The Difference Between Sand Casting and Die Casting
Casting is a crucial manufacturing process used to create a variety of metal components by pouring molten metal into a mold. Among the myriad casting techniques, sand casting and die casting are two of the most commonly employed methods, each with distinct characteristics, advantages, and disadvantages. Understanding the fundamental differences between these two processes is essential for selecting the appropriate method for a specific application.
Sand Casting
Sand casting is one of the oldest and most versatile casting processes. It involves the use of a sand-based mold that is typically made from a mixture of sand, clay, and water. This mixture gives the mold sufficient strength and flexibility to hold its shape during the pouring of the molten metal.
Advantages of Sand Casting 1. Cost-Effectiveness Sand casting is relatively inexpensive, especially for small production runs. The materials required for mold creation are generally low-cost, making it an attractive option for prototype development or low-volume production. 2. Flexibility This method can accommodate a wide range of casting sizes and complexities. The molds can be customized easily, allowing for intricate designs without significant alterations to the equipment. 3. Materials Variety Sand casting allows for the use of various metals, including but not limited to aluminum, iron, and bronze, enabling manufacturers to choose materials best suited for their specific needs.
However, sand casting also has its drawbacks. The process typically results in rougher surface finishes compared to die casting, and the dimensional accuracy is generally lower. Additionally, the sand molds may need extensive finishing work to meet precise requirements.
difference between sand casting and die casting
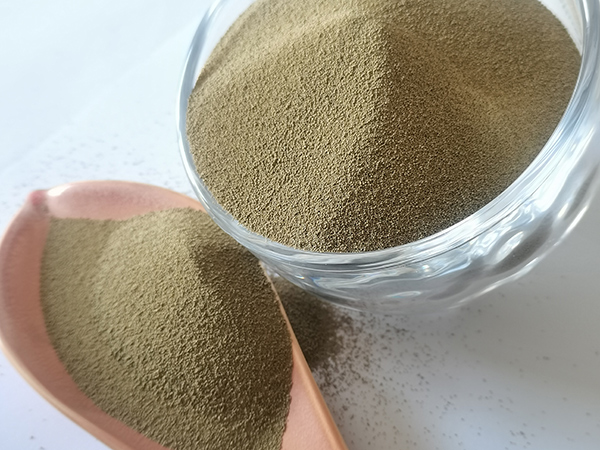
Die Casting
Die casting is a more modern and refined metal casting process that utilizes high-pressure to inject molten metal into a steel mold. The molds used in die casting are called dies and are designed to produce precise, highly detailed parts.
Advantages of Die Casting 1. High Precision and Accuracy Die casting produces components with excellent dimensional accuracy and smooth surface finishes. This precision is particularly beneficial for parts that require tight tolerances and intricate designs. 2. Efficient Production The process is highly automated and can be adapted for mass production, making it ideal for large production runs where speed and consistency are paramount. 3. Material Properties Parts made from die casting generally have better mechanical properties due to the denser structure of the cast material, making it suitable for more demanding applications.
However, die casting has its limitations. The initial setup cost is significantly higher due to the expensive molds, which may not be economically viable for small production runs. Additionally, the types of metals that can be used in die casting are typically limited to non-ferrous alloys, such as aluminum, zinc, and magnesium.
Conclusion
In summary, sand casting and die casting serve distinct roles in the manufacturing landscape. Sand casting is valued for its cost-effectiveness and flexibility, making it suitable for small batches and prototypes. On the other hand, die casting offers exceptional precision and efficiency, making it the method of choice for high-volume production of complex and detailed components. The choice between these two methods ultimately depends on the specific requirements of the project, including budget, production volume, and the desired properties of the final product. Understanding these differences will help manufacturers make informed decisions tailored to their unique needs.
Post time:Tach . 12, 2024 03:22
Next:golden sanda