Foundry Molding Sand The Backbone of Casting Operations
Molding sand is an essential material in foundry operations, playing a critical role in the casting process. This versatile and adaptable medium is primarily used to create molds for metal casting, a process that involves pouring molten metal into the cavity of a mold to shape it into a desired form. The quality of the molding sand is pivotal to the success of casting, as it directly influences the final attributes of the cast part, including dimensional accuracy, surface finish, and mechanical properties.
Composition of Molding Sand
Foundry molding sand typically consists of sand grains, a binder, and water. The most commonly used type of sand is silica sand, which is abundant and has excellent heat resistance. The sand grains provide the bulk for the mold, while the binder (such as clay or resin) helps to hold the sand grains together, giving the mold its strength and integrity. Water is added to improve the plasticity of the mixture, allowing it to be shaped more easily. The ratios of these components can vary depending on the specific requirements of the casting process and the type of metal being poured.
Types of Molding Sand
There are several types of molding sand used in foundry operations, each suited for different applications
1. Green Sand This is the most common type of molding sand, consisting of silica sand, water, and clay. It is referred to as green because it is used in a moist state. Green sand molds are cost-effective and have good permeability, allowing gases to escape during pouring.
2. Dry Sand This sand is similar to green sand but is cured in an oven to remove moisture. It results in a more rigid mold that can withstand higher temperatures and provides excellent dimensional accuracy.
3. Resin Sand This type utilizes a resin binder instead of clay. Resin sand molds have superior surface finishes and dimensional stability. They are often employed for complex and intricate metal castings.
4. Shell Molds Created by coating a pattern with a mixture of sand and thermosetting resin, shell molds offer high precision and can produce smooth surface finishes, making them ideal for complex shapes.
5. Lost Foam Sand This involves creating a mold around a foam model, which evaporates when the molten metal is poured, leaving behind a detailed mold for casting intricate components.
foundry molding sand
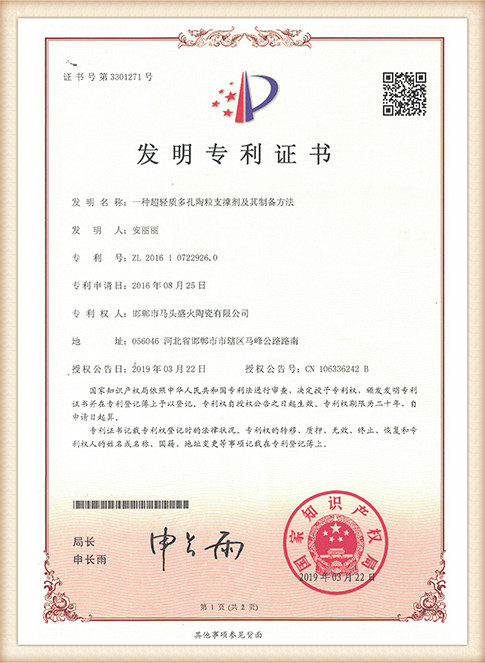
Properties of Quality Molding Sand
The effectiveness of molding sand is influenced by several key properties
- Refractoriness The ability of the sand to withstand high temperatures without deforming is crucial, especially when casting metals with high melting points.
- Permeability This property allows gases generated during the pouring of molten metal to escape, preventing defects such as gas holes or inclusions in the final casting.
- Cohesiveness A mold must maintain its shape and structural integrity during the metal pouring process, requiring adequate binding properties.
- Plasticity The mixture must have enough plasticity to be molded into intricate shapes while still being removable from the pattern without breaking.
Environmental Considerations
As industries focus on sustainability, the production and disposal of foundry molding sand are scrutinized for environmental impacts. Efforts are being made to recycle used foundry sand by processing it for other applications, such as in construction, landscaping, or as an aggregate in concrete production. This not only helps reduce waste but also conserves natural resources.
Conclusion
In summary, foundry molding sand is a foundational material in metal casting, influencing the quality and efficiency of the casting process. With various types available, each suited for specific applications, the selection of the right molding sand is vital for achieving desired outcomes in casting operations. As the foundry industry continues to evolve, so too will the materials and techniques used, potentially leading to advancements in molding sand technology that prioritize performance and sustainability. As manufacturers seek to optimize their processes, understanding the properties and applications of molding sand will remain crucial in the pursuit of quality castings.
Post time:Lis . 08, 2024 05:53
Next:Exploring the Properties and Applications of Spherical Sand in Modern Industries