Molding Sand for Metal Casting An Essential Component in Foundry Operations
Molding sand is a critical material used in the metal casting process, where molten metal is poured into a pre-formed mold to produce various metal components. The effectiveness of this casting process largely depends on the quality and properties of the molding sand. Foundries rely on specific types of sand, mixed with binders and additives, to create molds that can withstand the intense heat and pressure of liquid metals while providing excellent detail and dimensional accuracy.
Types of Molding Sand
The primary types of molding sand include green sand, dry sand, and investment sand.
1. Green Sand This is the most commonly used molding sand, composed of silica sand, clay, and moisture. The clay acts as a binder, giving the sand its plasticity, which allows it to be shaped easily. Green sand molds are generally used for ferrous metal castings, thanks to their ability to retain detail and resist thermal shock. 2. Dry Sand Unlike green sand, dry sand is constructed with a low moisture content, often enhanced with a resin binder. This type is primarily used in high-temperature casting processes, such as for non-ferrous metals. It allows for better dimensional stability and surface finish compared to green sand.
3. Investment Sand This type, also known as investment casting sand, is used in precision casting applications. It typically involves the use of a form made from a wax pattern, which is coated with a sand mixture. Once the mold is formed, the wax is melted away, leaving a detailed cavity for the molten metal.
Properties of Molding Sand
molding sand for metal casting
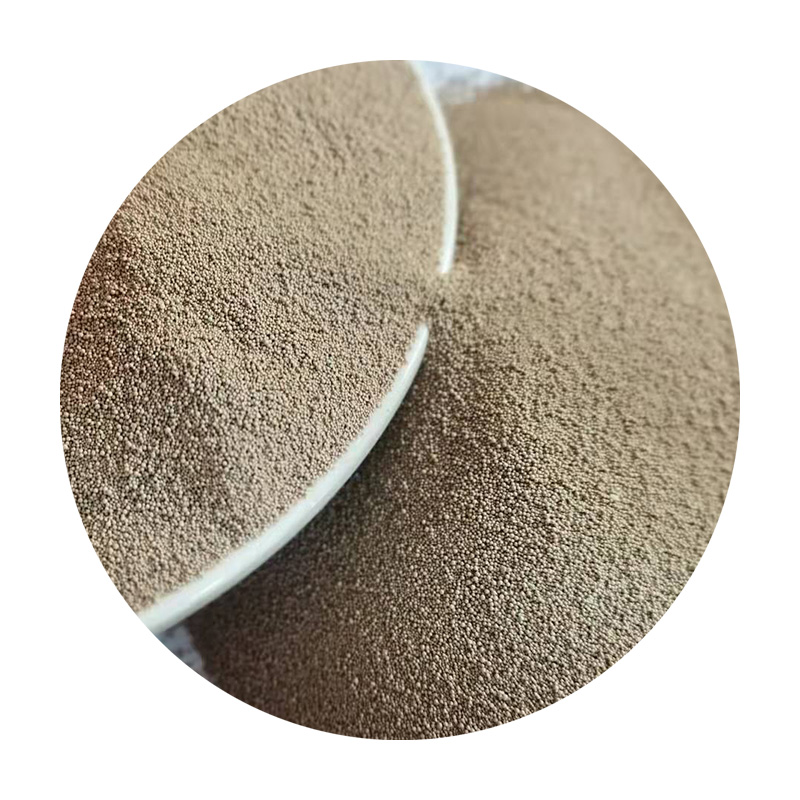
The effectiveness of molding sand is characterized by several key properties
- Grain Size and Shape The size and shape of the sand grains significantly affect the strength of the mold and the surface finish of the cast part. A uniform grain size helps in achieving better compaction and minimal defects in the final product.
- Flowability Good molding sand must flow easily during the molding process to fill the mold cavity completely and avoid air pockets. This ensures that intricate designs can be accurately reproduced.
- Thermal Stability Molding sand must withstand the high temperatures of molten metal without breaking down. Its thermal stability plays a crucial role in preventing the mold from cracking or weakening during the casting process.
- Reusability Many sand systems are designed for recycling and reuse, which reduces waste and lowers material costs for foundries. Advanced processes allow for the cleaning and reconditioning of sand, making it suitable for multiple casting cycles.
Conclusion
In the world of metal casting, molding sand plays an indispensable role in determining the quality and precision of the final product. Understanding the different types of molding sand, their properties, and applications is essential for foundry operations aiming to produce reliable and high-quality metal components. As technology advances, innovations in molding sand formulations and recycling techniques continue to enhance the efficiency and sustainability of the casting industry, ensuring that it meets the demands of modern manufacturing.
Post time:Tach . 19, 2024 17:36
Next:lost foam casting coating