3D Printing for Sand Casting Revolutionizing the Foundry Industry
In recent years, 3D printing has emerged as a transformative technology across various industries, and the foundry sector is no exception. Specifically, the integration of 3D printing into sand casting processes has significantly enhanced manufacturing efficiency, precision, and sustainability. This innovative approach offers a plethora of benefits that traditional methods struggle to match, fundamentally altering how sand casting is performed.
Sand casting is one of the oldest metal casting methods, involving the creation of molds from sand to form metal objects. Traditionally, this process has required the use of wooden patterns, which can be time-consuming and costly to produce. With the advent of 3D printing, patterns can now be designed and fabricated rapidly using digital modeling software. This shift not only speeds up the production process but also allows for greater complexity in design, enabling manufacturers to create intricate patterns that would be difficult or impossible to achieve with conventional techniques.
3D Printing for Sand Casting Revolutionizing the Foundry Industry
Additionally, the customization options available through 3D printing are nearly limitless. Manufacturers can adjust designs easily without the need for new tooling, allowing them to experiment with different geometries and features until they find the optimal design. This flexibility supports innovation and allows companies to respond swiftly to market changes or client demands, enhancing their competitive edge.
3d printing for sand casting
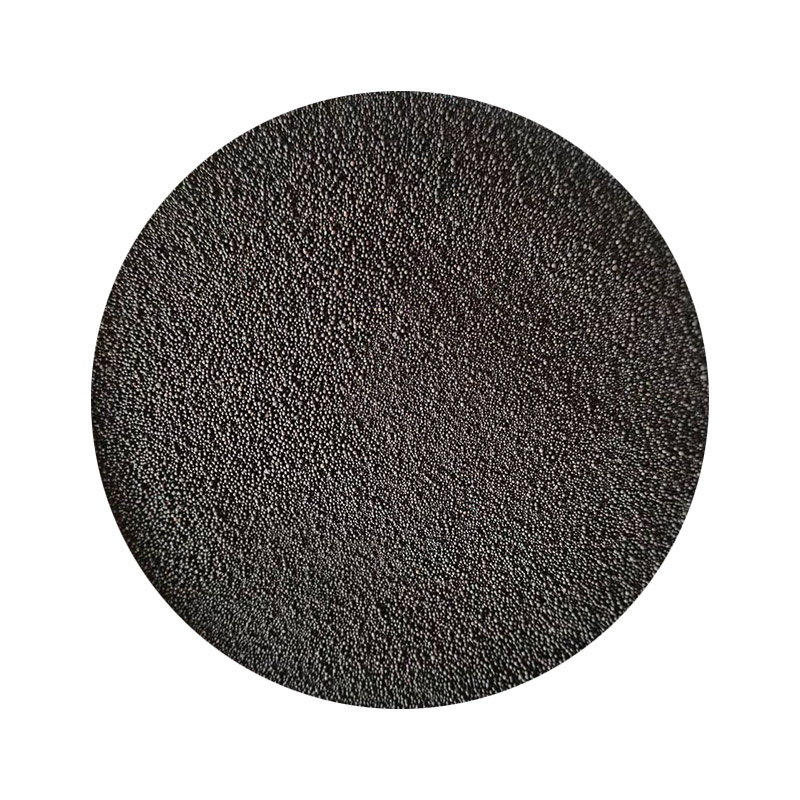
Sustainability is another critical factor driving the adoption of 3D printing in sand casting. Traditional casting methods often generate substantial waste, as excess material is removed from patterns. However, 3D printing allows for more precise material usage, minimizing waste. Moreover, advancements in 3D printing technology have enabled the use of biodegradable and recyclable materials, aligning with the growing emphasis on sustainable manufacturing practices. This shift not only benefits the environment but also helps companies reduce operational costs associated with waste disposal and material procurement.
Moreover, the incorporation of 3D printing into the sand casting process leads to improved accuracy and repeatability. Traditional methods may introduce variations due to human error and inconsistencies in pattern production. In contrast, 3D printing relies on digital files that produce identical patterns every time, ensuring a higher degree of precision in the final cast products. This level of accuracy is crucial in industries that demand stringent tolerances, such as medical device manufacturing.
Despite its advantages, the transition to 3D printing in sand casting is not without challenges. Initial investment costs for industrial-grade 3D printers can be significant, and companies must also invest in training staff to operate the new technology effectively. Furthermore, the properties of the printed patterns need to be carefully considered to ensure that they withstand the rigors of the sand casting process. However, as technology continues to evolve and become more accessible, these challenges are likely to diminish.
In conclusion, 3D printing for sand casting represents a significant advancement in the foundry industry, offering increased efficiency, customization, sustainability, and precision. As manufacturers continue to explore and integrate this technology into their operations, we can expect to see a new era of innovation in metal casting that not only meets the demands of modern production but also paves the way for a more sustainable future. The potential for 3D printing in sand casting is vast, promising to redefine standards and practices within the industry for years to come.
Post time:Hyd . 11, 2024 19:53
Next:Understanding the Process of Creating Foundry Sand for Casting Applications