The Art and Science of Ceramic Sand Casting
Ceramic sand casting is an innovative and efficient method used in the manufacturing industry for creating intricate metal parts and components. This process stands out for its ability to produce high-quality castings with excellent surface finishes and dimensional accuracy. As industries seek ways to enhance efficiency and reduce costs, ceramic sand casting has emerged as a preferred choice for many applications.
Understanding Ceramic Sand Casting
At its core, ceramic sand casting involves using a mixture of ceramic materials and sand as the mold medium. Unlike traditional green sand molds, ceramic sand molds are more stable and can withstand higher temperatures, making them suitable for casting metals with melting points exceeding those of conventional materials. Ceramic sand, primarily composed of silica and other ceramic additives, offers superior thermal resistance and lower thermal expansion rates, contributing to improved casting precision.
The basic process of ceramic sand casting begins with the preparation of a pattern, which is a replica of the final product. The pattern is typically made from metal or a durable polymer and is used to create a mold. The ceramic sand is then mixed with a bonding agent, often a resin, to allow the sand particles to adhere to each other and form a solid structure once cured. After the mold is formed around the pattern, it is heated to harden, creating a strong shell.
Advantages of Ceramic Sand Casting
One of the primary advantages of ceramic sand casting is its capability to produce highly detailed and complex geometries with precision. This is particularly beneficial in industries such as aerospace, automotive, and energy, where components often require intricate designs to meet strict regulatory and performance standards. The fine granulation of ceramic sand allows for a smooth surface finish, reducing the need for extensive post-casting machining and finishing processes.
Another significant benefit is durability. Ceramic sand molds can be reused multiple times, enhancing the sustainability of the casting process. This not only reduces material waste but also lowers production costs over time as manufacturers do not need to create new molds for each casting cycle.
ceramic sand casting
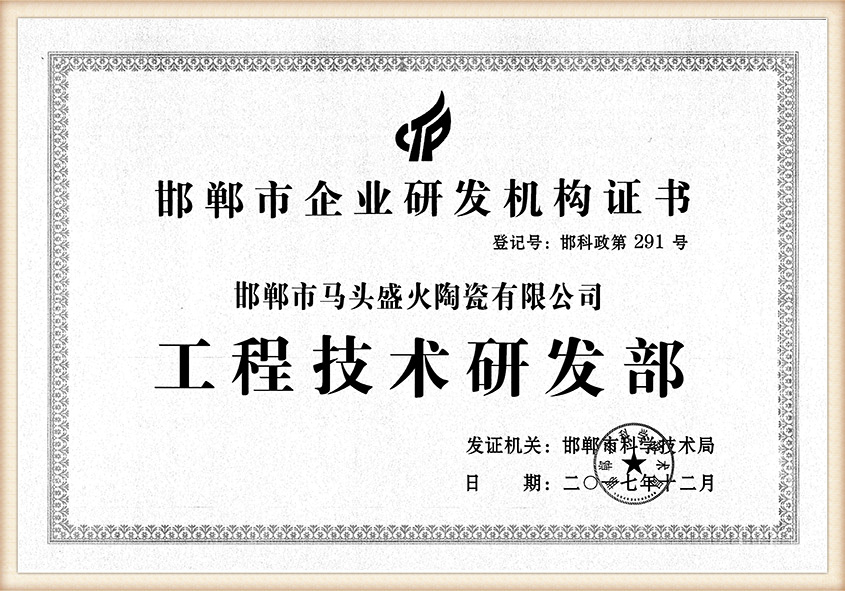
Moreover, ceramic sand casting is highly adaptable, allowing manufacturers to cast a wide range of metals, including aluminum, iron, and alloys
. This versatility makes it an attractive option for companies looking to streamline their production processes and expand their capabilities.Applications of Ceramic Sand Casting
The applications of ceramic sand casting are vast and varied. In the aerospace industry, it is used to produce components such as turbine blades and casings, where strength-to-weight ratios and temperature resistance are critical. The automotive sector utilizes it for producing engine components, housing, and other parts that must withstand high stress and thermal conditions.
In the realm of energy, ceramic sand casting is essential for creating parts used in gas and steam turbines, ensuring efficient energy conversion processes. Additionally, it is increasingly being used in the medical field for manufacturing surgical instruments and implants, where precision and biocompatibility are paramount.
Challenges and Future Outlook
While ceramic sand casting has numerous advantages, it is essential to acknowledge the challenges it faces. The initial setup costs and investment in specialized equipment can be significant, which may deter smaller manufacturers. Moreover, the process requires skilled workers to handle the complexities of mold preparation and metal pouring, along with stringent quality control measures.
Looking forward, the future of ceramic sand casting appears promising. Advancements in technology, such as the integration of automation and AI-driven quality assurance systems, are likely to streamline the process further while reducing costs. As industries continue to prioritize sustainability and efficiency, the demand for innovative casting methods like ceramic sand casting is expected to grow.
In conclusion, ceramic sand casting stands as a testament to the intersection of tradition and innovation in manufacturing. Its unique properties and adaptability make it a vital part of modern production, driving advancements across various industries while meeting the ever-evolving demands of the market. As technology advances, the potential for ceramic sand casting will only become greater, solidifying its status as a key player in the manufacturing landscape.
Post time:Νοέ . 27, 2024 06:55
Next:Types of Sand Used in Sand Casting Processes and Their Characteristics