An Overview of Foundry Sand Suppliers Meeting Industry Needs
Foundry sand plays a pivotal role in the casting process, where molten metal is poured into molds to create various metal components, ranging from automotive parts to intricate machinery. The quality of castings depends significantly on the type and quality of sand used, making foundry sand suppliers crucial to the manufacturing sector. This article explores the role of foundry sand suppliers, the types of sand they offer, and the importance of choosing the right supplier.
Understanding Foundry Sand
Foundry sand is a specially graded silica sand that has excellent properties for producing molds and cores in metal casting. The primary characteristics that make this sand ideal for foundries include its thermal stability, high permeability, and ability to withstand the rigors of the casting process. The most common types of foundry sand include
1. Silica Sand This is the most widely used foundry sand, obtained from deposits of quartz or sandstone. Silica sand has excellent molding properties, making it suitable for various applications.
2. Synthetic Sand Created from a mixture of inorganic materials, synthetic sand can be engineered to have specific properties tailored to particular casting applications.
3. Resin-coated Sand This type of sand is coated with a thermosetting resin, which provides better strength and allows for the creation of finer mold details. It is often used for high-precision casting processes.
4. Recycled Sand An environmentally friendly option, recycled sand is processed used sand that has been cleaned and reused for casting. This type of sand can significantly reduce material costs and waste.
The Role of Foundry Sand Suppliers
Foundry sand suppliers serve as a bridge between the sand producers and the foundries that utilize the material. They typically offer a comprehensive range of services that include
- Sourcing High-Quality Sand Suppliers are responsible for procuring sand from reliable sources, ensuring that it meets industry standards and specific requirements of various foundries.
- Customization Many suppliers provide customized sand solutions tailored to the unique needs of their clients. This can involve blending different sand types or adjusting properties to improve casting efficiency.
foundry sand suppliers
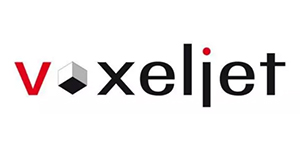
- Logistics and Supply Chain Management Foundry sand suppliers manage the logistics of transporting sand from production sites to foundries, ensuring timely delivery and minimizing downtime for their clients.
- Technical Support Suppliers also provide technical assistance, helping foundries select the right sand for their specific applications and offering guidance on best practices for sand usage.
The Importance of Selecting the Right Supplier
Choosing the right foundry sand supplier is critical for foundries looking to optimize their production processes. The following factors should be considered when selecting a supplier
1. Quality Assurance The supplier should have rigorous quality control measures in place to ensure that the sand meets industry specifications.
2. Experience and Reputation A supplier with a history of reliability and strong relationships with foundries can provide assurance of their capabilities.
3. Service Flexibility The ability to adjust to changing needs, such as varying quantities or the introduction of new sand types, is vital for foundries that operate in a dynamic environment.
4. Sustainability Practices As the industry moves towards more sustainable practices, suppliers that offer recycled sand options or environmentally friendly sourcing methods should be prioritized.
5. Technical Expertise Suppliers with a knowledgeable team can provide added value through advice and recommendations, which can significantly impact the casting process's efficiency and quality.
Conclusion
The foundry industry relies heavily on the expertise and resources of foundry sand suppliers. As the demand for high-quality casting continues to grow, these suppliers play an essential role in ensuring that foundries have access to the right materials for their operations. By prioritizing quality, flexibility, and technical support, foundry sand suppliers contribute significantly to the overall success of metal casting processes. For foundries looking to enhance their production capabilities, establishing a strong partnership with a reliable sand supplier is a critical step toward achieving operational excellence.
Post time:Dez . 26, 2024 04:12
Next:sanded resin