Steps in Sand Casting A Comprehensive Guide
Sand casting, also known as sand mold casting, is one of the oldest casting methods used in manufacturing. The process involves using a sandy material to create molds into which molten metal is poured to produce various parts. This method is not only cost-effective and versatile but also suitable for a wide range of metals. Below, we outline the key steps involved in the sand casting process.
1. Pattern Making
The first step in sand casting is to create a pattern, which serves as a replica of the desired part. Patterns are typically made from materials such as wood, plastic, or metal. The choice of material often depends on the production volume and the required dimensional accuracy. The pattern is crafted slightly larger than the final component to accommodate for the shrinkage of the metal as it cools.
2. Mold Preparation
Once the pattern is complete, the next step is preparing the mold. This involves taking the pattern and placing it into a mixture of sand and a binding agent. The sand is typically a silica-based product, and the binding agent may be clay or resin. The mold is created in two halves – the cope (top half) and the drag (bottom half). After placing the pattern into the sand mixture, the sand is compacted around the pattern to ensure that it retains its shape when the pattern is removed.
3. Pattern Removal
After the sand has been compacted, the pattern is carefully removed from the mold. This step is crucial as it determines the precision of the mold cavity. A good mold should maintain the intricacy of the pattern without breaking apart. In most sand casting processes, the pattern is removed directly after molding, although in some cases, it may be left in place until the mold is ready for pouring.
4
. Mold AssemblyOnce the patterns are removed, the two halves of the mold (cope and drag) are brought together. At this stage, any necessary additional components like gates and risers are added. Gates are channels that allow the molten metal to enter the mold, while risers act as reservoirs of excess metal to compensate for shrinkage during cooling. Proper design of these components is vital for ensuring a smooth casting process.
steps in sand casting
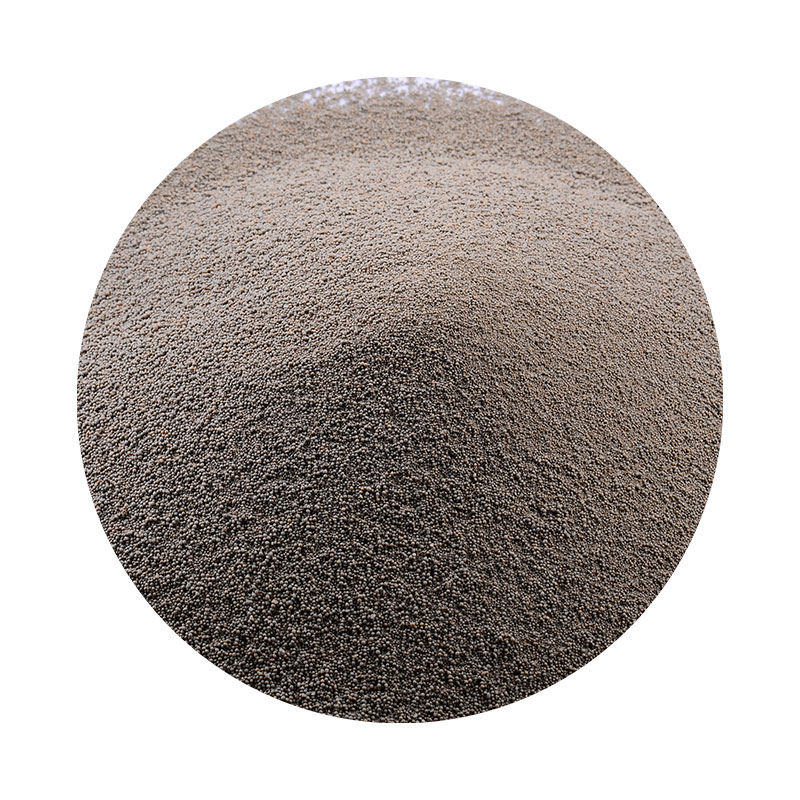
5. Pouring
With the mold assembled and ready, the molten metal is now poured into the mold cavity through the gates. The temperature of the molten metal and the pouring technique can significantly affect the final casting quality. There are various pouring methods, including gravity pouring and pressure pouring, depending on the melt and mold design. Care must be taken to avoid defects such as oxidation and porosity, which can compromise the integrity of the cast.
6. Cooling
After pouring, the molten metal needs time to cool and solidify within the mold. The cooling time will depend on several factors, including the metal type, mold material, and thickness of the casting. During this phase, it’s essential to avoid rapid temperature changes that could lead to cracking or warping of the casting.
7. Casting Removal
Once the metal has cooled and solidified, the next step is to break the mold to remove the casting. This is typically done by hand or with mechanical means, depending on the size of the casting. The sand mold is typically not reusable for high-volume production, although with certain techniques, it can be reprocessed.
8. Finishing Processes
After removal, the cast part usually requires finishing processes such as sandblasting, machining, or grinding to achieve the desired surface finish and dimensional accuracy. This step also includes removing any excess material left from gates and risers.
Conclusion
Sand casting remains a widely used method in manufacturing due to its simplicity and effectiveness. Understanding the steps involved in sand casting helps in ensuring high-quality cast parts while minimizing defects. As manufacturing continues to evolve, sand casting will undoubtedly retain its pivotal role in producing components across various industries.
Post time:Říj . 10, 2024 19:38
Next:Sand Casting Techniques for Precision Metal Printing and Manufacturing Solutions