Sand Casting Alloys An Overview
Sand casting is a widely used metal casting process that utilizes sand as the primary mold material. This method allows for the manufacture of complex shapes and sizes, making it an integral part of various industries, including automotive, aerospace, and machinery. The success of sand casting heavily relies on the choice of alloy, as this defines the physical and mechanical properties of the final product. This article will explore the commonly used alloys in sand casting, their characteristics, and their applications.
Sand Casting Alloys An Overview
Another significant category in sand casting is the use of iron alloys, primarily gray iron and ductile iron. Gray iron accounts for a substantial portion of sand cast products due to its excellent castability, machinability, and wear resistance. It is often used in the manufacturing of engine blocks, pipes, and various machine components. Ductile iron, on the other hand, has improved tensile strength and ductility over gray iron, making it suitable for heavy-duty applications, such as automotive crankshafts and agricultural equipment.
sand casting alloys
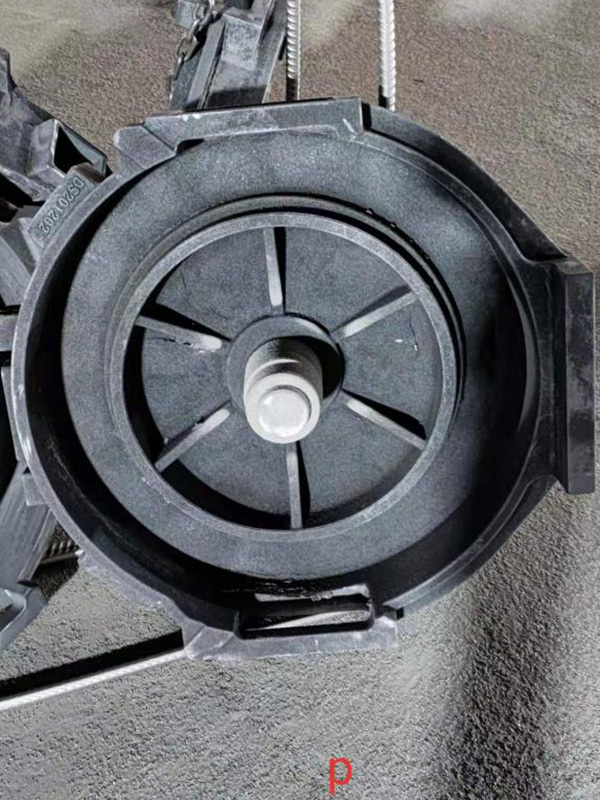
Copper alloys, particularly bronze and brass, are also utilized in sand casting. Bronze, an alloy of copper and tin (and sometimes other metals), is known for its corrosion resistance and great mechanical properties. It's often used in marine applications and artistic sculptures due to its aesthetic appeal. Brass, which typically consists of copper and zinc, is valued for its attractive finish and is commonly used in fittings and fixtures.
Zinc alloys are another important category; they are often appreciated for their low melting point and excellent fluidity. Zinc can be alloyed with aluminum and copper to further improve its casting properties. Zinc alloys are frequently used in applications ranging from die casting to sand casting for components requiring good strength and corrosion resistance, such as electrical housings and automotive parts.
Titanium alloys, though less common due to higher costs, are increasingly being explored in sand casting for applications in the aerospace industry. Titanium is known for its extraordinary strength-to-weight ratio and superior corrosion resistance, making it ideal for high-performance components. However, the challenges associated with titanium casting, such as controlling oxidation and the complex melt process, necessitate advanced technologies and techniques.
In conclusion, sand casting is a versatile process that accommodates a multitude of alloys, each chosen based on the final product's design and functional requirements. The selection of the appropriate alloy is crucial as it profoundly influences the physical and mechanical properties of the cast part. From aluminum and iron to copper, zinc, and titanium alloys, each category presents unique advantages that cater to specific industry needs. Continued advancements in sand casting techniques and alloy formulations are expected to expand the capabilities and applications of this essential manufacturing process, ensuring its relevance in an ever-evolving industrial landscape.
Post time:Tach . 29, 2024 21:07
Next:Innovative Techniques in Resin Sand Casting for Enhanced Precision and Efficiency