Understanding the Parts of Sand Casting
Sand casting, also known as sand mold casting, is one of the oldest and most commonly used metal casting processes. It involves creating a mold from a mixture of sand and a bonding agent, then pouring molten metal into that mold to create a desired shape. To fully comprehend the sand casting process, it is essential to understand its various components and parts.
1. Pattern
The pattern serves as the model for the final product and is typically made of wood, metal, or plastic. It is a crucial element in sand casting, as it determines the dimensions and contours of the final casting. Patterns can be solid or split; solid patterns are single units, while split patterns are divided into two or more sections to facilitate easier removal from the sand mold.
2. Mold
The sand mold is crafted from a mixture of sand, clay, and water. The sand provides the ability to withstand the heat of molten metal, while the clay acts as a binder, holding the sand grains together. The quality of the mold is critical as it influences the surface finish and dimensional accuracy of the final casting. Molds can be designed for single or multiple uses, with the former being commonly employed for one-off or custom castings.
3. Core
In cases where internal features or complex shapes are needed, cores are utilized. Cores are made from similar sand mixtures but are separate components that fit into the mold. They are often used to create hollow cavities within the casting. Cores can be removed after the metal cools, leaving behind spaces or hollow sections according to the design requirements.
4
. Ram and Dragparts of sand casting
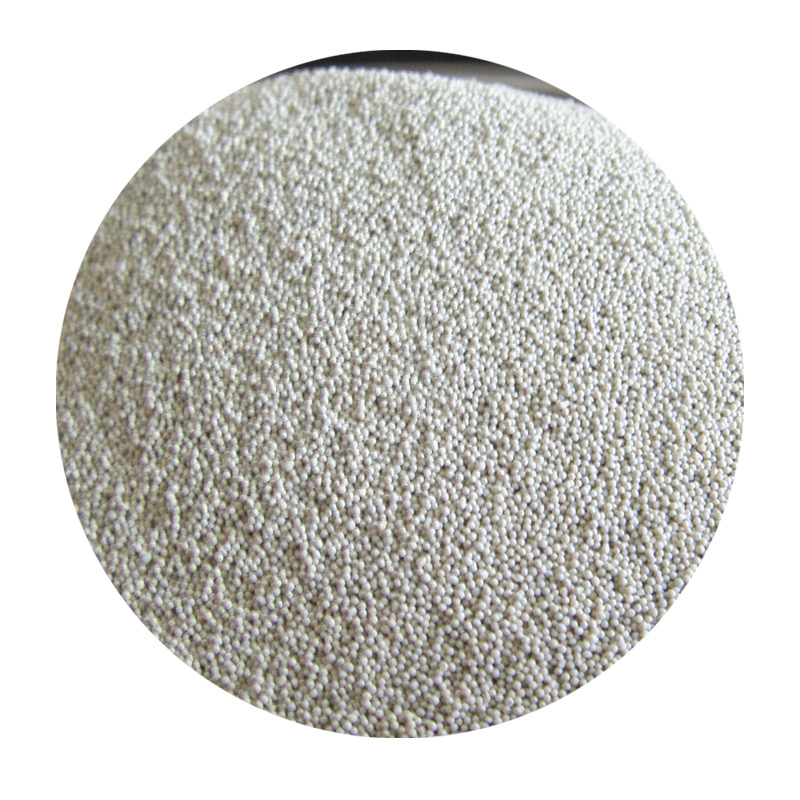
The mold is typically made up of two parts the ram (top half) and the drag (bottom half). These components are brought together to form a complete mold, and each part is responsible for shaping different halves of the cast item. The design and quality of the ram and drag play a significant role in establishing the integrity of the mold, ensuring that it can withstand the pressures of pouring molten metal.
5. Feeding System
The feeding system is an essential part of the sand casting process. It consists of channels and gates that direct the flow of molten metal into the mold cavity. A well-designed feeding system ensures that the metal fills all sections of the mold uniformly, minimizing defects such as voids or cold shuts. The feeding system also aids in compensating for metal shrinkage as it cools.
6. Vent and Riser
Vents are small openings in the mold that allow gases to escape during the pouring process. Without vents, trapped gases can cause defects in the casting. Risers, on the other hand, are reservoirs of molten metal located above the mold cavity. They feed additional metal into the casting as it cools and shrinks, ensuring that the final product remains solid and free from defects.
7. Finishing Tools
Once the casting has cooled and solidified, the finishing process begins. This involves removing excess material, cleaning the surface, and possibly machining or polishing the final product. Finishing tools and techniques are crucial in achieving the desired surface finish and dimensional accuracy.
Conclusion
Understanding the various parts of the sand casting process provides valuable insight into its functionality and relevance in manufacturing. Each component, from the pattern to the finishing tools, plays a vital role in ensuring the accuracy and quality of the final cast product. As industries continue to evolve, sand casting remains a fundamental technique in producing metal components across a wide range of applications.
Post time:Medi . 28, 2024 15:20
Next:cast iron sand casting