Types of Sand Casting
Sand casting is one of the oldest and most widely used manufacturing processes for creating metal parts. This versatile method involves the use of sand as the primary mold material, allowing for the production of complex shapes and designs. There are several types of sand casting techniques, each with its own unique characteristics and applications.
1. Green Sand Casting
Green sand casting is the most common method used in the industry. It utilizes a mixture of sand, clay, and water to form the mold. The term green refers to the fact that the mold is not dried or baked before pouring molten metal into it. This process is favored for its cost-effectiveness and flexibility. Green sand molds are easy to create, making them suitable for both large and small production runs. Furthermore, the sand can be reused multiple times, reducing waste.
2. Dry Sand Casting
In dry sand casting, the sand mixture is baked or dried in an oven to harden it before the casting process takes place. This creates a more durable mold that can withstand higher temperatures and pressures. Dry sand casting provides a smoother surface finish compared to green sand casting, making it ideal for intricate designs that require fine details. However, this method is generally more expensive due to the additional energy required for drying the molds.
types of sand casting
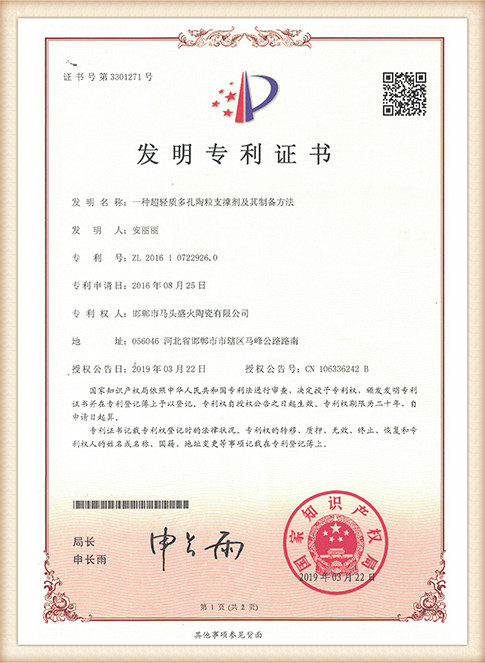
Resin sand casting involves using a resin binder mixed with silica sand. The mixture is more resistant to thermal deformation and can produce intricate shapes with excellent surface finishes. This technique is particularly beneficial for producing large castings with thin wall sections. Resin sand molds have a good dimensional accuracy, which reduces the need for extensive machining after casting. However, the cost of resin can make this method less economical for certain applications.
4. Shell Mold Casting
Shell mold casting uses a mixture of sand and a thermosetting resin to create thin-walled molds. The process involves preheating the metal pattern so that the sand mixture adheres to it and creates a shell. After curing, the shell molds are assembled, and molten metal is poured in. This method is known for very high dimensional accuracy and excellent surface finish, making it suitable for complex parts with tight tolerances, such as automotive components.
5. Lost Foam Casting
In lost foam casting, a foam pattern is covered with a sand mixture, and molten metal is poured directly into the mold, vaporizing the foam pattern. This technique allows for the production of complex geometries without the need for a traditional mold. It is particularly effective for low to medium production runs and creates parts that require minimal finishing work.
Conclusion
Sand casting remains a fundamental process in the manufacturing industry due to its adaptability and cost-effectiveness. Understanding the various types of sand casting techniques enables manufacturers to select the most appropriate method for their specific requirements, leading to improved productivity and higher quality castings. Each type has its strengths and weaknesses, making it essential to consider the application's demands when choosing the right casting technique.
Post time:Říj . 05, 2024 05:42
Next:steel sand casting suppliers