The Role of Foundry Sand in Concrete An Innovative Approach to Sustainable Construction
In the realm of construction, the search for sustainable materials that can substitute traditional aggregates is becoming increasingly crucial. One such material gaining traction is foundry sand, a byproduct of metal casting processes. This specialized sand, which is typically disposed of as waste, has shown great potential as a partial replacement for conventional fine aggregates in concrete. Utilizing foundry sand in concrete not only promotes recycling and sustainability but also enhances certain properties of the concrete mix.
What is Foundry Sand?
Foundry sand is produced in large quantities during the metal casting process, where it is used to create molds for steel and iron products. Traditionally, this sand is made from silica and is often coated with a resin or clay to improve its molding properties. After its initial use, foundry sand is generally discarded, leading to significant environmental concerns due to the increasing waste generated by the foundry industry. However, researchers and practitioners in the construction field have begun to explore its potential as a valuable resource.
Benefits of Using Foundry Sand in Concrete
1. Sustainability One of the most compelling reasons to consider foundry sand in concrete is its potential to reduce waste. By incorporating this byproduct into concrete mixes, the construction industry can minimize the demand for natural sand, which is increasingly being depleted due to excessive extraction. This not only contributes to environmental conservation but also encourages a circular economy within the industry.
2. Improved Concrete Properties Studies have shown that foundry sand can enhance several properties of concrete. Its angular and rounded grains can improve the workability of fresh concrete mixes, leading to better flow and placement. Additionally, foundry sand can contribute to increased compressive strength and durability in hardened concrete, particularly when used in moderate proportions.
foundry sand in concrete
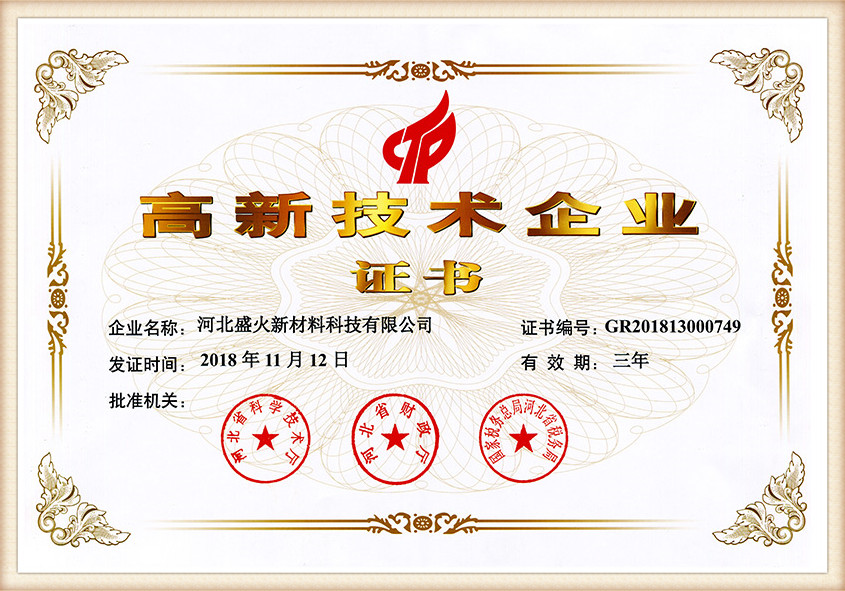
3. Cost-Effectiveness Utilizing foundry sand can also be cost-effective. As a waste material, it can be less expensive than traditional fine aggregates, leading to potential reductions in overall project costs. This is especially beneficial for large-scale construction projects where material costs significantly impact budget constraints.
4. Reduction of Environmental Impact Implementing foundry sand in concrete mixtures can also result in lower carbon emissions associated with mineral extraction and processing of natural aggregates. Furthermore, it reduces landfill waste, mitigating the environmental impact associated with traditional waste disposal methods.
Challenges and Considerations
Despite the numerous advantages, there are challenges associated with using foundry sand in concrete. One primary concern is the variability in the composition and quality of foundry sand, which can impact the performance of the concrete. Rigorous testing and quality control measures must be implemented to ensure consistency and reliability.
Another challenge is the perception and acceptance of foundry sand among construction professionals and regulatory bodies. Clear guidelines and standards for the use of foundry sand in concrete must be established to facilitate its wider acceptance.
Conclusion
As the construction industry continues to seek innovative solutions to combat environmental degradation, the utilization of foundry sand presents a promising avenue for sustainability. By transforming a waste product into a functional component of concrete, we not only reduce landfill pressures but also conserve natural resources. While challenges remain, ongoing research and development can help address these issues, paving the way for a more sustainable and efficient construction future. Embracing foundry sand in concrete mixes could very well be a substantial step towards a more eco-friendly built environment.
Post time:Pro . 16, 2024 11:26
Next:Understanding the Sand Casting Process and Its Key Techniques for Metal Casting