The Advantages and Innovations in Sand Casting Unveiling the Future of Manufacturing
In the realm of manufacturing, sand casting has stood the test of time as one of the oldest and most versatile casting methods. This technique, which dates back thousands of years, is still widely utilized today due to its numerous advantages and the innovations that continue to enhance its effectiveness. As we delve into the world of sand casting companies, it becomes clear why this method remains a cornerstone in the production of metal components across various industries.
Understanding Sand Casting
Sand casting involves creating a mold from a pattern made of metal, wood, or plastic, which is then filled with molten metal to form the desired component. The process begins with the creation of a sand mold, typically comprising a mixture of sand, clay, and water. This mixture is packed around the pattern, creating a negative impression. Once the mold is prepared, the pattern is removed, leaving a cavity into which molten metal is poured.
Benefits of Sand Casting
One of the primary advantages of sand casting is its versatility. It can accommodate a wide range of materials, including aluminum, bronze, iron, and magnesium. This flexibility makes it an ideal choice for producing both simple and complex shapes. Sand casting is particularly advantageous for low to medium production volumes, enabling manufacturers to create unique designs without the prohibitive costs associated with other casting methods.
Another significant benefit is the ability to produce large components. Unlike investment casting or die casting, which are often limited by the size of the molds, sand casting can create exceptionally large parts, making it essential for industries like automotive and aerospace, where large engine components are required.
Moreover, the costs associated with sand casting are generally lower than those of other methods. The materials used for sand molds are inexpensive, and the process does not require elaborate machinery. This cost-effectiveness allows manufacturers to produce high-quality components without stretching their budgets.
sand casting company
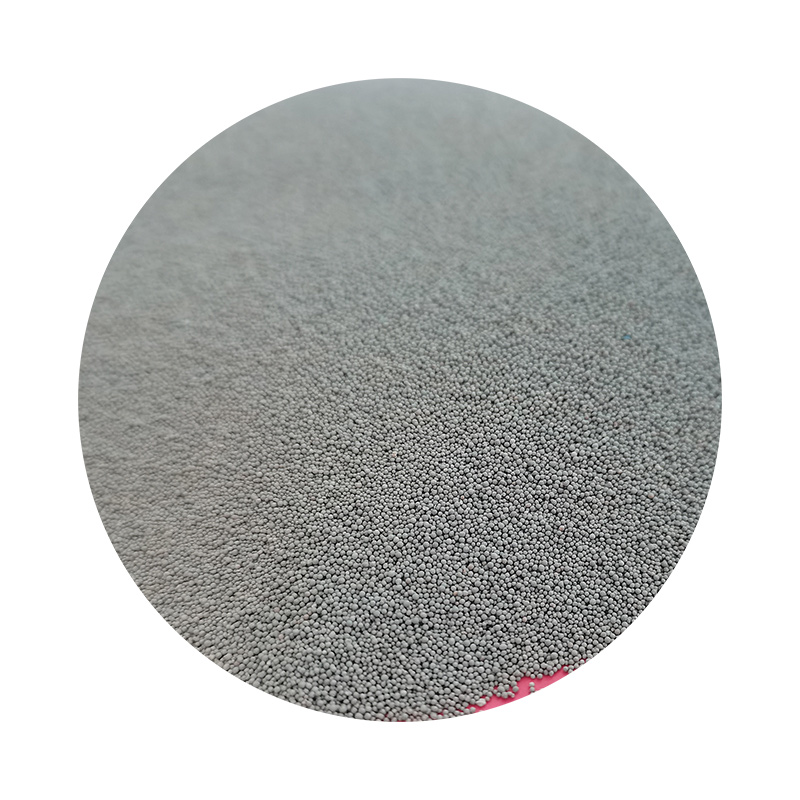
Innovations in Sand Casting
While traditional sand casting techniques have remained largely unchanged for years, technological advancements are significantly enhancing the process’s efficiency and precision. One of these innovations includes the development of computer numerical control (CNC) technology, which allows for more precise mold-making and pattern creation. This technology reduces manual labor and minimizes errors, leading to higher quality casts.
3D printing is another groundbreaking development impacting the sand casting industry. This technology allows manufacturers to create sand molds directly from digital designs, streamlining the production process. 3D-printed molds can reduce lead times and allow for greater customization, meeting the varying demands of modern manufacturing.
Additionally, advancements in materials science have led to the development of new types of sand mixtures that improve mold strength and reduce defects in the final castings. Techniques such as lost foam casting, which integrates foam patterns into the sand casting process, are also being explored, offering the potential for enhanced precision and reduced waste.
Conclusion
As we look towards the future, sand casting companies are poised to play a vital role in the manufacturing landscape. The combination of traditional techniques with modern technology is redefining the possibilities of what can be achieved through sand casting. By embracing these innovations, manufacturers can produce high-quality, cost-effective components that meet the demands of a rapidly evolving market.
In summary, sand casting remains a foundational method in manufacturing, characterized by its versatility, cost-effectiveness, and capacity for producing large components. As technology continues to advance, the sand casting industry is set to thrive, further solidifying its place as an essential method for creating metal components in various applications. This blend of tradition and innovation reaffirms the potential of sand casting to adapt and flourish in the face of changing industrial needs.
Post time:Okt . 22, 2024 13:47
Next:Exploring the Potential of 3D Printing with Wet Sand for Innovative Designs