Coated Sand Casting A Detailed Overview
Coated sand casting is an advanced casting technique that combines traditional sand casting with innovative coating technologies. This method not only enhances the quality of the castings produced but also offers increased efficiency and versatility for manufacturers across industries. In this article, we will explore the fundamentals of coated sand casting, its process, benefits, applications, and future trends.
The Basics of Sand Casting
Sand casting, one of the oldest and most widely used metal casting processes, involves creating a mold from a mixture of sand, clay, and water. The mold is formed by compacting this mixture around a pattern of the object to be cast. Once the mold is prepared, molten metal is poured into the cavity, allowed to cool, and solidify before the mold is broken open to retrieve the finished casting.
While conventional sand casting is robust and cost-effective, it has its limitations. Defects such as poor surface finish, dimensional inaccuracies, and inadequate mechanical properties can arise due to the physical characteristics of the sand itself. This is where coated sand casting comes into play.
What is Coated Sand Casting?
Coated sand casting involves the application of a coating material onto the surface of the sand grains before they are used to form the mold. This coating is typically made from resin or other bonding agents that enhance the sand's properties. The primary purpose of the coating is to improve the sand's strength, thermal stability, and dimensional accuracy, leading to better overall casting quality.
The coated sand casting process incorporates several key steps
1. Coating Preparation The sand is treated with a coating material to create a uniform coating around each sand grain. This process can be done through various methods, such as mixing, spraying, or fluidized bed coating.
2. Mold Formation Once the sand is coated, it is packed around the pattern to form the mold. The coated sand exhibits increased strength compared to uncoated sand, allowing for the creation of more intricate designs and thinner walls.
3. Curing The coated sand mold is cured using heat or chemical catalysts, solidifying the coating and reinforcing the mold's structure.
4. Metal Pouring After curing, molten metal is poured into the mold cavity. The thermal stability of the coated sand ensures that the mold maintains its integrity under high temperatures.
5. Casting Retrieval Once the metal has cooled and solidified, the mold is broken apart to retrieve the finished casting.
Benefits of Coated Sand Casting
Coated sand casting offers numerous advantages over traditional sand casting methods
coated sand casting
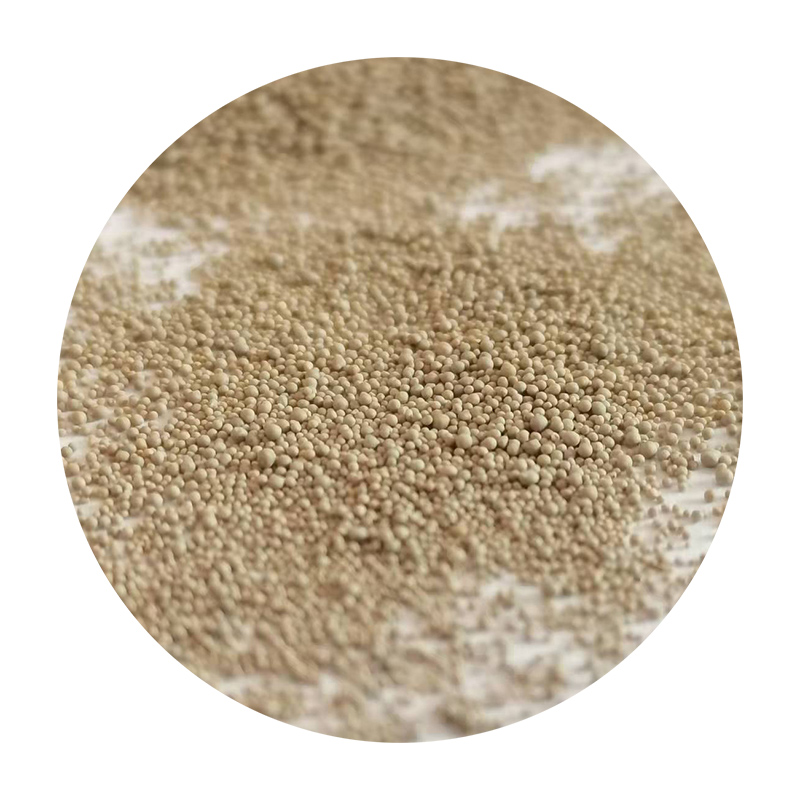
- Improved Surface Finish The coated sand results in a smoother surface on the final castings, reducing the need for extensive post-processing.
- Enhanced Dimensional Accuracy The improved mold strength and stability lead to more precise dimensions, allowing for tighter tolerance controls
.- Reduced Defects The application of coatings minimizes the occurrence of defects such as sand-related inclusions, resulting in higher quality cast parts.
- Increased Design Flexibility Manufacturers can create more complex shapes and finer details with coated sand casting, making it suitable for a wide range of applications.
Applications of Coated Sand Casting
Coated sand casting is widely utilized in various industries. Some of the most common applications include
- Automotive Parts Engine blocks, cylinder heads, and other components benefit from the precision and quality afforded by coated sand casting.
- Aerospace Components High-performance parts requiring stringent tolerances and excellent surface finishes are often produced using this method.
- Industrial Machinery Large castings for heavy equipment and machinery can be efficiently manufactured with coated sand casting.
Future Trends
As technology continues to advance, the coated sand casting process is expected to evolve further. Innovations in coating materials, automation in mold preparation, and enhanced simulation technologies will likely contribute to the efficiency and sustainability of coated sand casting operations.
Moreover, with the growing demand for lightweight and complex designs in various industries, coated sand casting may see increased adoption as manufacturers seek to leverage its benefits.
Conclusion
Coated sand casting is redefining the landscape of metal casting through its innovative approach to enhancing traditional sand casting methods. With its ability to produce high-quality castings with improved surface finishes and dimensional accuracy, coated sand casting stands out as a vital technique for meeting the demands of modern industries. As advancements continue, this method will undoubtedly play a crucial role in the future of manufacturing.
Post time:Δεκ . 11, 2024 03:11
Next:cheap sand casting