future where precision and sustainability are key, a deeper understanding of foundry sand's meaning and applications will continue to support the industry's growth and innovation. Whether in automotive, aerospace, or machinery, foundry sand remains an indispensable material in the journey from raw metal to finished product.
Post time:Νοέ . 27, 2024 12:48
Next:Understanding the Density Characteristics of Foundry Sand for Optimal Casting Performance