What is a Sand Casting?
Sand casting is one of the oldest and most versatile metal casting processes used in manufacturing. It involves creating a mold from sand, into which molten metal is poured to create various parts and components. This method is widely employed in various industries, from automotive to aerospace, due to its adaptability, low cost, and ability to produce complex shapes.
The Process of Sand Casting
The sand casting process begins with the creation of a mold. Typically, a mixture of sand and clay, along with water, is used to make the mold. The first step is to form a pattern, which is a replica of the object to be cast. Patterns are usually made from durable materials like wood, metal, or plastic.
Once the pattern is ready, it is placed in a mold box, and sand is packed tightly around it. The sand must be compacted sufficiently to hold its shape when the pattern is removed. After the sand is packed, the mold is split into two halves, allowing for the removal of the pattern. This creates a cavity in the sand that corresponds to the shape of the desired part.
After the pattern is extracted, the two halves of the mold are reassembled, and a sprue or pouring cup is added. This allows the molten metal to flow into the mold cavity. Once everything is set, the mold is ready to receive the molten material.
The next step involves melting the metal, which can be done using various methods, such as induction furnaces, electric arc furnaces, or gas-fired furnaces. The type of metal used can vary widely, including aluminum, iron, bronze, and brass, depending on the application and desired properties of the final product.
what is a sand casting
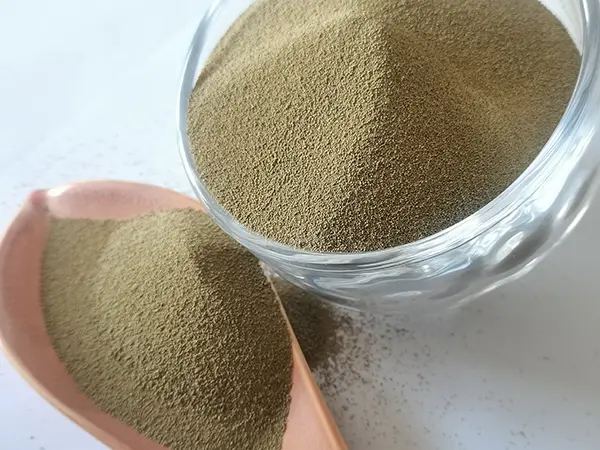
Once the metal is melted, it is poured into the mold through the sprue. The molten metal fills the cavity, takes the shape of the mold, and then solidifies as it cools. The cooling time varies depending on the size of the casting and the type of metal used.
After the metal has completely solidified, the mold is broken apart to reveal the cast part. This stage usually involves cleaning the casting to remove any sand residue, trimming excess material, and performing quality inspections.
Advantages of Sand Casting
One of the main advantages of sand casting is its flexibility in producing parts of various sizes and shapes, including those that are difficult to manufacture through other methods. It also allows for the casting of large components, which would be challenging with other techniques.
Additionally, sand casting is cost-effective, primarily for low to medium production volumes. The materials used for the mold are relatively inexpensive, and the process itself does not require extensive tooling. Moreover, the sands can be reused, which further minimizes waste and lowers production costs.
Conclusion
In summary, sand casting is a highly versatile and widely used metal casting process that offers numerous benefits for various manufacturing needs. Its ability to create complex shapes, coupled with its cost-effectiveness, makes it a favored choice in industries that require durable and precise metal components. As technology advances, sand casting continues to evolve, incorporating new materials and techniques to enhance its efficiency and effectiveness in producing high-quality castings.
Post time:Lis . 19, 2024 08:07
Next:Key Stages in the Sand Casting Process for Metal Fabrication