Investment Casting vs. Sand Casting A Comprehensive Comparison
When it comes to manufacturing metal parts, two of the most commonly used techniques are investment casting and sand casting. Both methods have their unique advantages and disadvantages, making them suitable for different applications and industries. Understanding these differences is crucial for businesses looking to optimize their production processes and minimize costs.
Investment Casting
Investment casting, also known as lost-wax casting, is a precision casting process typically used for complex and intricate geometries. It begins with creating a wax pattern that is coated in a ceramic material. Once the ceramic shell hardens, the wax is melted away, leaving a mold for molten metal to be poured into. This process allows for tight tolerances and excellent surface finishes, often eliminating the need for extensive machining post-production. Investment casting is particularly favored in industries where precision is paramount, such as aerospace, automotive, and medical.
However, the investment casting process can be expensive due to the high cost of materials and the labor-intensive setup involved. The molds are often designed for specific parts, limiting their reusability for other products. Additionally, investment casting may not be cost-effective for large-scale production runs, where the cost per unit can significantly increase.
Sand Casting
investment vs sand casting
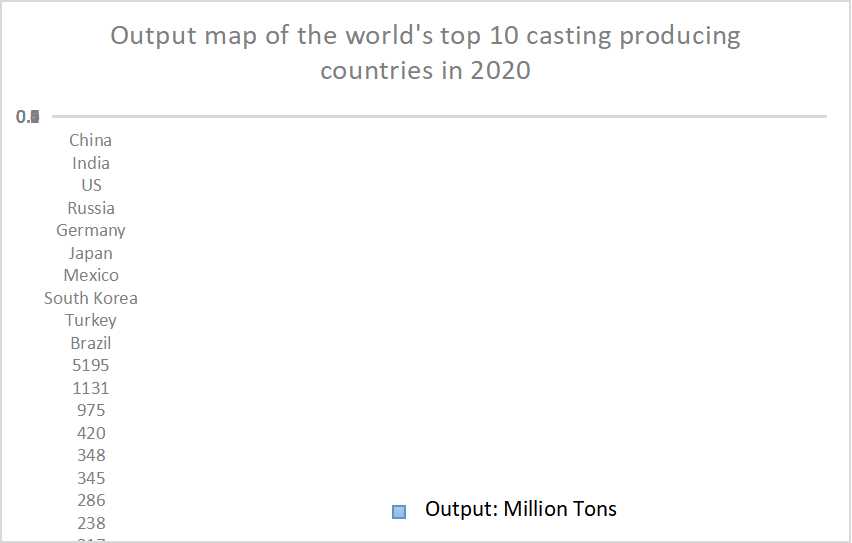
In contrast, sand casting is one of the oldest and most widely used casting methods. It involves creating a mold from a mixture of sand, clay, and water. The sand mold is formed around a pattern of the part, which is then removed to leave a cavity for the molten metal. Sand casting is highly versatile and can accommodate a wide range of part sizes and complexities. It is especially suitable for larger components where precision is less critical, making it a go-to method for industries such as construction, agriculture, and general manufacturing.
One of the key advantages of sand casting is its cost-effectiveness. The materials used in sand casting are relatively inexpensive, and the molds can be reused multiple times with proper maintenance. This process also allows for faster turnaround times when producing large quantities of parts. However, sand casting generally results in coarser surface finishes and lower precision than investment casting, necessitating additional machining processes for tight-tolerance applications.
Conclusion
Ultimately, the choice between investment casting and sand casting depends on specific project requirements, including design complexity, precision needs, production volume, and budget constraints. Investment casting excels in producing high-precision, complex parts, making it ideal for specialized applications. On the other hand, sand casting offers a more economical solution for larger, less intricate components.
In the dynamic world of manufacturing, understanding the strengths and limitations of each casting method empowers businesses to make informed decisions, optimize their production processes, and ultimately enhance their competitive edge in the market. Whether to invest in the high precision of investment casting or embrace the versatility of sand casting boils down to the specific needs of the project at hand.
Post time:Říj . 10, 2024 15:47
Next:make sand casting