Sand Casting Metal An Integral Process in Metal Fabrication
Sand casting is one of the oldest and most versatile techniques used in the metal fabrication industry. This method involves creating a mold from sand, which is then used to cast molten metal into the desired shape. The process is celebrated for its simplicity, cost-effectiveness, and ability to create complex shapes, making it a preferred choice for manufacturers around the globe.
At its core, sand casting involves several key steps. First, a pattern is created, typically from wood or metal, to represent the final product. This pattern is then placed into a mold made from a mixture of sand and a bonding agent, usually clay or resin. The sand is compacted around the pattern to create a mold cavity. Once the mold is prepared, the pattern is removed, leaving behind an impression that matches the shape of the final component.
Sand Casting Metal An Integral Process in Metal Fabrication
After the metal is molten, it is carefully poured into the mold cavity through a system of channels known as gates. This stage requires precision, as improper pouring can lead to defects such as air pockets or uneven surfaces. Once the molten metal fills the mold and cools, it solidifies into the shape of the intended part.
sand casting metal
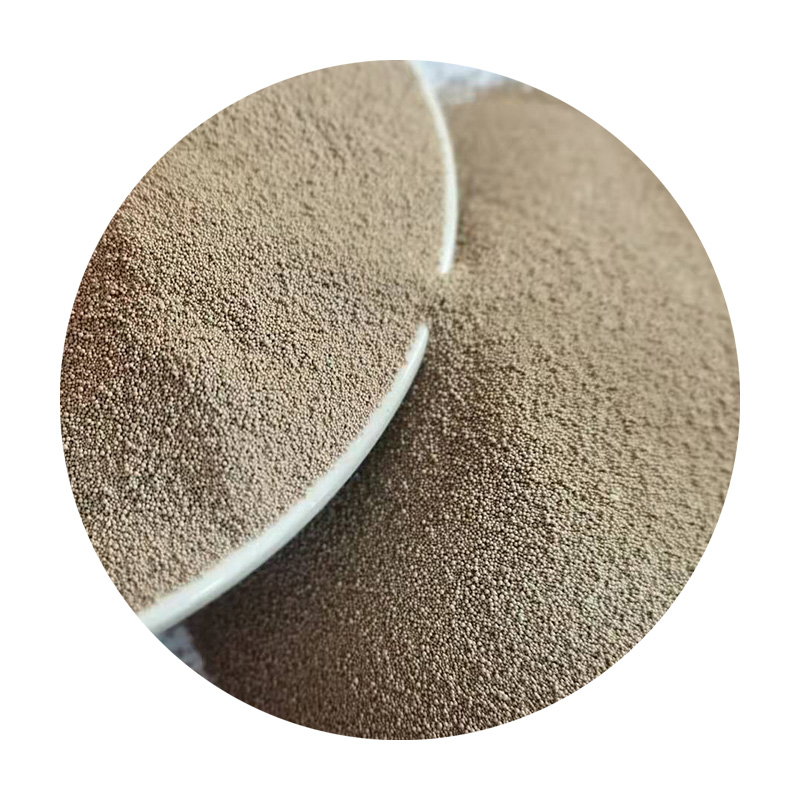
After cooling, the solidified casting is removed from the mold. This process may involve breaking the sand mold apart or using vibration to shake out the casting. The casting is then cleaned of any residual sand, and further finishing operations, such as machining, grinding, or polishing, may be performed to achieve the desired specifications.
One of the significant advantages of sand casting is its ability to produce large parts with minimal limitations on size and shape. This is particularly beneficial in industries such as automotive, aerospace, and manufacturing, where unique and large-scale components are often required. Furthermore, sand casting can be adapted for both small quantities of custom parts and mass production, making it a flexible solution for various manufacturing needs.
However, it is not without challenges. The sand casting process can be susceptible to defects, including shrinkage and surface imperfections, which may require additional machining or finishing. Moreover, controlling the temperature and timing during pouring is vital to minimize these imperfections.
In conclusion, sand casting metal remains a fundamental method in the engineering and manufacturing sectors due to its adaptability and cost-effectiveness. As technology continues to advance, improvements in materials and processes promise to enhance the quality and efficiency of sand casting, ensuring its relevance in the future of metal fabrication. Whether for producing intricate components or large industrial parts, sand casting offers a reliable solution that has stood the test of time.
Post time:Sep . 04, 2024 09:00
Next:physical properties of foundry sand