Types of Sand Used in Sand Casting
Sand casting is one of the oldest and most versatile methods of metal casting, primarily due to its adaptability and ease of use. The main component of the sand casting process is the sand itself, which plays a crucial role in determining the quality and properties of the final cast. This article will explore the different types of sand used in sand casting, their characteristics, and their applications.
1. Green Sand
Green sand is the most commonly used type in sand casting, composed of a mixture of silica sand, clay, and water. The term “green” refers to the moisture content in the sand rather than the color. This type of sand is highly malleable and can easily take the shape of the mold, providing excellent details in the casting. The clay acts as a binding agent, which enhances the sand’s strength, while the water helps to keep the sand particles together. Green sand is particularly favored for ferrous and non-ferrous metal casting and is known for its ability to withstand high temperatures.
Resin-bonded sand is another popular choice in sand casting applications. This type uses synthetic resin as a binding agent instead of clay, which provides superior strength and dimensional accuracy. The resin is mixed with the sand and then cured, either by heat or chemical reaction, forming a strong and rigid mold. Although this type of sand is more costly than green sand, it allows for intricate designs and finer details, making it ideal for high-precision applications like automotive parts and intricate machinery components.
types of sand used in sand casting
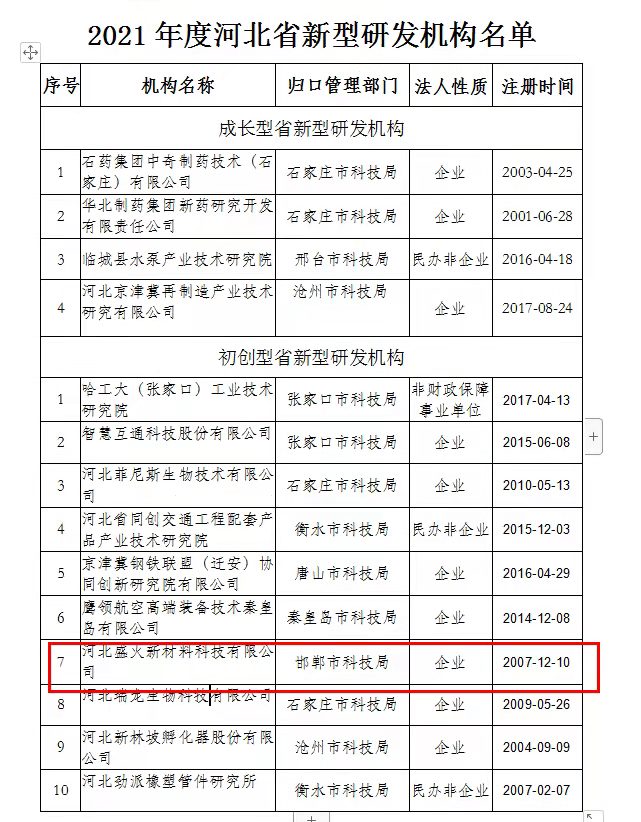
3. Silica Sand
Silica sand, composed primarily of silicon dioxide, is widely used in sand casting processes due to its high melting point and thermal stability. It offers excellent flowability, enabling it to fill molds effectively and create detailed castings. Silica sand can be used alone or mixed with clay and other additives. However, it has a tendency to produce more dust compared to other sands, which can pose respiratory hazards during handling. Nonetheless, its availability and versatility make it a popular choice in various casting applications.
4. Chrome Sand
Chrome sand is composed of chromite, primarily used when casting high-quality stainless steel and iron components. Due to its unique properties, like high thermal conductivity and resistance to thermal shock, it is particularly suitable for casting high-heat or complex shapes. The addition of chrome sand enhances the mold's ability to handle heat without deforming or breaking, contributing to the overall quality of the casting.
Conclusion
Choosing the right type of sand for sand casting is vital for achieving the desired outcomes in terms of strength, detail, and overall casting quality. Green sand remains a staple in the industry due to its cost-effectiveness and ease of use, while resin-bonded sand is preferred for high-precision applications. Silica and chrome sands also play significant roles, each contributing unique properties that cater to specific casting needs. As technology advances, the development of new sand mixtures continues to enhance the capabilities and applications of sand casting in modern manufacturing.
Post time:Říj . 30, 2024 19:24
Next:metal sand casting process