The Art of Ceramic Sanding Techniques and Tips for Perfect Finishes
Ceramic sanding, often an overlooked process in the world of ceramics, is essential for achieving smooth, polished surfaces that enhance both aesthetic appeal and functional quality. Whether you are a hobbyist or a professional potter, understanding the intricacies of ceramic sanding can elevate your work from ordinary to extraordinary.
The process begins after the initial firing of the ceramic piece, often referred to as bisque firing. This gives the ceramic body strength while remaining porous enough to allow for effective sanding. At this stage, many artists might rush to glaze their work without considering the finishing touches that sanding provides. However, taking the time to sand can significantly improve the final appearance of the glaze and the overall quality of the piece.
One of the first steps in ceramic sanding is choosing the right tools. Sanding sponges or abrasive papers designed specifically for ceramics are highly effective. These products come in various grits, allowing artists to gradually increase the smoothness of the surface. Coarse grits can help remove larger imperfections and rough areas, while finer grits are ideal for achieving a silky finish. It’s advisable to start with a medium grit and progress to finer grits to avoid deep scratches that can be difficult to remove.
Technique is crucial in ceramic sanding. It’s important to apply even pressure while sanding to avoid creating uneven surfaces. Users should employ a circular motion or sand in lines, depending on the shape of the piece. When sanding edges, a gentle touch is needed to prevent chipping. Moreover, regularly checking the surface with your hand can help gauge the smoothness and identify any areas that may require more attention.
ceramic sanding
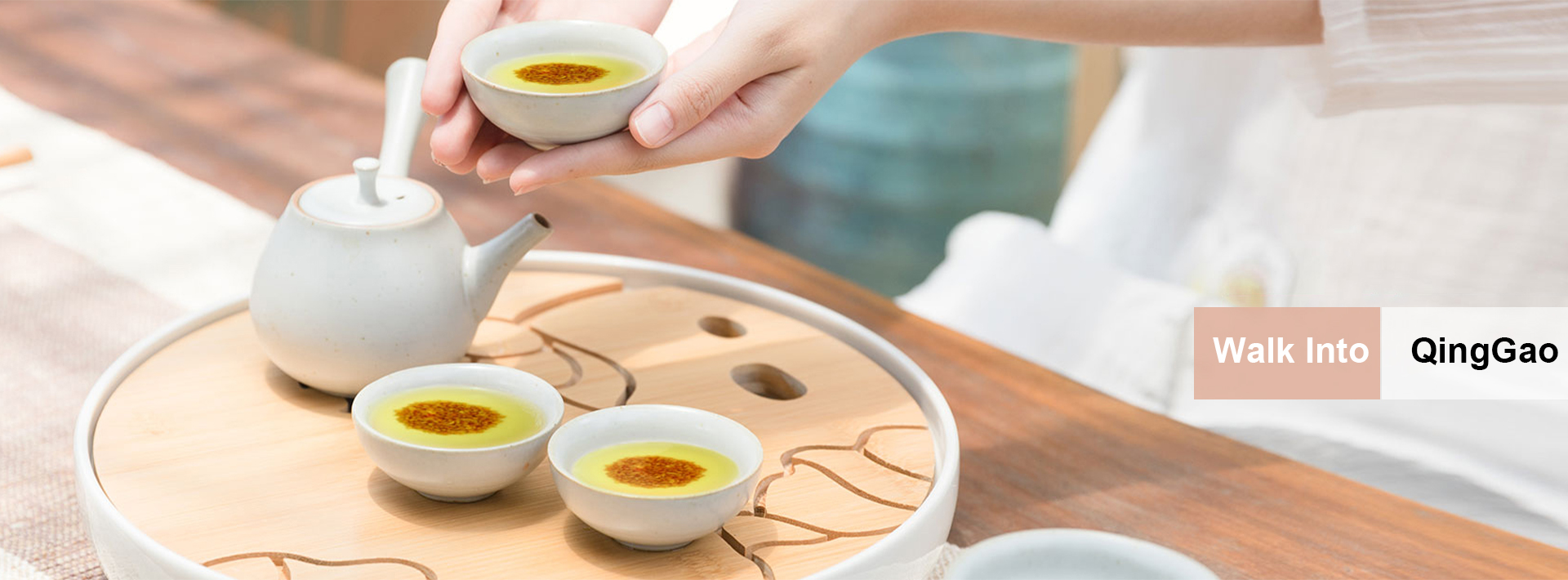
Another key aspect of ceramic sanding is controlling dust. Sanding can create a significant amount of fine dust, which can be hazardous when inhaled. Using a dust mask and working in a well-ventilated area is highly recommended. Additionally, lightly wetting the surface can minimize dust production and help keep the sanding surface clean.
After sanding, it’s essential to clean the piece thoroughly. Any remaining dust can affect glaze adhesion, leading to undesirable outcomes. A damp cloth or sponge can effectively remove any residual particles, ensuring that the surface is ready for glazing.
Once you’ve achieved a perfectly sanded surface, the next step is glazing. The smoothness of the ceramic will allow the glaze to flow more evenly, enhancing the final appearance. A well-sanded piece will show off the glaze’s vibrancy and depth, showcasing the skill and effort put into the creation.
In conclusion, ceramic sanding is an art form in its own right. It requires patience, practice, and the right techniques to master. By investing time in sanding, ceramic artists can ensure their pieces not only look flawless but also withstand the test of time. Whether you are crafting functional items or intricate sculptures, the impact of a well-sanded surface cannot be understated. So, the next time you finish a ceramic piece, remember to take the extra step to sand it to perfection.
Post time:Medi . 25, 2024 02:48
Next:casting sand for sale