Resin Bonded Sand Casting An Overview
Resin bonded sand casting is a popular metal casting process known for its ability to produce high-quality castings with intricate details and excellent surface finishes. This casting technique employs a mixture of sand and a thermosetting resin binder, which significantly enhances the properties of traditional sand casting methods. By understanding the fundamentals of resin bonded sand casting, one can appreciate its advantages, applications, and overall significance in modern manufacturing.
The Process
The resin bonded sand casting process begins with the preparation of the sand mixture. Unlike conventional sand casting, where sand is typically held together with water, resin bonded sand uses a thermosetting resin that is mixed with the sand in precise proportions. The most commonly used resins are phenolic or furan resins, which, upon heating, solidify to create a strong, rigid mold.
After mixing the sand and resin, the mixture is typically compacted into a mold using various techniques such as vibration or pressure. Once the mold is formed, it is heated to cure the resin, solidifying the mold structure. This curing process allows the mold to maintain its shape even under the heat of molten metal pouring.
Once the mold is ready, the molten metal is poured into the cavity created by the mold. After the metal cools and solidifies, the mold is broken away to reveal the finished casting. This method not only enables the production of complex geometries but also reduces the amount of post-casting finishing required, leading to improved efficiency.
Advantages
One of the primary advantages of resin bonded sand casting is the superior surface finish it offers compared to traditional sand casting methods. The resin’s bonding properties allow for sharper details and smoother surfaces, which is particularly beneficial for components requiring aesthetic appeal or lower tolerances.
resin bonded sand casting
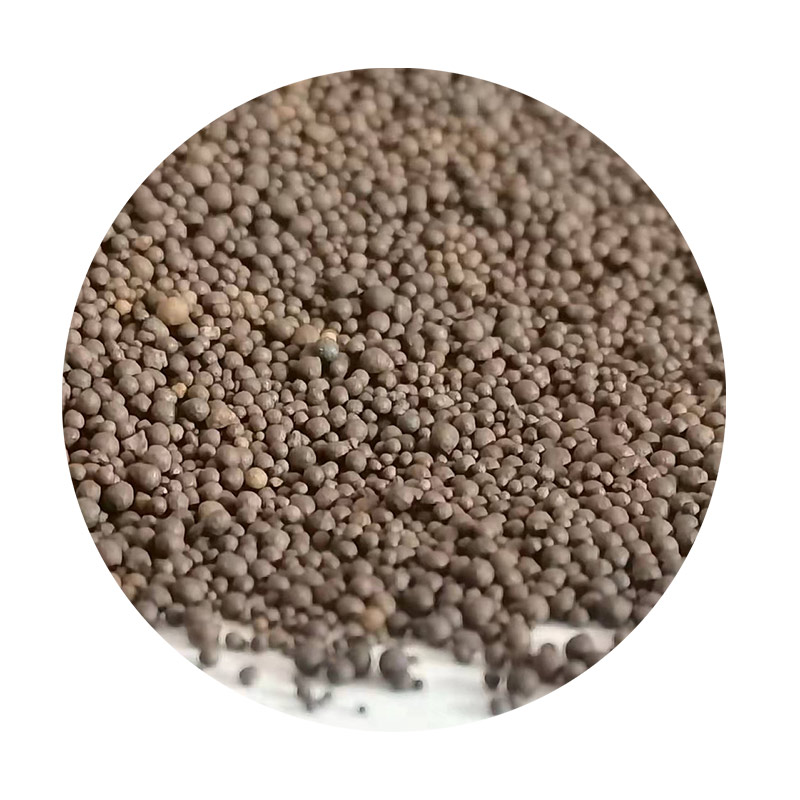
Additionally, resin bonded sand casting exhibits excellent dimensional accuracy. The heat resistance of the cured resin allows the molds to retain their shape under thermal stress, reducing the risk of distortion common in other molding techniques. This accuracy is crucial in industries like aerospace and automotive manufacturing, where precision components are paramount.
Another notable advantage is the reduced setup time. The quick curing process of the resin enables faster production cycles, which, combined with its ability to create complex shapes, makes it ideal for low to medium volume production runs. This efficiency can lead to significant cost savings and improved turnaround times for manufacturers.
Applications
The applications of resin bonded sand casting are diverse and span multiple industries. It is widely used in the production of automotive components, where strength and precision are critical. Additionally, industries such as aerospace, marine, and heavy machinery also benefit from this technique for producing complex components that can withstand harsh environments.
Furthermore, the versatility of resin bonded sand casting allows it to be used for both ferrous and non-ferrous metals, expanding the range of possibilities for manufacturers. Custom tooling can also be developed for specific needs, further enhancing the adaptiveness of this casting method.
Conclusion
In conclusion, resin bonded sand casting represents a significant advancement in the field of metal casting technology. With its enhanced surface finish, dimensional accuracy, and efficient production capabilities, it serves as a valuable process for a variety of applications. As industries continue to demand higher standards of quality and precision, understanding and utilizing resin bonded sand casting will remain essential for manufacturers looking to innovate and improve their products.
Post time:Rhag . 05, 2024 22:04
Next:Innovative Techniques in 3D Sand Casting for Enhanced Manufacturing Efficiency