The Intersection of 3D Printing and Sand Casting in Modern Manufacturing
In recent years, the manufacturing industry has experienced a technological revolution, with 3D printing emerging as a transformative process across various applications. One noteworthy area where 3D printing technology is making significant strides is in sand casting, a traditional method that has been used for centuries to create intricate metal parts. The convergence of these two technologies is enhancing efficiency, reducing costs, and widening the scope of creative possibilities in metal fabrication.
Sand casting, a process where molten metal is poured into molds made from sand, has long been favored for its ability to produce complex shapes and large components. However, traditional sand casting methods can be time-consuming and labor-intensive, requiring the production of patterns and cores that may take weeks to design and manufacture. This is where 3D printing comes into play, providing a faster and more precise way to create molds and cores.
The Intersection of 3D Printing and Sand Casting in Modern Manufacturing
The integration of 3D printing into the sand casting workflow also contributes to cost savings. Traditional mold-making requires significant material and labor, whereas 3D printing optimizes these resources by minimizing waste. Furthermore, manufacturers can produce molds on-demand, obviating the need for large inventories of physical patterns. This shift towards a more sustainable production method not only reduces costs but also minimizes the environmental impacts traditionally associated with casting.
3d printing sand casting
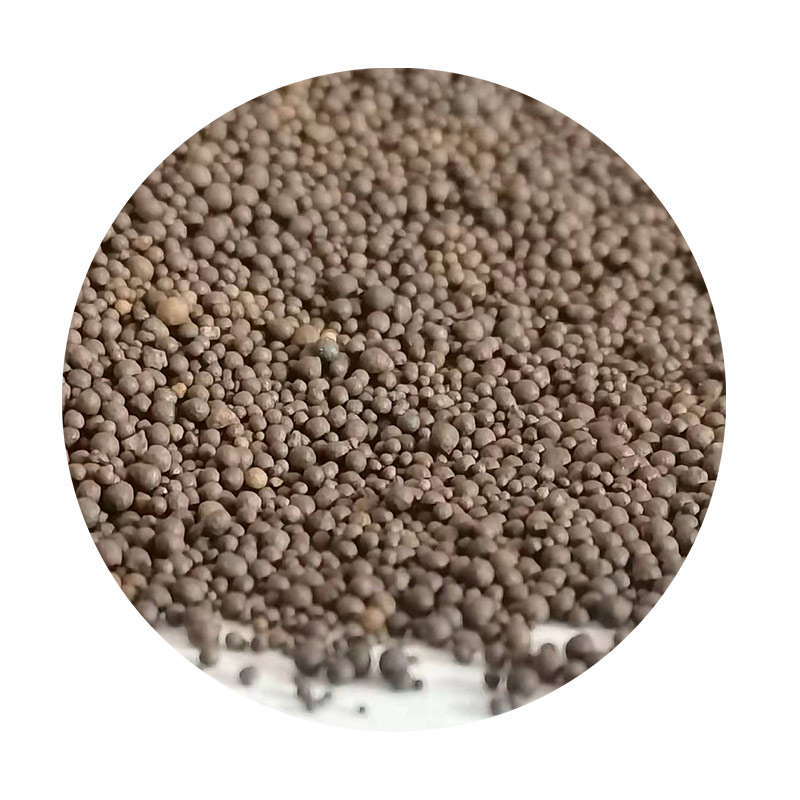
Another advantage of combining 3D printing with sand casting is the enhancement of design flexibility. Engineers can innovate without being constrained by the limitations of conventional machining and casting techniques. Complex internal channels, intricate designs, and lightweight structures are more easily achievable with 3D-printed molds, leading to improved performance characteristics in the finished product.
The aerospace and automotive industries are among the first to benefit from this technological synergy. In aerospace, for instance, lightweight components produced through 3D-printed sand casting can contribute to fuel efficiency and performance. Similarly, the automotive industry can leverage these techniques to produce lower-volume, high-value parts that meet stringent industry standards without lengthy production times.
Despite the numerous advantages, there are challenges that manufacturers must address in seamlessly integrating 3D printing and sand casting. Issues such as surface finish quality and the strength of the molds produced must be thoroughly investigated to ensure that the final castings meet performance requirements.
In conclusion, the marriage of 3D printing technology and sand casting presents exciting opportunities for innovation in manufacturing. As industries continue to embrace this hybrid approach, the potential for creating more complex, efficient, and sustainable metal components will only grow. By marrying traditional craftsmanship with cutting-edge technology, manufacturers can look forward to a future rich with possibilities and advancements.
Post time:Hyd . 12, 2024 08:07
Next:rapid sand casting