Sand casting, a favored process in metalworking, is widely used for manufacturing metal parts across various industries. This technique involves creating a mold from sand and using it to cast molten metal into desired shapes. The alloys used in sand casting significantly impact the quality, durability, and applicability of the final product. In this article, we will explore key alloys commonly employed in sand casting, their properties, and their applications.
One of the most prevalent metals used in sand casting is aluminum. Aluminum alloys, particularly those in the 3xxx and 5xxx series, offer excellent corrosion resistance, lightweight properties, and good machinability. These characteristics make aluminum an ideal choice for automotive and aerospace components, such as engine blocks and frames, where reducing weight without sacrificing strength is crucial. Moreover, aluminum's versatility and recyclability add to its appeal in modern manufacturing.
Another significant category of sand casting alloys is iron-based metals. Gray cast iron is one of the most widely used alloys in this category. It is known for its excellent casting characteristics, high wear resistance, and good machinability. These properties make gray cast iron suitable for manufacturing heavy machinery components, such as engine blocks and cylinder heads. Additionally, ductile iron, which offers improved tensile strength and ductility compared to gray cast iron, is increasingly popular for applications requiring high strength, such as automotive components and industrial machinery.
Copper alloys, particularly bronze and brass, are also commonly utilized in sand casting. Bronze, an alloy of copper and tin, is known for its strength, corrosion resistance, and low friction properties, making it ideal for marine applications and bearing components. Brass, composed of copper and zinc, is celebrated for its machinability and aesthetic appeal, often used in decorative items, plumbing fittings, and electrical connectors. The excellent thermal and electrical conductivity of copper alloys makes them highly valuable in specific applications, including electrical and plumbing systems.
sand casting alloys
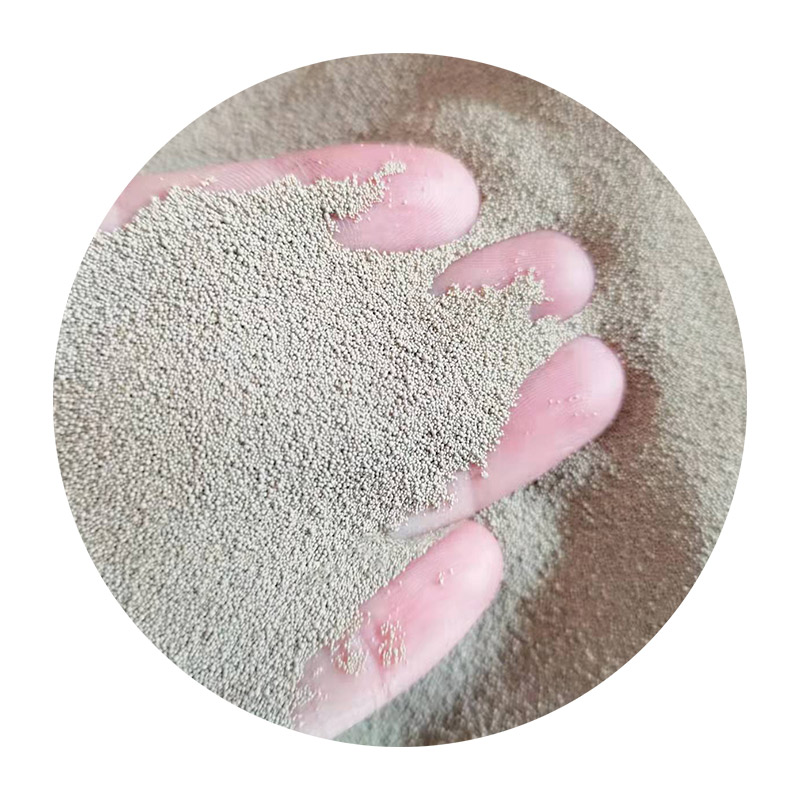
In recent years, the emergence of specialized alloys, such as nickel-based superalloys, has expanded the horizons of sand casting. These superalloys are engineered to withstand extreme temperatures and corrosive environments, making them essential in industries like aerospace and gas turbine manufacturing. The intricate sand casting process allows for the production of complex shapes and geometries, enabling the manufacture of high-performance components that meet rigorous industry standards.
Despite the numerous advantages of sand casting alloys, selecting the appropriate alloy for a specific application is crucial
. Factors such as mechanical properties, thermal stability, and environmental resistance must be considered to ensure the longevity and performance of the cast product. Furthermore, advancements in additive manufacturing and simulation technologies are paving the way for improvements in sand casting processes, allowing for greater design flexibility and reduced lead times.In conclusion, sand casting alloys play a fundamental role in the production of high-quality metal components in various industries. Understanding the properties and applications of these alloys is essential for engineers and manufacturers seeking to optimize their casting processes and achieve superior results. As advancements continue in alloy development and casting technologies, the future of sand casting remains bright, promising innovative solutions to meet the ever-evolving demands of modern engineering.
Post time:Zář . 15, 2024 19:24
Next:High-Quality Ceramic Sanding Discs for Superior Finishing