Investment Casting Sand Key Element in Precision Metal Casting
Investment casting, a manufacturing process renowned for its ability to create complex shapes with excellent dimensional accuracy, heavily relies on a range of materials, one of which is casting sand. Sand plays a pivotal role in the overall casting process, enhancing the quality of the final product while also influencing operational efficiency. This article delves into the significance of investment casting sand, its types, properties, and its impact on the mold-making process.
Understanding Investment Casting
Investment casting, commonly referred to as lost-wax casting, involves creating a wax pattern that is subsequently coated in a refractory material to form a mold. Once the mold is created, the wax is melted and drained away, leaving a cavity in the shape of the desired metal component. Molten metal is then poured into this cavity, resulting in highly detailed and intricate parts. The quality of the mold directly influences the final product, and this is where investment casting sand plays an essential role.
The Role of Casting Sand
While investment casting traditionally utilizes a ceramic shell process, there are instances where casting sand is introduced into the workflow. The casting sand provides several advantages, including
1. Thermal Stability Casting sand is designed to withstand high temperatures, making it conducive for metal pouring. This stability is crucial during the cooling process, as it minimizes thermal shock and ensures a uniform cooling rate.
2. Surface Finish The right type of casting sand can significantly affect the surface finish of the casted part. Fine-grained sand yields smoother finishes, reducing the need for extensive post-processing.
3. Mold Strength The mechanical strength of the sand mix ensures that the mold holds its shape during the pouring process. Strong molds are less likely to deform, leading to consistent and accurate results.
4. Reusability Casting sand can often be reclaimed and reused, making the process more efficient and environmentally friendly. This reusability not only lowers costs but also reduces waste.
Types of Investment Casting Sand
Investment casting sand comes in various types, each serving different requirements
investment casting sand
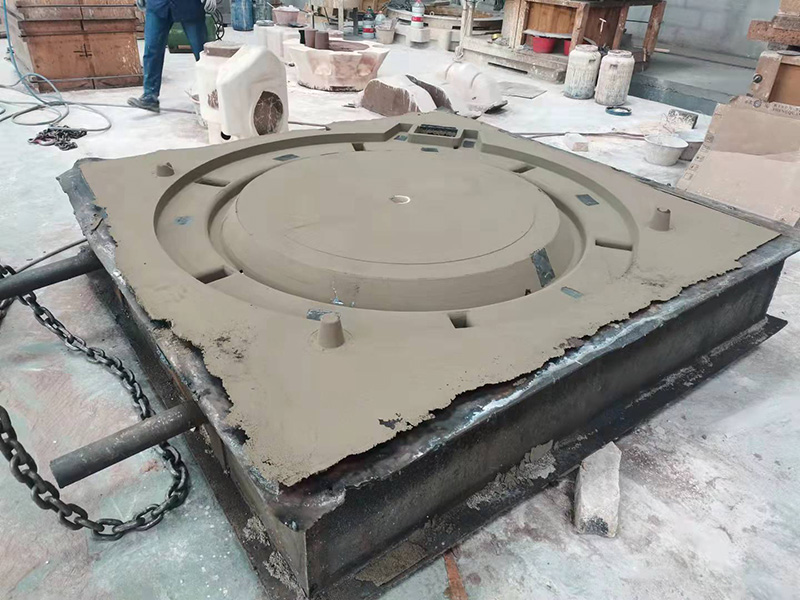
1. Silica Sand This is one of the most widely used types of casting sand due to its favorable properties such as high melting point and low thermal expansion. It is typically used when high precision and surface finish are required.
2. Zircon Sand Known for its superior thermal stability and low thermal expansion, zircon sand is ideal for casting high-temperature metals. It provides an excellent surface finish and is often used in demanding applications, such as aerospace components.
3. Chromite Sand This sand type is chosen for its excellent resistance to thermal shock and ability to withstand high temperatures. Chromite is often employed in casting ferrous metals due to its effective control of mold collapse.
Factors Influencing the Selection of Casting Sand
Choosing the right investment casting sand depends on several key factors
1. Casting Material The choice of metal being cast will significantly influence the casting sand parameters, as different metals have varying thermal and chemical properties.
2. Desired Finish The surface finish required for the final part is a determining factor. Finer sands are preferable for high-quality finishes, while coarser sands may be adequate for simpler geometries.
3. Production Volume For large-volume productions, the reusability and cost-effectiveness of the casting sand become paramount. Sands that can be easily reclaimed and processed for reuse are preferred.
4. Environmental Considerations Sustainable casting practices involve the selection of environmentally friendly sand options and processes that minimize waste and energy consumption.
Conclusion
Investment casting sand is an integral component of the casting process, influencing the quality, efficiency, and sustainability of manufacturing operations. Understanding the different types of casting sands and their properties allows manufacturers to select the ideal materials that meet their specific requirements. As the demand for precision metal components continues to rise, the role of investment casting sand will remain crucial in advancing casting technologies and improving product outcomes. With careful consideration and innovation, companies can harness the full potential of investment casting, delivering high-quality products to meet market needs.
Post time:Lis . 25, 2024 11:16
Next:advantages and disadvantages of sand casting