Dry Sand Casting Process
Dry sand casting is a widely used method in the field of metal casting. This process involves pouring molten metal into a mold made of dry sand, which is compacted to form the desired shape. The simplicity and adaptability of dry sand casting make it a popular choice for producing a wide range of metal components.
Overview of the Process
The dry sand casting process begins with the preparation of the sand mixture. The primary component is silica sand, which is mixed with a binder to ensure that the mold can hold its shape without adding moisture. Unlike wet sand casting, where water is used to help bind the sand together, dry sand casting relies entirely on the binder materials, which can include sodium silicate or other chemical agents capable of hardening in the absence of moisture.
Once the sand is prepared, it is packed into a mold frame, which consists of two halves—the cope (top half) and the drag (bottom half). After the sand is compacted into the mold halves, the two pieces are joined together. The assembled mold has a cavity that reflects the desired shape of the final cast object.
Advantages of Dry Sand Casting
dry sand casting process
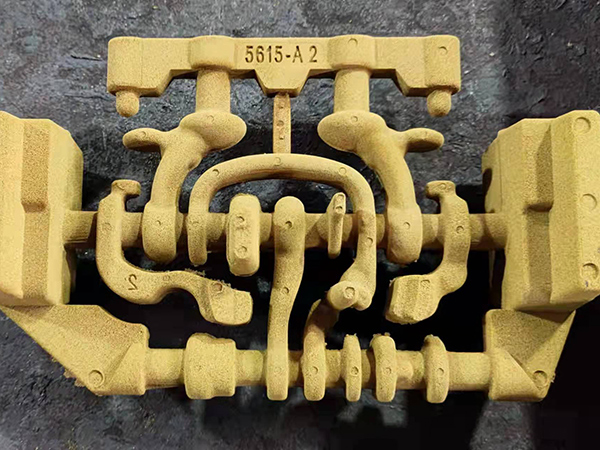
One of the main advantages of dry sand casting is its ability to produce highly detailed and accurate castings. The use of dry sand allows for fine surface finishes, reducing the need for extensive machining after casting. Additionally, the dry nature of the sand prevents issues such as gas entrapment, which can occur with wet sand molds, leading to defects in the finished product.
Dry sand casting is also cost-effective, especially for short production runs or custom parts. The materials used are inexpensive and readily available, making it an attractive option for manufacturers. Furthermore, the process can accommodate a variety of metal alloys, enabling the production of components with diverse properties, such as strength, ductility, and resistance to corrosion.
Applications of Dry Sand Casting
The applications of dry sand casting span many industries, including automotive, aerospace, and general manufacturing. It is often used to create intricate parts such as engine blocks, valve bodies, and housings. Due to its versatility, dry sand casting is also employed in crafting artistic pieces and architectural elements, where precision and surface finish are critical.
Conclusion
In summary, dry sand casting is a robust process that offers numerous advantages, such as accuracy, detail, and cost-effectiveness. By utilizing dry sand and chemical binders, manufacturers can achieve high-quality metal castings suited for various applications. As technologies advance, the dry sand casting process continues to evolve, incorporating innovations that enhance its efficiency and effectiveness. This enduring method remains a cornerstone in the foundry industry, illustrating the balance of tradition and innovation in manufacturing practices. With its wide-ranging applications and adaptability, dry sand casting will likely continue to play a vital role in modern engineering and manufacturing for years to come.
Post time:Říj . 06, 2024 08:47
Next:sand ceramic