Foundry Sand Composition A Key Element in Metal Casting
The foundry industry plays a pivotal role in manufacturing a wide range of metal components used in various applications, from automotive parts to intricate machinery. At the heart of this industry lies a fundamental material foundry sand. The composition of foundry sand significantly influences the quality of the final castings, making it a crucial element in ensuring the integrity of the metal products produced.
Understanding Foundry Sand
Foundry sand is a crucial material used in the metal casting process, primarily for creating molds and cores. This sand needs to possess specific properties to withstand the rigors of metal casting, including high temperatures, mechanical stress, and chemical reactions that occur during the pouring of molten metal. The most commonly used type of foundry sand is silica sand, known for its high thermal stability and resistance to deformation under heat. However, other types of sand may also be utilized depending on the specific requirements of the casting process.
Key Components of Foundry Sand
The composition of foundry sand can vary based on the casting method and the type of metal being used. However, several key components are consistently found across different types of foundry sand. These include
1. Silica (SiO2) The primary component of most foundry sands, silica provides the essential structure and stability required for mold making. The shape, size, and distribution of silica particles can significantly affect the mold's permeability and strength.
2. Clay Clay is often added to enhance the binding properties of the sand. It helps in holding the sand grains together, providing strength to the molds. Common clays used in foundry sand include bentonite, which offers excellent bonding capabilities and thermal stability.
foundry sand composition
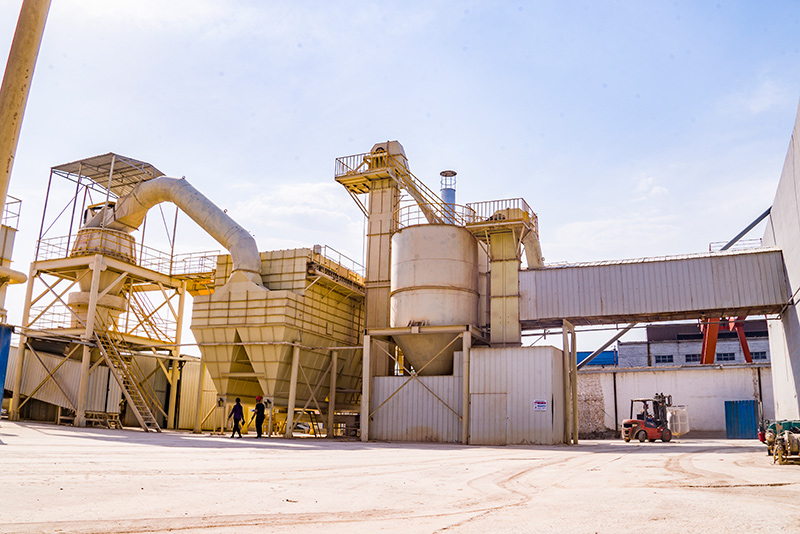
3. Water Water is crucial in the foundry sand mixture as it aids the clay in binding the silica grains together. The moisture content must be carefully controlled, as too much water can lead to casting defects, while too little can make the mold weak.
4. Additives Various additives may be incorporated into foundry sand for specific purposes. These can include synthetic resins that enhance mold strength, coloring agents for visual identification, and agents that help reduce slag formation during casting.
The Role of Grain Shape and Size
The grain shape and size of foundry sand are critical factors in determining the mold's performance. Angular grains provide better interlocking and strength, while rounded grains offer improved flowability and compaction. Uniform grain size contributes to optimal permeability, allowing gases to escape during the casting process, which is essential in preventing defects such as blowholes.
Recycling Foundry Sand
One of the significant trends in the foundry industry is the recycling of used foundry sand. Used sand can be treated and reused in the casting process, leading to cost savings and reduced environmental impact. However, the composition of recycled sand may change, and it is essential to analyze its properties to determine its suitability for future casting applications.
Conclusion
In conclusion, the composition of foundry sand is a fundamental aspect of the metal casting process. It directly influences the quality, strength, and integrity of the final products. By carefully selecting and controlling the components of foundry sand, manufacturers can optimize their production processes and ensure that they meet the stringent demands of various industries. As the foundry industry continues to evolve, ongoing research and development into sand compositions and recycling methods will play an increasingly important role in enhancing sustainability and efficiency in metal casting. Understanding the complexities of foundry sand composition is essential for any manufacturer aiming to achieve excellence in casting quality and performance.
Post time:Νοέ . 06, 2024 02:07
Next:sand casting foundries