The Rise of 3D Sand Printing in Casting Revolutionizing Manufacturing Processes
In recent years, the manufacturing industry has witnessed a transformative evolution through the integration of advanced technologies. One notable innovation is 3D sand printing, which has emerged as a game-changer in the field of casting. This revolutionary technique combines the advantages of 3D printing with traditional sand casting methods, offering numerous benefits that drive efficiency, reduce costs, and enhance the overall quality of final products.
Traditionally, sand casting has been a staple method for producing metal parts. It involves creating a mold from a mixture of sand and a binding agent, where molten metal is poured to create the final product. While effective, this process often faces limitations such as long lead times for mold production, high material waste, and difficulties in achieving complex geometries. However, 3D sand printing addresses these issues head-on by introducing a layer-by-layer additive manufacturing approach that allows for more intricate designs and faster production times.
The Rise of 3D Sand Printing in Casting Revolutionizing Manufacturing Processes
Moreover, the efficiency of the 3D sand printing process significantly reduces lead times. Traditional mold production can take days or even weeks, depending on the complexity and size of the mold. In contrast, 3D sand printers can create molds in a matter of hours, enabling manufacturers to respond quickly to market demands and minimize turnaround times for production. This rapid prototyping capability also allows for iterative design changes, facilitating a more agile and innovative manufacturing process.
3d sand printing casting
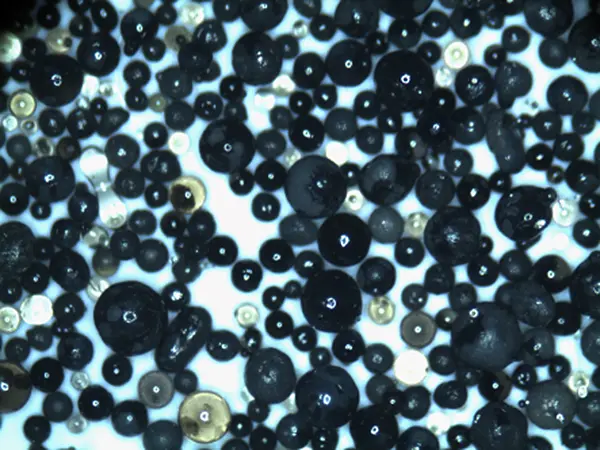
Another key benefit of 3D sand printing is its material efficiency. Traditional sand casting often results in a significant amount of waste, as excess material needs to be removed from the mold after casting. With 3D sand printing, the process is streamlined, as only the necessary material is used to create the mold. This reduction in waste not only lowers production costs but also contributes to more sustainable manufacturing practices, which is becoming increasingly important in today’s eco-conscious market.
In addition to its efficiency and sustainability, 3D sand printing enhances the consistency and quality of cast parts. Traditional sand casting can result in variations in mold quality due to human error or inconsistencies in the sand mixture. However, 3D sand printers use precise digital designs, ensuring that each mold produced is identical and meets stringent quality standards. This reliability translates into higher-quality cast parts with improved mechanical properties, leading to better performance in their respective applications.
As the adoption of 3D sand printing technology continues to grow, we see a shift in the competitive landscape of manufacturing. Companies that embrace this technology gain a significant edge by offering faster production times, reduced material costs, and the ability to create intricate designs. The potential for innovations in product design and functionality is expanding, unlocking new possibilities across various industries.
In conclusion, 3D sand printing is revolutionizing the casting process by combining traditional methods with cutting-edge technology. With its capacity for complexity, efficiency, and sustainability, this innovative technique is poised to redefine manufacturing standards and practices. As industries seek to enhance productivity and maintain competitive advantages, 3D sand printing will play an increasingly vital role in shaping the future of manufacturing, making it an exciting area to watch in the coming years.
Post time:Δεκ . 05, 2024 03:51
Next:Tips for Properly Sanding Ceramic Surfaces for a Smooth Finish