Sand Casting Techniques A Comprehensive Overview
Sand casting, one of the oldest and most versatile metal casting processes, holds a significant place in the manufacturing industry. The technique has been employed for centuries to create intricate metal components with high precision. This article explores the various sand casting techniques, their advantages, and the steps involved in the process.
What is Sand Casting?
Sand casting is a process that involves creating a mold from sand to produce metal parts. The mold is typically formed using a mixture of sand, clay, and water, which gives it strength and flexibility. The primary materials used are silica sand and a bonding agent (usually clay). Once the mold is prepared, molten metal is poured into it to create the desired shape.
Key Techniques in Sand Casting
1. Green Sand Casting Green sand casting is perhaps the most common method, which utilizes a mixture of sand, clay, and moisture. This green sand mold allows gases to escape during the pouring of molten metal. The advantage of this technique lies in its cost-effectiveness and recyclability. The sand can be reused multiple times without significant loss of quality.
2. Cold Box Process The cold box process involves using a resin-coated sand that hardens at room temperature when exposed to a curing agent. This technique allows for more precise and detailed mold shapes compared to green sand casting. It is particularly well-suited for high-volume production runs where dimensional accuracy is critical.
3. No-Bake (Chemically Bonded) Process In this method, a mixture of sand and a binder (like a chemical resin) is prepared, which hardens at room temperature. The no-bake process is ideal for complex molds and larger parts due to its strength and ability to capture intricate details. However, it can be more costly and time-consuming than green sand casting.
4. Lost Foam Casting This innovative technique involves creating a pattern from foam, which is then coated in sand. When molten metal is poured into the mold, the foam evaporates, leaving behind the desired metal part. Lost foam casting is beneficial for producing complex shapes with excellent surface finishes.
The Sand Casting Process
The sand casting process can be broken down into several key steps
sand casting techniques
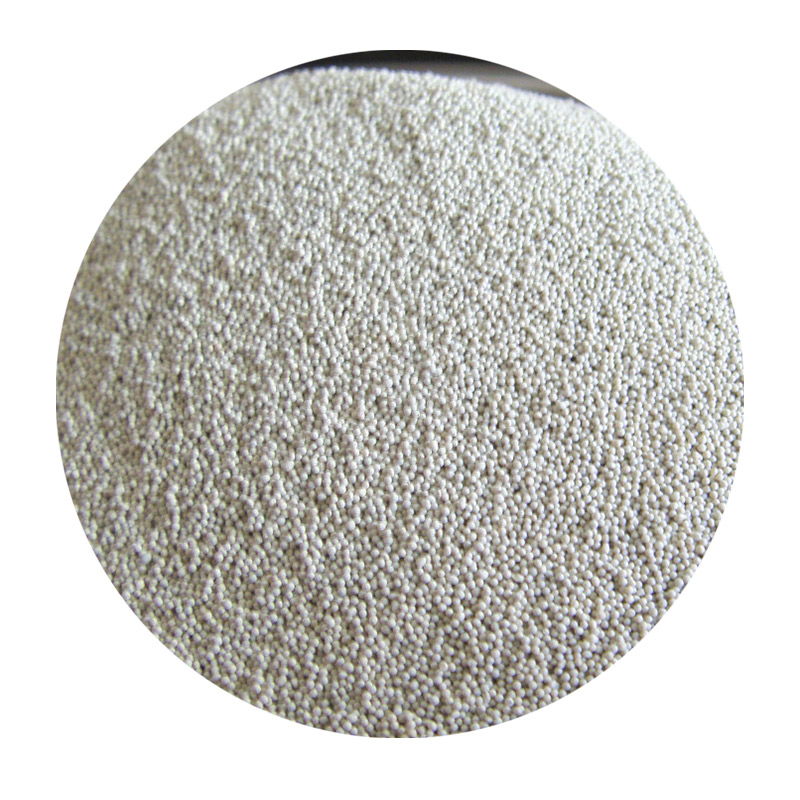
1. Pattern Making A pattern is created to form the cavity for the mold. This pattern can be made from various materials, including metal, wood, or plastic, and is designed to be slightly larger than the final product to account for shrinkage during cooling.
2. Mold Preparation The pattern is placed in a mixture of sand and a bonding agent to form the mold. The sand is compacted around the pattern, and once it hardens, the pattern is removed, leaving behind a cavity.
3. Pouring Molten metal is poured into the mold cavity, filling it completely. This must be done swiftly to avoid any solidification before the mold is filled.
4. Cooling After pouring, the metal is allowed to cool and solidify. The time required for cooling depends on the size and thickness of the casting.
5. Mold Removal Once the metal has cooled, the sand mold is broken away to reveal the final casting. It is a delicate process, requiring care to avoid damaging the product.
6. Finishing The completed casting may require additional finishing processes such as machining, cleaning, and surface treatment to achieve the desired specifications.
Advantages of Sand Casting
Sand casting offers several benefits, making it a popular choice in various industries
- Cost-Effectiveness The materials required for sand casting are relatively inexpensive, especially for low to medium production volumes. - Versatility It can accommodate a wide range of metals, including aluminum, cast iron, and steel, as well as various component sizes and shapes. - Rapid Prototyping Sand casting enables quick iterations for prototypes, facilitating efficient design modifications.
Conclusion
In conclusion, sand casting remains a vital technique in metal manufacturing due to its adaptability and economic feasibility. Its various methods, including green sand casting, cold box processes, and lost foam techniques, provide manufacturers with the flexibility to produce complex parts with precision. As technology continues to advance, sand casting techniques will likely evolve, further enhancing efficiency and product quality in the rapidly changing industrial landscape.
Post time:Lis . 19, 2024 15:56
Next:coated sand casting