Understanding Sand Casting Processes
Sand casting is one of the most widely utilized metal casting processes, renowned for its ability to produce complex shapes and designs with a variety of metals such as aluminum, iron, and bronze. The process involves creating a mold from sand, which is then used to form a particular object through the subsequent pouring of molten metal into the mold. This article delves into the intricacies of sand casting, exploring its steps, advantages, and applications.
The Sand Casting Process
The sand casting process begins with the creation of the mold. Typically, this is accomplished using a mixture of sand, clay, and water, which is durable enough to withstand the heat of the molten metal. The first step involves crafting a pattern, which is a replica of the final product. The pattern is usually made from materials such as wood, metal, or plastic and is crucial for creating the negative space in the mold.
Once the pattern is ready, it is placed in a box called a flask, which is then filled with the sand mixture. The sand is compacted around the pattern to ensure that all details are captured. Once the sand hardens, the pattern is removed, revealing a hollow cavity that matches the shape of the desired object. This mold is then equipped with additional features like runners and gates to facilitate the flow of molten metal during casting.
With the mold prepared, the next step involves melting the metal. The metal is heated until it reaches a liquid state, typically in a furnace. Once melted, the metal is carefully poured into the mold cavity through the designated openings. The cooling process begins immediately, allowing the metal to solidify and take the shape of the mold.
After the metal has cooled sufficiently, the mold is broken apart, and the casting is removed. The final step involves cleaning and finishing the casting. This may involve removing any excess material, smoothing rough edges, and applying protective coatings if necessary.
sand casting processes
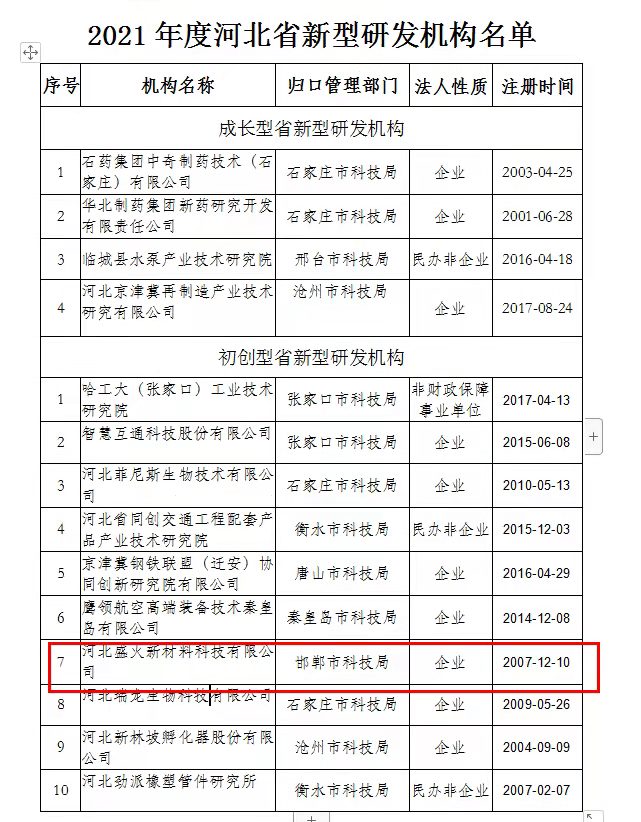
Advantages of Sand Casting
One of the primary advantages of sand casting is its versatility. It can accommodate large and complex parts that would be challenging to produce using other methods. The process is also relatively low in cost, particularly for small production runs, as the molds can often be reused multiple times.
Additionally, sand casting allows for the use of a wide range of metal alloys, expanding the potential applications across various industries. The ability to create intricate designs with excellent surface finish further enhances the process's appeal, making it suitable for various components in automotive, aerospace, and machinery sectors.
Applications of Sand Casting
Sand casting is integral to numerous applications, ranging from the manufacturing of engine blocks and transmission cases in the automotive industry to producing artistic sculptures and complex machinery parts. Due to its cost-effectiveness and flexible nature, it is a preferred method for prototype development and low to medium volume production runs.
In conclusion, sand casting processes play a crucial role in modern manufacturing, combining tradition with technology to produce high-quality metal parts efficiently. Its advantages in flexibility, cost, and capability make it an enduring choice for engineers and manufacturers alike, ensuring its continued relevance in an ever-evolving industrial landscape. As advances in materials science and technology continue to develop, the sand casting process is likely to adapt and innovate, facilitating the production of even more complex and efficient designs in the future.
Post time:Tach . 19, 2024 09:31
Next:Exploring the Benefits and Techniques of Lost Foam Casting in Modern Manufacturing