Understanding the Sand Casting Foundry Process
Sand casting is one of the oldest and most widely used metal casting processes, renowned for its simplicity, versatility, and cost-effectiveness. The sand casting foundry process involves several key steps to transform raw materials into finished metal products. This article will explore the fundamental stages of the sand casting process and its significance in modern manufacturing.
The first step in the sand casting process is mold preparation. Molds are typically made from a mixture of sand, clay, and water, which creates a pliable yet sturdy structure capable of holding the molten metal. The foundry worker creates a pattern—an exact replica of the desired casting—often made from metal or plastic. This pattern is pressed into the sand to form an impression, which is then reinforced with metal frames. The shape and size of the pattern directly influence the final product's specifications.
Once the mold is prepared, the next step is to melt the metal. Common metals used in sand casting include aluminum, bronze, and iron. The metal is heated in a furnace until it reaches a molten state. The choice of metal often depends on the desired properties of the finished product, such as strength, weight, and resistance to corrosion.
With the metal ready, it is poured into the mold. This step requires precision, as the molten metal must be carefully introduced to avoid defects. Pouring too quickly can lead to uneven filling or turbulence, while pouring too slowly could cause premature solidification. Proper pouring techniques are crucial for achieving a successful casting without flaws.
sand casting foundry process
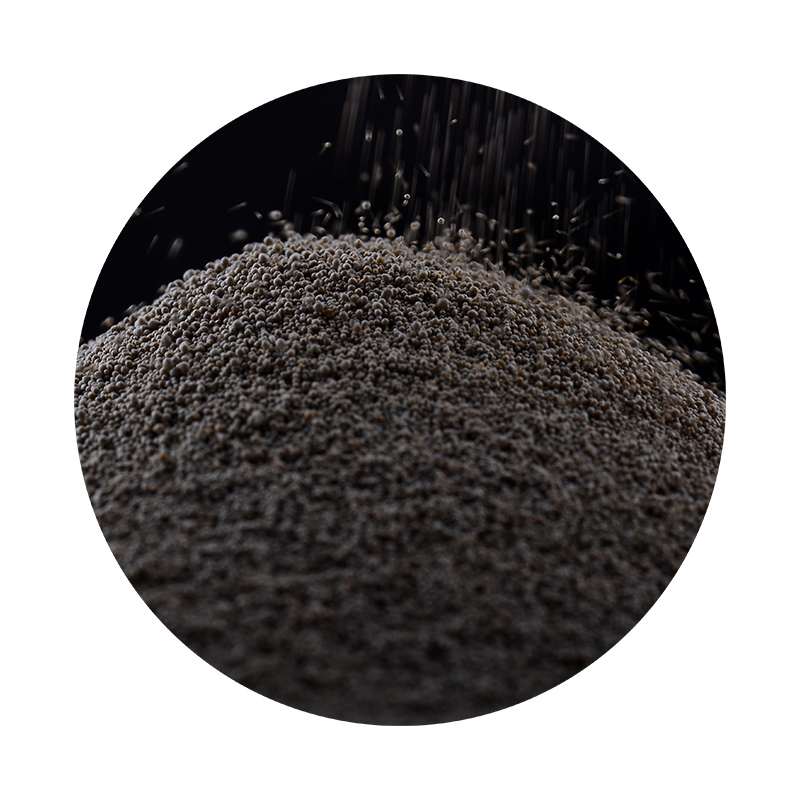
After the molten metal is poured, it begins to cool and solidify within the mold. The cooling time varies depending on the metal type and the thickness of the casting. Once solidification is complete, the mold is broken away to reveal the cast product. This phase can often involve the use of mechanical tools to aid in removing the mold while minimizing damage to the cast.
After extraction, the casting may undergo various finishing processes. These can include grinding, machining, or sandblasting, all aimed at achieving the desired surface finish and dimensional accuracy. Quality control is critical here, as any defects must be identified and rectified to ensure the product meets industry standards.
The sand casting foundry process is widely utilized across various industries, including automotive, aerospace, and construction, due to its ability to produce complex shapes and large components. Its adaptability, combined with the use of readily available materials, makes sand casting a vital part of the manufacturing landscape.
In conclusion, sand casting remains a cornerstone of metal fabrication. Understanding its process not only highlights the craftsmanship involved but also emphasizes its importance in producing reliable and diverse metal components essential for modern machinery and infrastructure.
Post time:Říj . 30, 2024 20:56
Next:sand castings supplier