High-Quality Sand Casting A Cornerstone of Manufacturing Excellence
Sand casting, one of the oldest and most versatile metal casting processes, has stood the test of time and continues to play a crucial role in modern manufacturing. While many advanced techniques have emerged over the years, the robustness and adaptability of sand casting make it a preferred choice for producing high-quality metal components. This article will explore the key aspects of high-quality sand casting, including its process, advantages, applications, and the measures to ensure superior results.
The Sand Casting Process
The sand casting process involves several steps that begin with the creation of a pattern, which is a replica of the final product. This pattern is typically made from materials such as wood, metal, or plastic, and it plays a pivotal role in defining the dimensions and finish of the cast object. Once the pattern is ready, it is placed into a mold box, and sand is packed around it. The sand used in this process is a special type known as green sand, which consists of silica sand, clay, and water, providing excellent binding properties.
After the pattern is removed, the mold is prepared for pouring molten metal. The quality of the mold directly impacts the finish and structural integrity of the cast piece. Once the molten metal is poured into the mold and allowed to solidify, the next step involves break-out and core removal. Finally, the cast piece is cleaned, trimmed, and subjected to finishing processes to achieve the desired surface quality.
Advantages of High-Quality Sand Casting
1. Versatility Sand casting can accommodate a wide range of metals, including iron, aluminum, brass, and more, making it suitable for various applications. Additionally, it can produce both small and large parts, from intricate designs to heavy-duty components.
2. Cost-Effectiveness Compared to other casting methods, sand casting often requires lower initial investment and tooling costs. The flexibility in modifying patterns for different projects further enhances its cost-effectiveness.
3. Complex Geometries High-quality sand casting is capable of producing complex shapes and intricate designs, which can be challenging for other processes. This allows manufacturers to create parts that closely match their specifications without extensive additional machining.
4. Scalability Sand casting can efficiently produce single pieces or large quantities of components. This scalability makes it ideal for both prototypes and full-scale production runs.
high quality sand casting
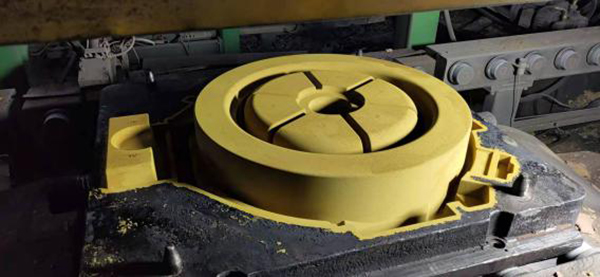
Ensuring Quality in Sand Casting
To achieve high-quality results in sand casting, several key factors must be considered
1. Material Selection The choice of sand and binders is crucial. High-quality silica sand, combined with the right clay and moisture content, ensures proper mold strength and thermal properties. Regular testing and calibration of raw materials can prevent defects in the cast products.
2. Mold Preparation Proper mold preparation techniques improve the accuracy and finish of the cast pieces. This includes maintaining precise tolerances in mold dimensions, consistent compaction of the sand, and effective venting to allow gases to escape during pouring.
3. Temperature Control Monitoring the temperature of the molten metal is essential. Pouring the metal at the correct temperature reduces the risk of defects such as porosity or shrinkage.
4. Post-Casting Treatments After casting, several finishing processes such as shot blasting, grinding, and surface treatment can enhance the quality of the final product. Implementing these treatments ensures the removal of any surface imperfections and improves aesthetic appeal.
Applications of Sand Casting
High-quality sand casting finds extensive applications in various industries, including automotive, aerospace, construction, and general manufacturing. Components such as engine blocks, valve bodies, pump casings, and intricate decorative items can all be effectively produced using this method.
Conclusion
High-quality sand casting remains an essential process in the manufacturing industry, offering unmatched versatility, cost-effectiveness, and the ability to produce complex geometries. By focusing on material selection, mold preparation, temperature control, and post-casting treatments, manufacturers can achieve superior results that meet the demands of modern engineering. As advancements continue to take place, sand casting is poised to remain a reliable option for quality metal component production for years to come.
Post time:Rhag . 19, 2024 09:57
Next:sanding casting resin