Understanding Sand Sintering A Pathway to Innovative Material Development
Sintering is a critical process in material science, particularly in the production of ceramics and metals. Among the various types of sintering, sand sintering stands out due to its unique properties and applications. Sand sintering involves the bonding of sand particles through the application of heat, without reaching the melting point of the material. This process not only enhances the mechanical strength and durability of sand-based products but also opens doors to innovative manufacturing techniques.
At its core, sand sintering capitalizes on the natural properties of silica sand, which is abundant and inexpensive. The process begins by compacting sand particles, followed by controlled heating. As the temperature rises, the surface of the sand grains begins to soften, leading to the formation of bonds between adjacent particles. This creates a robust structure that is essential for various applications such as construction, refractory materials, and even in the production of advanced ceramics.
One of the primary advantages of sand sintering is the material's ability to withstand high temperatures. Sintered sand is often used to create molds and cores for metal casting. Because the material can endure extreme conditions, it allows for the production of intricate shapes without compromising structural integrity. This is particularly important in industries such as automotive and aerospace, where precision and durability are paramount.
sand sintering
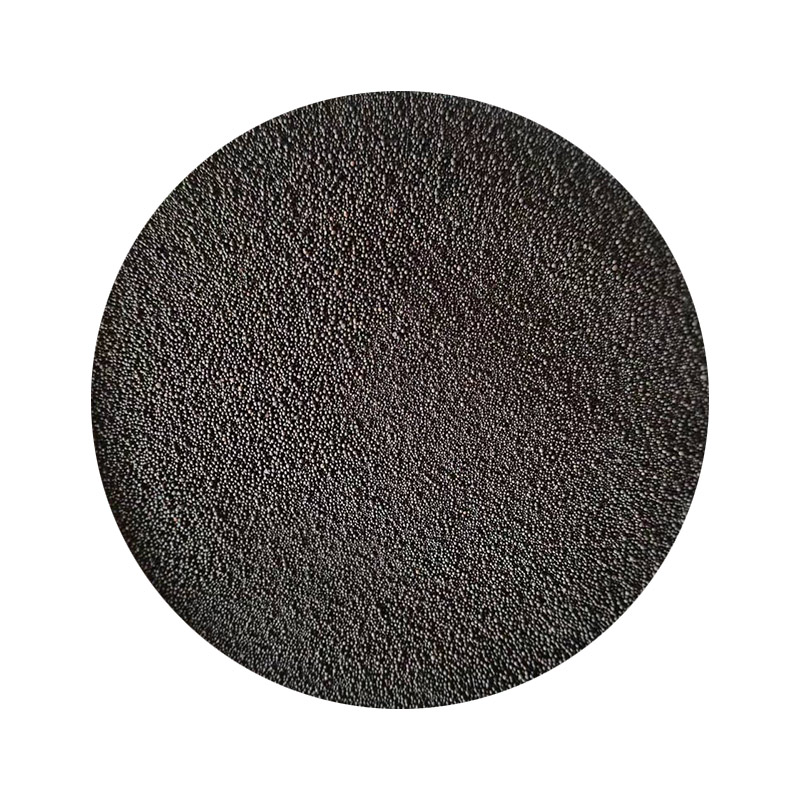
Moreover, sand sintering allows for the creation of composite materials by incorporating additives such as polymers or metal oxides. These additions can enhance specific properties, such as thermal resistance, chemical stability, and aesthetic qualities. For instance, sintered sand can be modified to produce lightweight, highly durable components that meet the evolving demands of modern engineering applications.
In recent years, advancements in technology have propelled sand sintering techniques to new heights. The introduction of 3D printing in sand sintering has revolutionized the way molds and components are designed and manufactured. This additive manufacturing method enables the production of complex geometries that were previously challenging or impossible to achieve with traditional machining methods. As a result, manufacturers can reduce waste and time while increasing design flexibility.
However, the sand sintering process does come with its challenges. Achieving the right balance of temperature and time is crucial to ensure optimal bonding and prevent defects. Additionally, the choice of sand type and particle size can significantly influence the final properties of the sintered product. Continuous research and development are essential to refine the process and explore new variations that could enhance performance.
In conclusion, sand sintering presents a wealth of opportunities for the development of innovative materials with high performance and durability. As industries strive for sustainability and efficiency, the role of sand sintering in advanced manufacturing continues to grow. By harnessing the unique properties of sand and refining sintering techniques, we can pave the way for the next generation of materials that meet the demands of our ever-evolving world. The future of sand sintering will undoubtedly shape various sectors, emphasizing its importance in both traditional and emerging applications.
Post time:Hyd . 06, 2024 21:52
Next:3d sand printing