The Steel Sand Casting Process An Overview
Steel sand casting is a crucial manufacturing process utilized in the production of metal components. This method combines the versatility of sand casting with the hardness and strength of steel, resulting in durable and reliable finished products. In this article, we will explore the steel sand casting process, its advantages, applications, and considerations for manufacturers.
Understanding the Steel Sand Casting Process
The steel sand casting process begins with the creation of a mold from sand. The primary materials used in this technique include green sand, which consists of silica sand mixed with clay and water, and in some cases, other additives to enhance the properties of the mold.
1. Mold Creation The process starts with the design of the pattern, which is a replica of the final product. Patterns can be made of various materials, including metal, plastic, or wood. Once the pattern is prepared, it is placed in a mold box, and sand is packed around it to create an imprint. The sand mixture is then compacted to ensure stability during the pouring of molten steel.
2. Core Preparation If the casting requires internal features or hollow sections, cores made of sand are prepared and placed within the mold. These cores create the desired internal shapes of the final product.
3. Pouring Once the mold is ready, molten steel, heated to a temperature of around 1400-1500°C (2550-2730°F), is poured into the mold cavity. The pouring must be conducted carefully to prevent defects such as cold shuts, air entrapment, or misruns.
4. Cooling and Solidification After pouring, the molten steel begins to cool and solidify within the mold. This stage is critical, as the cooling rate can significantly affect the mechanical properties of the final product.
5. Mold Removal After a sufficient cooling period, the sand mold is broken away to reveal the cast part. Depending on the complexity of the design, the removal process may require careful handling to avoid damage to the casting.
6. Finishing The final stage involves cleaning, machining, and finishing the cast product. This may include processes such as grinding, sanding, or surface treatments to achieve the desired finish and tolerances.
Advantages of Steel Sand Casting
One of the key advantages of the steel sand casting process is its ability to produce complex shapes with high dimensional accuracy
. Additionally, it allows for the casting of large components, making it suitable for various industries, including automotive, aerospace, and construction.steel sand casting process
