Advantages of Lost Foam Casting
Lost foam casting is an innovative metal casting process that has gained popularity in various industries due to its numerous advantages. This technique involves the use of a foam pattern, typically made of expanded polystyrene (EPS), which is coated with a refractory material. When molten metal is poured into a mold, the foam evaporates, leaving a precise replica of the original pattern. This method has revolutionized the casting industry and offers several unique benefits.
Advantages of Lost Foam Casting
Another notable benefit is the excellent surface finish achieved through the lost foam process. Because the foam pattern evaporates as the metal fills the mold, there is minimal room for air inclusions or defects. This results in a smooth surface that often requires little to no additional finishing. The superior surface quality is essential for components in industries such as automotive and aerospace, where precision and aesthetics are critical.
advantages of lost foam casting
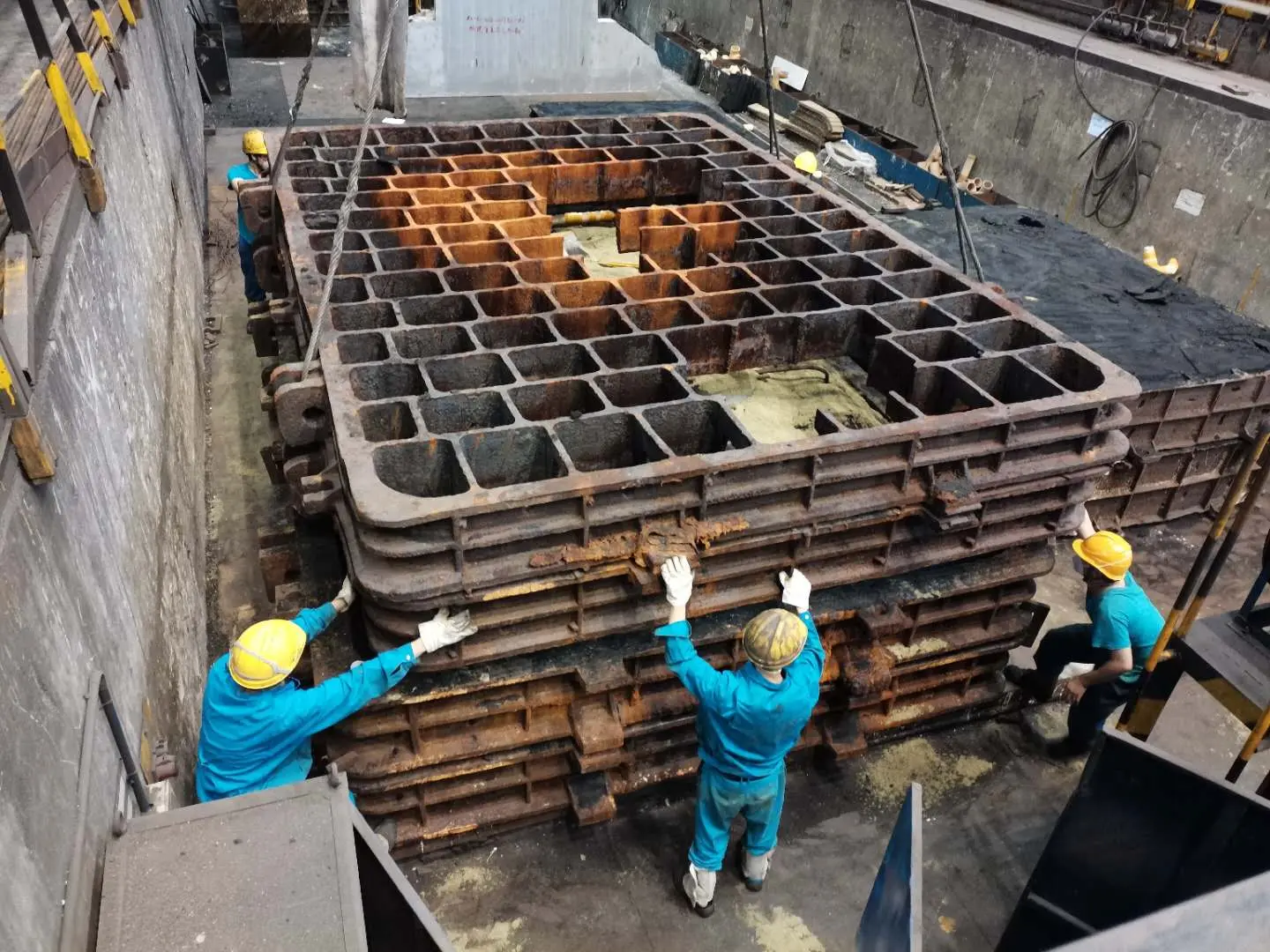
Moreover, lost foam casting is inherently efficient in terms of material usage. The process minimizes waste because it allows for the casting of complex geometries that would typically require additional machining or material removal. By using the foam pattern, manufacturers can achieve near-net shapes, reducing the amount of raw material needed and minimizing scrap. This efficiency not only decreases production costs but also makes it a more sustainable option, aligning with modern environmental standards.
Additionally, this casting process offers considerable flexibility in terms of design modifications. Since the foam patterns are typically lightweight and cost-effective to produce, changes can be made relatively quickly, allowing for rapid prototyping and iterative design processes. This flexibility is particularly beneficial in industries where design specifications may evolve, enabling companies to respond swiftly to market demands and customer requirements.
Furthermore, lost foam casting is compatible with a variety of metals, including aluminum, iron, and certain alloys. This versatility makes it suitable for a broad range of applications, from automotive parts to industrial machinery components. Manufacturers can select the appropriate material based on the desired properties of the final product, such as strength, weight, or corrosion resistance.
In conclusion, lost foam casting presents several advantages that make it an attractive choice for modern manufacturing. Its capability to produce complex shapes, achieve high-quality finishes, minimize material waste, allow for flexible design changes, and accommodate various metals positions it as a leading method in the casting industry. As technology continues to advance, the lost foam casting process is likely to become even more widely adopted, driving innovation and efficiency across numerous sectors.
Post time:Hyd . 14, 2024 14:02
Next:Lightweight Aggregate for Sustainable Construction Solutions