The Art of Iron Sand Casting A Comprehensive Overview
Iron sand casting, a technique rooted in ancient practices, remains a vital component in modern manufacturing. This process utilizes iron sand, primarily consisting of magnetite, as a key raw material for producing a variety of ferrous items ranging from art pieces to industrial machinery components. Understanding the principles of iron sand casting can shed light on its importance in today's metallurgical landscape.
Historical Context
Iron sand casting has a rich history that dates back thousands of years. Ancient civilizations, such as the Japanese, were known to use iron sand due to its abundance and low melting point, which made it an excellent material for casting. The traditional Japanese technique of tatara smelting is a prime example, where iron sand was smelted in clay furnaces to produce high-quality iron.
As the industrial revolution unfolded, the demand for more robust and versatile casting methods grew. Iron sand casting evolved to meet the needs of burgeoning industries, enabling the mass production of tools, machinery, and numerous other applications.
The Process of Iron Sand Casting
The process of iron sand casting involves several steps that ensure precision and quality in the final product.
1. Preparation of Molds The casting process begins with the creation of molds that define the shape of the final product. This is often done using sand mixed with a binding agent to form a sturdy mold. The accuracy of the mold is critical as it impacts the dimensional integrity of the cast object.
2. Melting the Iron Sand The prepared molds are then subjected to high temperatures in a furnace, where the iron sand is melted. This stage requires careful temperature control to ensure that the sand completely transforms into a liquid state.
3. Pouring the Molten Iron Once the iron sand reaches its molten state, it is poured into the pre-prepared molds. The pouring must be quick yet controlled to prevent any defects in the cast.
iron sand casting
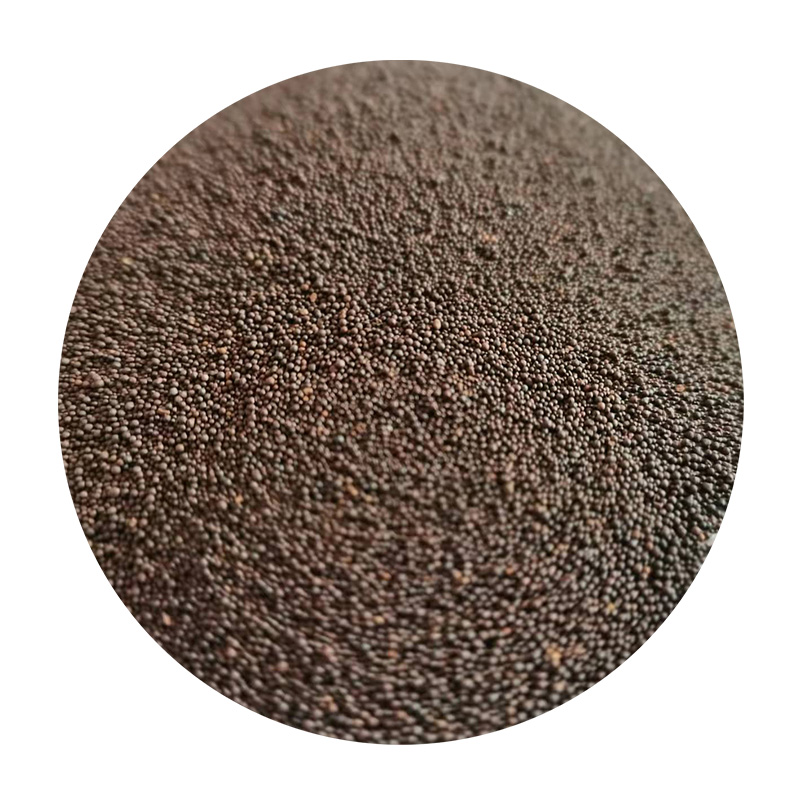
4. Cooling and Solidification After pouring, the molten iron sand cools and solidifies within the mold. This stage can take varying lengths of time depending on the thickness of the casting and ambient temperatures.
5. Finishing Touches Once cooled, the molds are broken away, revealing the cast object. It may require additional processes such as machining, grinding, and surface finishing to achieve the desired final shape and surface quality.
Advantages of Iron Sand Casting
One of the primary advantages of iron sand casting is its versatility. This method can accommodate complex shapes and designs, making it suitable for both artistic and industrial applications. Additionally, the use of iron sand is economically advantageous due to its availability and cost-effectiveness compared to other casting materials.
Furthermore, iron sand casting also boasts excellent mechanical properties, yielding products with high strength and durability. This is particularly beneficial for components that must withstand heavy loads or intense environmental conditions, such as those used in automotive parts or heavy machinery.
Environmental Considerations
While iron sand casting is advantageous in many ways, it is essential to consider its environmental impacts. The extraction of iron sand can lead to ecological disruptions, particularly if not managed sustainably. Modern practices have begun to incorporate recycling techniques and sustainable sourcing of raw materials, aiming to minimize the industry's carbon footprint.
Conclusion
Iron sand casting stands as a testament to the ingenuity and adaptability of manufacturing processes. Its combination of historical relevance, practical advantages, and modern adaptations ensures that it will continue to play a crucial role in various industries for years to come. As we advance technologically, it will be exciting to see how traditional methods like iron sand casting evolve to meet the challenges of a sustainable future, melding craftsmanship with ecological responsibility.
Post time:Rhag . 07, 2024 12:58
Next:advantages of sand casting process