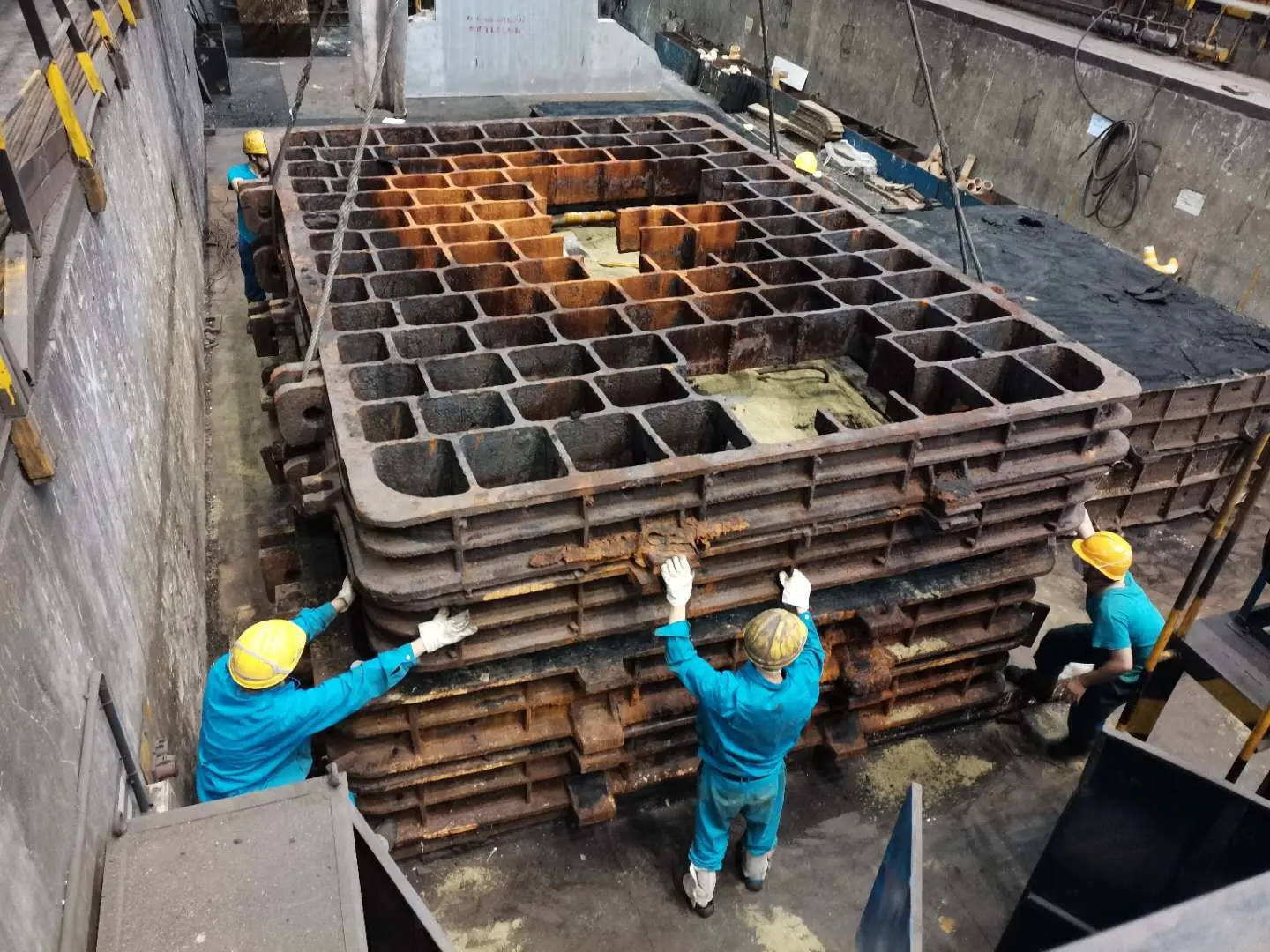
- Cost-Effectiveness Sand casting is often more cost-effective compared to other casting methods, especially for small to medium-sized production runs. The materials required (sand and binding agents) are relatively inexpensive, and the process can be quickly adjusted to accommodate design changes.
- Versatility The steel sand casting process can accommodate a wide range of steel grades, including carbon steel, alloy steels, and tool steels. This versatility makes it suitable for various applications, from ornamental products to engineering components that require high strength and wear resistance.
- Strength and Durability Steel castings exhibit excellent mechanical properties, making them suitable for applications that demand high strength and durability. The inherent properties of steel also allow for improved fatigue resistance and performance under stress.
Applications of Steel Sand Casting
Steel sand casting is widely used across several industries due to its adaptability and the quality of the products it can produce. Key applications include
- Automotive Parts Components such as engine blocks, gear cases, and suspension parts often utilize steel sand casting for their strength and reliability.
- Machinery Components Many industrial machines rely on cast steel parts for their operational efficiency and durability, including gears, frames, and housings.
- Construction Equipment Heavy construction machinery often requires substantial cast components that can withstand extreme conditions, making steel sand casting an ideal choice.
Considerations for Manufacturers
While the advantages of steel sand casting are significant, manufacturers must also consider several factors when utilizing this process. Ensuring the quality of raw materials, maintaining mold integrity, and controlling cooling rates are critical to achieving desired outcomes. Additionally, while the process is cost-effective, the time required for mold production and setup can impact overall lead times, necessitating efficient planning and execution.
In conclusion, the steel sand casting process is a vital manufacturing method that combines cost efficiency with the ability to produce complex, durable components. Its wide range of applications and benefits make it a preferred choice for many industries, continuing to play a pivotal role in modern manufacturing.
Post time:Rhag . 16, 2024 21:39
Next:Innovative Foundry Solutions for High-Quality Sand Casting Services and Products