Difference Between Sand Casting and Die Casting
Casting is a manufacturing process where liquid metal is poured into a mold to create a component with a desired shape. Two of the most widely used casting methods are sand casting and die casting. While both processes aim to achieve similar results, they differ significantly in terms of methodology, materials, costs, and applications.
Sand Casting Overview
Sand casting is a traditional casting method that uses a sand-based mold. The process begins with creating a mold from a pattern, which is typically made out of metal or wood. The sand mold is formed by compacting sand around the pattern. Once the mold is ready, liquid metal is poured into the cavity. After the metal has solidified, the mold is broken away to reveal the finished product.
One of the main advantages of sand casting is its versatility. It can accommodate a wide range of metals, including ferrous and non-ferrous materials. Additionally, sand casting can produce large and complex parts, making it suitable for a variety of industries, from automotive to aerospace. However, the surface finish of sand-cast parts is generally rougher compared to those made using die casting, often requiring further machining.
Die Casting Overview
Die casting, on the other hand, involves injecting molten metal under high pressure into a steel mold, or die. This process provides a high degree of precision and allows for very intricate designs. While die casting is typically limited to non-ferrous metals, such as aluminum, zinc, and magnesium, it excels in producing a high quantity of parts with exceptional surface finishes and dimensional accuracy.
Die casting can be further categorized into two types hot chamber and cold chamber, each offering distinct advantages based on the type of metal used and the specific application. The fast production cycle and the reduced need for secondary operations make die casting a cost-effective choice for high-volume production.
difference between sand casting and die casting
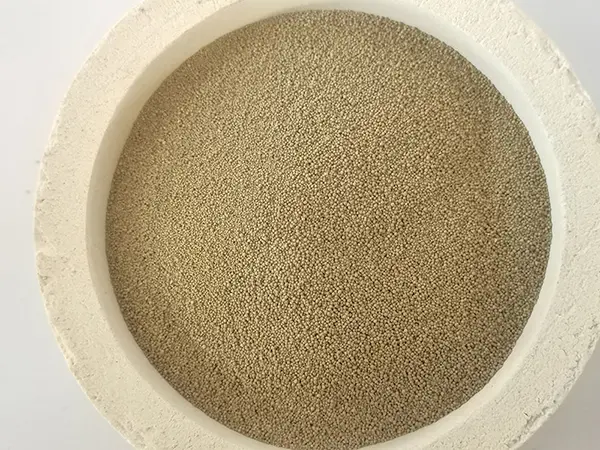
Key Differences
2. Production Speed and Cost Die casting typically offers faster production rates due to its automated nature, making it more economical for large volumes. In contrast, sand casting has a longer lead time and is generally more labor-intensive.
3. Surface Finish and Tolerances Parts produced via die casting have better surface finishes and tighter tolerances compared to sand cast parts, which often require additional machining for a smoother finish.
4. Mold Creation Sand casting uses relatively inexpensive materials for mold creation, allowing for easy modifications. Die casting molds are more expensive and time-consuming to create but offer better durability and reusability.
5. Applications Due to the above factors, sand casting is often used for low-volume, complex parts, particularly where material costs are a factor. Conversely, die casting is ideal for high-volume production runs where precision and surface quality are critical, such as in automotive and electronics.
Conclusion
In summary, both sand casting and die casting have unique advantages and disadvantages, making them suitable for different applications. Understanding these differences can help manufacturers choose the right casting method to meet their specific needs, ensuring optimal quality and cost-effectiveness in their production processes. Ultimately, the choice between sand casting and die casting will depend on factors such as production volume, material type, and desired finish quality.
Post time:Σεπ . 13, 2024 04:14
Next:sand used for sand casting