Understanding the Types of Sand Used in Sand Casting
Sand casting is one of the oldest and most versatile manufacturing processes, used to create a wide array of parts from metals and other materials. A crucial element of this process is the type of sand utilized, as it plays a significant role in determining the quality, efficiency, and outcome of the castings. This article will explore the various types of sand used in sand casting, their properties, and the reasons behind their selection.
The Basics of Sand Casting
Sand casting involves creating a mold from sand to hold molten metal, which then solidifies to form a part. The process typically involves several stages pattern making, molding, pouring, and finishing. The choice of sand is pivotal in ensuring the mold can withstand high temperatures and hold the desired shape. The most common type of sand used in this process is silica sand, but it’s important to understand that not all sands are created equal.
Types of Sand
1. Silica Sand Silica sand is primarily composed of silicon dioxide (SiO2) and is the most widely used material in sand casting. Its high melting point and excellent thermal stability make it suitable for casting ferrous and non-ferrous metals. Additionally, silica sand has good flowability, allowing it to fill intricate patterns effectively, which helps in producing detailed molds.
2. Green Sand Green sand is a mixture of silica sand, clay, and moisture. It gets its name from the fact that it is not baked or hardened before use. This type of sand is used extensively because it is economical and offers excellent moldability. Green sand molds can retain their shape even under the heat of molten metal. The addition of clay provides cohesion to the sand grains, allowing the mold to withstand the pouring process.
3. No-Bake Sand No-bake sand is another popular choice, consisting of silica sand mixed with a resin bonding agent. Unlike green sand, this type is chemically cured at room temperature rather than requiring moisture. No-bake sands can be prepared in advance, allowing for higher production rates and the ability to create more complex shapes. They also offer good surface finishes, making them the preferred choice for high-quality castings.
4. System Sand System sand is a type of high-quality silica sand that is used in automatic molding processes. This sand is reclaimed and reused several times in modern foundries. System sand is carefully processed to maintain its quality, thus ensuring consistent results across multiple casting cycles. Its fine grain structure allows for better mold quality and reduced defects in the final product.
what type of sand is used in sand casting
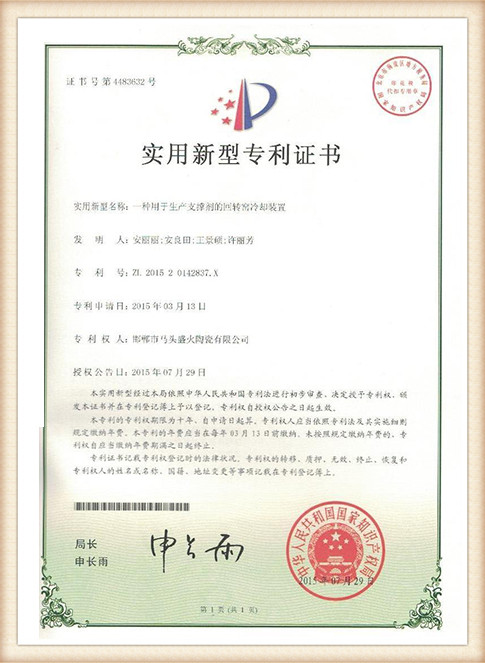
5. Casting Sand with Additives In some cases, additives are mixed with sand to enhance its properties. For example, adding graphite can improve the mold's thermal conductivity, while additives like coal dust can help reduce oxidation of the molten metal. These enhancements cater to specific casting requirements and can lead to improved surface finishes or other desirable attributes.
Choosing the Right Sand
Selecting the appropriate type of sand for a particular casting process depends on several factors
- Type of Metal Different metals require different sand types to ensure the best results. Ferrous metals, for instance, are often cast using green sand, while more intricate shapes might be better suited for no-bake sand processes.
- Casting Complexity The complexity of the mold and pattern design can affect the choice of sand. For highly complex shapes, no-bake sands or greens sands used in combination with strong binders may be preferred.
- Cost Considerations Budget constraints can influence sand selection, as some types can be more expensive due to their processing and material costs.
Conclusion
In conclusion, the type of sand used in sand casting significantly affects the final product’s quality, production efficiency, and overall costs. Silica sand, green sand, no-bake sand, and system sand each have unique properties that cater to different casting needs. A thorough understanding of these sand types enables manufacturers to optimize their casting processes, yielding high-quality components that meet industry standards. As advancements in materials science continue, it is likely that innovative sand formulations will emerge, further enhancing the capabilities of sand casting operations.
Post time:Lis . 27, 2024 12:06
Next:Resin Bonded Sand Casting Techniques and Applications for Precision Manufacturing