Different Types of Sand Casting
Sand casting is one of the oldest and most widely used metal casting processes. It involves the formation of a mold through the use of sand, which is then filled with molten metal to create a desired part or component. This versatile method is favored for its ability to produce complex shapes with intricate details. There are several different types of sand casting processes, each with its unique characteristics and applications.
Different Types of Sand Casting
Another popular method is dry sand casting. In this process, the sand is mixed with a binding agent and heated to create a hard mold. Unlike green sand, dry sand offers greater strength and stability, which is essential for producing large or intricate parts. This method minimizes the risk of distortion during the casting process and enables better surface finishes. Dry sand casting is particularly advantageous for high-precision applications and is often utilized in industries requiring high-quality components.
different types of sand casting
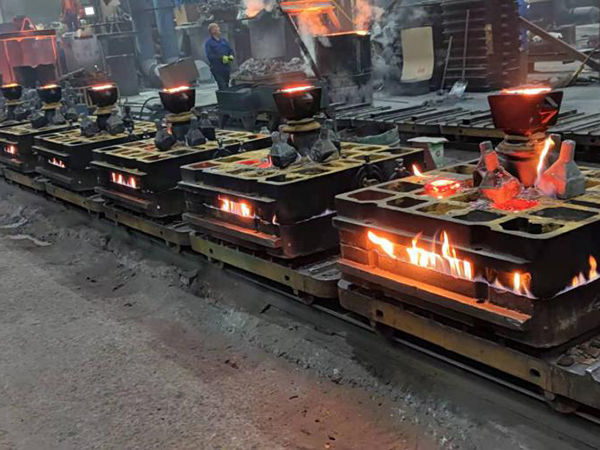
Cold box sand casting is another variation that allows for more efficient mold-making. In this technique, the sand mixture is compacted using a chemical binder that cures at room temperature. This aspires to reduce the need for additional drying time and results in harder molds. Cold box sand casting is often employed in high-volume production runs and is known for its ability to produce complex geometries with exceptional detail.
Shell molding is also a noteworthy type of sand casting that uses a thin shell of sand to create molds. This process relies on a thermosetting resin bonded sand that is heated to form a rigid shell around a metal pattern. Shell molding is known for its excellent dimensional accuracy and smooth surface finish, making it ideal for applications where precision is critical. While it can be more expensive than traditional sand casting methods, the benefits it offers in terms of finishing quality and detail often outweigh the costs.
Lastly, lost foam casting is an innovative approach that uses a foam pattern which is vaporized upon the introduction of molten metal into the mold. This process eliminates the need for cores and allows for the production of highly intricate shapes. Lost foam casting is particularly suited for low to medium production volumes and is favored in industries such as automotive and aerospace for manufacturing complex components.
In conclusion, sand casting encompasses various methods, each with its strengths and applications. From green sand casting's cost-effectiveness to the precision of shell molding and the innovative techniques of lost foam casting, manufacturers can choose the most suitable process based on their specific needs. As technology advances, these methods continue to evolve, ensuring that sand casting remains a vital part of modern manufacturing.
Post time:Οκτ . 08, 2024 18:57
Next:zandgietijzer