The Role of Foundry Casting Sand in Metal Casting Processes
Foundry casting sand plays a vital role in the metal casting industry, serving as a primary material for creating molds in which molten metal is poured to form various components. The properties of casting sand significantly influence the quality and precision of the final product. This article explores the types of foundry casting sand, its properties, and its application in metal casting.
Types of Foundry Casting Sand
There are several types of foundry casting sand, each with unique characteristics that make it suitable for different applications
1. Silica Sand This is the most common type of casting sand, composed mainly of silicon dioxide. Its high melting point and excellent thermal conductivity make it ideal for casting various metals.
2. Olive Sand Derived from olivine, this sand has good thermal stability and is resistant to metal infiltration. Olive sand is often used in casting ferrous and non-ferrous metals.
4. Green Sand This mixture of clay, water, and sand is used for its ability to retain moisture, providing good strength and flexibility for mold making.
5. Resin-coated Sand With a layer of resin that hardens when heated, this type of sand allows for finer detail in the casting process and is often used for high-precision castings.
foundry casting sand
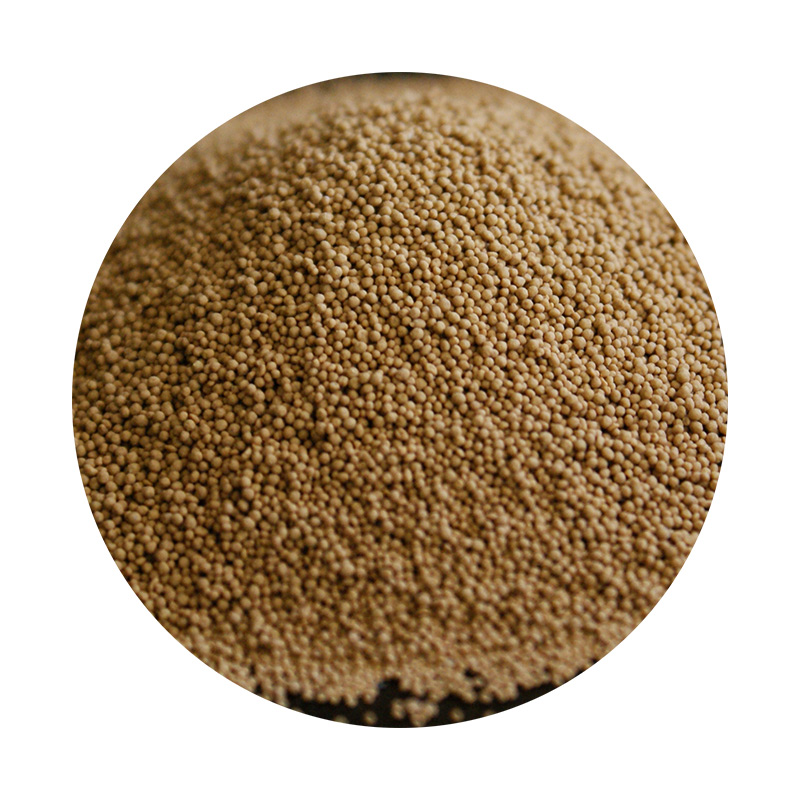
Properties of Foundry Casting Sand
The effectiveness of casting sand hinges on several key properties
- Grain Shape and Size The shape and size of sand grains affect the mold’s permeability and strength. Angular grains provide better interlocking and strength, while rounded grains improve flowability.
- Moisture Content The right amount of moisture enhances the binding capacity of the sand without making it too pliable. Optimal moisture content helps capture fine details and prevents cracking.
- Temperature Resistance Casting sands must withstand high temperatures without deforming. The ability to retain strength under heat is crucial for producing quality castings.
- Reusability Foundry sands can often be reclaimed and reused, making them cost-effective and environmentally friendly. The ability to recycle sand is increasingly important in sustainable manufacturing practices.
Applications in Metal Casting
Foundry casting sand is used extensively across various industries, including automotive, aerospace, and construction. Each application demands specific sand properties, making the choice of sand critical to the production process. For example, in the automotive industry, casting sand must withstand extreme conditions during the manufacturing of engine components, requiring high strength and thermal stability.
In conclusion, foundry casting sand is an indispensable material in metal casting processes. Its diverse types, unique properties, and significant applications underscore its essential role in the production of high-quality metal components. As industries continue to evolve, innovations in casting sand technology will likely enhance the efficiency and sustainability of metal casting practices.
Post time:Zář . 02, 2024 06:57
Next:metal sand casting process