The Resin Sand Casting Process An Overview
Resin sand casting is a sophisticated and versatile method widely employed in the manufacturing industry for producing complex metal components. This process combines traditional sand casting techniques with the utilization of resin-bonded sand, enhancing the quality, precision, and surface finish of the final products. As industries increasingly demand high-performance parts with intricate designs, resin sand casting has established itself as a reliable solution.
Understanding the Process
The resin sand casting process begins with the preparation of the mold. A mixture of sand, resin, and a hardener is used to create the mold material. The sand serves as the primary component, while the resin acts as a binder that strengthens the mold. The mixture is typically formed using a cold box process, where the sand is blown into a mold pattern and then cured with hot air or a heat source to harden the resin. This method ensures that the mold retains its shape and can withstand the high temperatures associated with metal pouring.
Once the molds are prepared, the next step is the assembly of the mold halves, which are then secured and ready for metal pouring. The molds are designed to accommodate complex geometries, allowing for intricate designs that are often challenging with other casting methods. Additionally, the smooth surface finish of the resin sand molds minimizes post-casting machining, thereby reducing production time and costs.
Metal Pouring and Cooling
In resin sand casting, molten metal is poured into the mold cavity created by the sand and resin mixture. The choice of metal can vary widely depending on the application, including aluminum, iron, and various steel alloys. The molten metal fills the cavity, taking the shape of the mold, before cooling and solidifying.
One of the significant advantages of resin sand casting is the precision it offers. The tight tolerance levels achievable in this process ensure that the final product requires minimal machining. This precision is increasingly crucial in sectors like automotive and aerospace, where component performance and reliability are paramount.
resin sand casting process
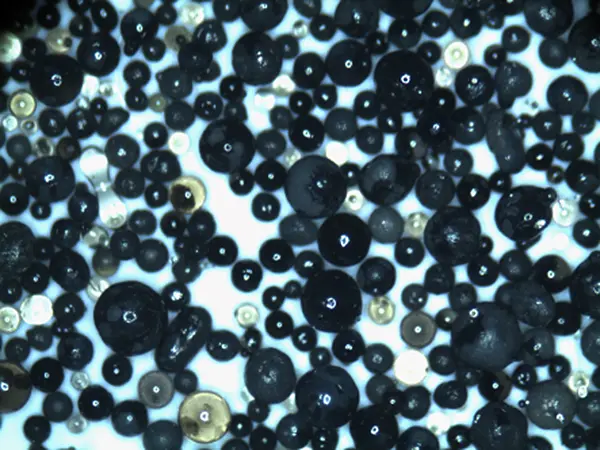
Post-Casting Processes
After the metal has cooled and solidified, the mold is broken apart to reveal the cast component. The resin sand can be easily reclaimed and reused, making this process not only efficient but also environmentally friendly. The ability to reuse the sand contributes to lower material costs and reduced waste.
Following the casting, the final products typically undergo finishing processes such as polishing, surface treatment, or coating to enhance their hardness, corrosion resistance, and aesthetic appeal. These post-casting treatments further improve the performance characteristics of the components, aligning with the stringent requirements of various industries.
Applications and Advantages
The resin sand casting process finds applications across various sectors, including automotive, aerospace, marine, and heavy machinery manufacturing. Components such as engine blocks, brackets, housings, and valve bodies are commonly produced using this method.
The advantages of resin sand casting are numerous. It allows for the production of complex shapes with intricate details, offers improved dimensional accuracy, and provides a better surface finish compared to traditional sand casting methods. Additionally, the process is flexible, accommodating small to medium production runs and catering to custom orders.
Conclusion
In summary, the resin sand casting process stands out as a modern casting method that meets the evolving demands of various industries. Its ability to produce high-quality components with intricate designs while minimizing waste and production costs makes it a preferred choice for manufacturers. As technology continues to advance, the role of resin sand casting is likely to grow, further solidifying its place in the manufacturing landscape.
Post time:Hyd . 13, 2024 20:23
Next:sanding a 3d print