The Essentials of Metal Casting Sand
Metal casting is a critical process in the manufacturing industry, allowing for the production of intricate metal parts and components. At the heart of this process lies an essential material casting sand. This specialized sand plays a vital role in shaping the final product, influencing both the quality of the cast and the efficiency of the casting process.
Casting sand is primarily a mixture of fine aggregates, binders, and water. The most commonly used sand for metal casting is silica sand due to its high melting point and availability. Its granularity and shape also contribute significantly to performance. The properties of the sand directly impact the casting process and the final product, making the selection of the right type of sand crucial.
One of the key roles of casting sand is to create a mold that determines the shape of the final cast piece. The sand must be able to retain its shape when formed into a mold and must not easily break apart during casting. To achieve this, sand is often mixed with binders such as clay or resin, which provide the necessary strength and cohesiveness. Clay-bound sands are generally used for ferrous metal casting, while resin-bonded sands are preferred for non-ferrous metals due to their superior surface finish and dimensional accuracy.
metal casting sand
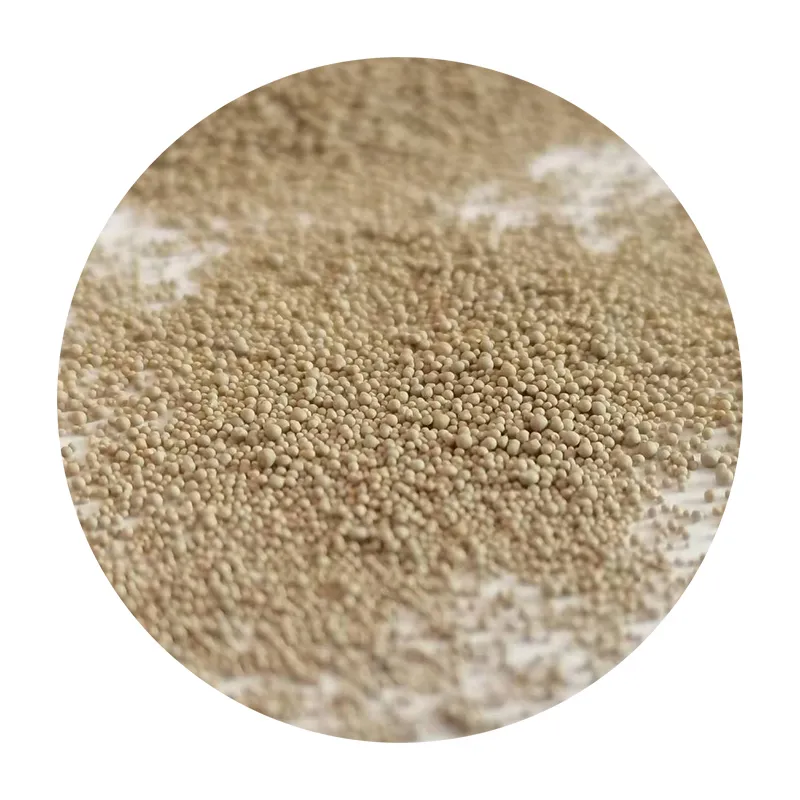
Moisture content is also an important factor in casting sand. The right amount of water helps to enhance the sand's bonding qualities, improving the mold's stability during pouring. However, too much moisture can lead to steam explosion during the casting process, creating defects in the final product. Therefore, monitoring and adjusting the moisture content is critical for achieving optimal results.
In addition to traditional silica sand, advancements in technology have led to the use of alternative materials. Materials such as zircon sand and olivine sand are being explored for specific applications due to their unique properties, such as higher thermal stability and lower thermal expansion. These alternative sands can yield improved casting quality and process efficiency.
The use of metal casting sand is not without environmental considerations. The disposal of spent sand can contribute to waste if not managed properly. Therefore, recycling methods are being implemented in many foundries to reduce waste and improve sustainability. Reclaimed sand can be treated and reused, which not only decreases the environmental impact but also reduces costs associated with purchasing new sand.
In conclusion, metal casting sand is a fundamental element of the casting process, influencing the quality, efficiency, and sustainability of metal production. As technology advances, the industry continues to explore new materials and methods to improve casting sand properties. Understanding these aspects is essential for manufacturers aiming to produce high-quality casts that meet specific performance standards while maintaining environmental responsibility. The ongoing research and development in this field promise a more efficient and sustainable future for metal casting.
Post time:Říj . 08, 2024 15:10
Next:Lost Foam Metal Casting