Types of Sand Used in Sand Casting
Sand casting is a widely used metal casting process that involves pouring molten metal into a mold that is formed from sand. It is not only economical and versatile but also allows for intricate designs to be achieved. One of the essential components of sand casting is the type of sand used, which significantly impacts the quality of the final product. This article explores the various types of sand utilized in the sand casting process, their properties, advantages, and applications.
1. Silica Sand
Silica sand, primarily composed of silicon dioxide (SiO2), is the most commonly used sand in the casting process. With its excellent thermal stability and ability to withstand high temperatures, silica sand is ideal for casting ferrous metals. Its coarse grain structure allows for good mold strength and durability. Silica sand is also relatively inexpensive and readily available, making it a cost-effective choice for manufacturers.
However, while it provides excellent casting quality, silica sand can become hazardous due to the release of crystalline silica dust. This has led to stricter regulations regarding worker safety and environmental impact. To mitigate these risks, many foundries employ proper dust control measures and personal protective equipment (PPE).
2. Green Sand
Green sand is a mixture of silica sand, clay, and water, which gives it its characteristic green color. The clay content acts as a binding agent, enhancing the mold's strength when mixed with water. Green sand is renowned for its ability to retain moisture, making it easy to shape and work with. It is especially beneficial for producing complex shapes and fine details.
Due to its excellent flowability and thermal properties, green sand is favored in the automotive and machinery industries. However, its moisture content must be closely monitored; too much water can lead to casting defects, while too little can weaken the mold.
3. Resin Sand
Resin sand, also known as resin-bonded sand, incorporates a thermal-setting resin as a binder. This type of sand is gaining popularity due to its superior strength, finer surface finish, and ability to produce more intricate patterns compared to traditional sands. Resin sand casting offers excellent dimensional accuracy, making it suitable for producing high-quality components.
types of sand used in sand casting
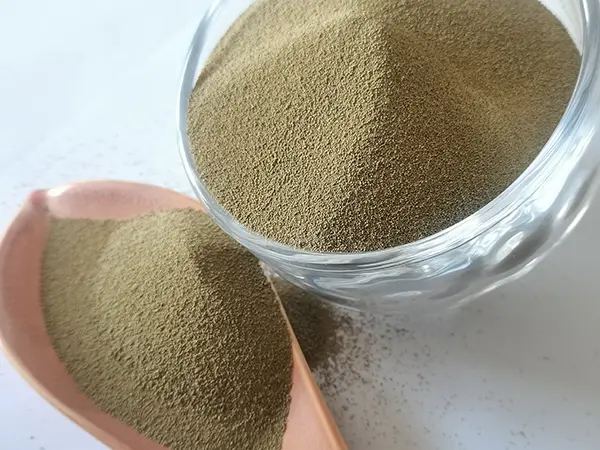
The primary disadvantage of resin sand is its cost; the resin is more expensive than clay, which can increase production costs. Additionally, working with resin sands requires careful management of curing times and temperatures. However, for high-value products where precision is critical, the benefits often outweigh the costs.
4. Chromite Sand
Chromite sand is composed of chromite, a mineral that contributes to its high melting point and resistance to thermal shock. Due to its exceptional performance under high temperatures, chromite sand is typically used for casting ferrous metals and applications where high-quality surfaces are required.
The use of chromite sand is particularly advantageous in processes that demand better conductivity and lesser expansion rates. It also minimizes mold erosion, resulting in reduced inclusion defects in castings. However, chromite sand is relatively expensive, and its usage may be limited to specific applications where its properties provide a distinct advantage.
5. Zircon Sand
Zircon sand consists of zirconium silicate (ZrSiO4) and boasts excellent thermal properties and a high melting point. Its low thermal expansion coefficient ensures dimensional stability when casting metals. Zircon sand also offers resistance to metal penetration and excellent mold strength.
While zircon sand is less common and significantly more expensive than silica sand, it is often used in high-performance casting applications, such as aerospace components and intricate molds requiring high precision and surface finish.
Conclusion
In conclusion, the choice of sand in the sand casting process is crucial for determining the casting quality and performance of the final product. Each type of sand offers distinct properties, advantages, and disadvantages that cater to different applications and industries. While silica sand remains the most widely used, alternative options such as green sand, resin sand, chromite sand, and zircon sand provide unique benefits that can meet specific casting requirements. As the industry continues to evolve, advancements in sand materials and casting technologies will likely lead to ongoing improvements in the efficiency and quality of sand casting processes.
Post time:Rhag . 05, 2024 19:12
Next:Benefits of Sand Casting in Manufacturing Processes and Applications