Lost Foam Casting An Innovative Foundry Process
Lost foam casting (LFC) is a modern manufacturing technique that has garnered attention in the foundry industry for its precision, versatility, and efficiency. This innovative process involves creating a foam pattern that is coated with a fine layer of refractory material. It offers distinct advantages over traditional casting methods, which is why it has become a popular choice for various applications, from automotive to aerospace and even art.
The lost foam casting process begins with the creation of a pattern made from polystyrene foam. This pattern is usually made to the exact dimensions of the desired metal part, which helps eliminate the need for complex tooling or machining. The foam pattern is then coated with a ceramic slurry, which solidifies and forms a shell around the pattern. Once the coating is hardened, the foam is removed—hence the term lost foam—and the cavity left behind is filled with molten metal. The final product is a casting that precisely reflects the detailed features of the original foam pattern.
Lost Foam Casting An Innovative Foundry Process
Another notable benefit of lost foam casting is the reduction of material waste. Traditional casting often requires the use of cores and additional machined components to achieve the desired final shape. In contrast, lost foam casting minimizes these concerns by eliminating the need for additional tooling or patterns, resulting in a more efficient use of materials. This can lead to a lower environmental impact and cost savings for manufacturers.
lost foam casting foundry
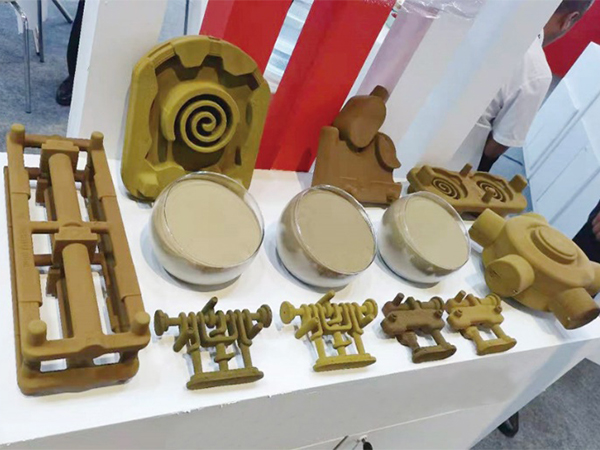
The LFC process is also highly flexible in terms of the types of metals that can be used. Whether it be aluminum, iron, or even non-ferrous materials, lost foam casting can accommodate a wide range of alloys and compositions. This versatility makes it an attractive option for foundries looking to diversify their production capabilities.
However, while lost foam casting presents many advantages, it also comes with its challenges. One significant obstacle is the sensitivity of the process to environmental conditions. Factors such as ambient temperature, humidity, and material properties can all impact the quality of the final casting. Careful control of these variables is essential to ensure consistent results. Additionally, the initial investment in equipment for lost foam casting can be higher than traditional methods, which may be a barrier for smaller foundries.
To mitigate these challenges, many firms have started investing in research and development to refine the lost foam casting process. Advanced technologies, including computer modeling and simulation, are being used to optimize patterns and improve the overall quality of the castings produced. Furthermore, the continued advancements in material science are paving the way for better binding agents and refractory materials, enhancing the effectiveness and reliability of the process.
In conclusion, lost foam casting is an innovative foundry process that offers numerous advantages, including high precision, reduced material waste, and flexibility in metal selection. While it does present some challenges, the ongoing research and technological advancements in this field are likely to overcome these issues. As industries continue to seek ways to improve efficiency and reduce environmental impact, lost foam casting is poised to play a significant role in the future of manufacturing. The combination of sustainable practices with high-quality output positions lost foam casting as an essential part of the evolving foundry landscape.
Post time:Pro . 12, 2024 18:05
Next:lost foam casting coating