The Role of Sand in Sand Casting
Sand casting is a widely used metal casting process that plays a crucial role in modern manufacturing. One of the key components of this process is sand, which serves as the mold material. The characteristics of the sand used in sand casting significantly affect the quality of the final metal object, making it essential to choose the right type and mixture of sand.
The most commonly used sand in sand casting is silica sand. Silica sand is composed primarily of silicon dioxide (SiO2) and is favored for its high melting point, excellent thermal stability, and ability to maintain shape under heat. It is also relatively inexpensive and readily available, making it an attractive choice for many foundries. However, not all silica sand is suitable for casting; factors like grain size, roundness, and clay content can impact the casting process.
In order to improve the performance of silica sand in sand casting, binding agents are often added. The most common binder is clay, which helps the sand grains adhere to one another, creating a strong mold. The mixture of sand and clay is known as “green sand,” and it has excellent properties for creating molds that can withstand the intense heat of molten metal. Additionally, water is mixed into green sand to activate the binder, resulting in a malleable yet sturdy mold that can be easily shaped.
sand used in sand casting
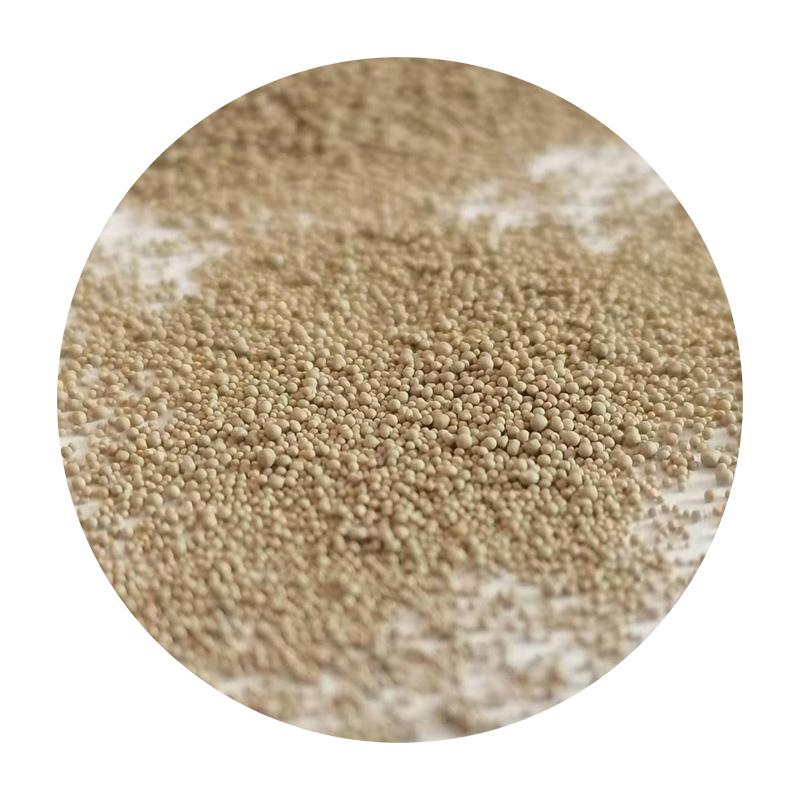
Another type of sand used in sand casting is “lost foam” sand, which incorporates polystyrene beads. This method allows for more intricate designs and a smoother surface finish. The beads evaporate when the molten metal is poured into the mold, leaving behind a highly detailed casting. Lost foam casting is particularly beneficial for complex parts that would be difficult to produce with traditional sand casting methods.
The choice of sand and its preparation can significantly impact the properties of the final casting. For instance, a well-prepared sand mold can reduce defects such as gas porosity and improve the surface finish of the casting. Conversely, poorly prepared sand can lead to weak molds, resulting in distortions or failures during the casting process.
Recycling sand is another important aspect of sand casting. After casting, the sand can often be cleaned and reused, reducing waste and costs. Modern foundries employ advanced sand reclamation technologies to efficiently process and recycle used sand, ensuring that it maintains its casting qualities over multiple uses.
In conclusion, sand is a vital component of the sand casting process, with its properties directly influencing the quality and performance of cast metal products. The choice of sand, the addition of binders, and the proper preparation all play critical roles in determining the success of the casting. By understanding and optimizing these factors, foundries can produce high-quality castings that meet the demands of various industries. This highlights the essential nature of sand not only as a material but also as a key player in the art and science of metal casting.
Post time:Zář . 06, 2024 01:53
Next:High-Quality Ceramsite for Lightweight Construction and Insulation