Understanding the Sand Casting Process
Sand casting is one of the oldest and most versatile manufacturing processes utilized in various industries today. This technique is particularly favored for producing complex shapes and large components that would be challenging or costly to manufacture using other methods. This article delves into the intricacies of the sand casting process, its advantages, applications, and the steps involved.
What is Sand Casting?
Sand casting, also known as sand mold casting, is a process in which a mold is made from sand and then used to create parts by pouring molten metal into it. The sand provides the rigidity needed to hold the shape of the mold, while allowing for easy removal of the final product once it has cooled and solidified. The materials used in sand casting are relatively inexpensive and readily available, making it a popular choice among manufacturers.
Advantages of Sand Casting
One of the primary benefits of sand casting is its adaptability. The process can accommodate a wide range of metals, including aluminum, copper, and various steel alloys. Additionally, sand casting can produce both large and small parts, making it suitable for industries ranging from aerospace to automotive.
Another significant advantage is the ability to create complex geometries and intricate designs. The sand molds can be shaped and reconfigured easily, allowing for the production of parts with complex details that would be challenging to achieve with alternative methods, such as die casting.
Sand casting is also well-known for its cost-effectiveness. The materials required for sand molds are inexpensive, and because the process can be scaled up for mass production, it remains economical for larger runs of parts.
The Sand Casting Process
The sand casting process generally involves several critical steps
describe sand casting process
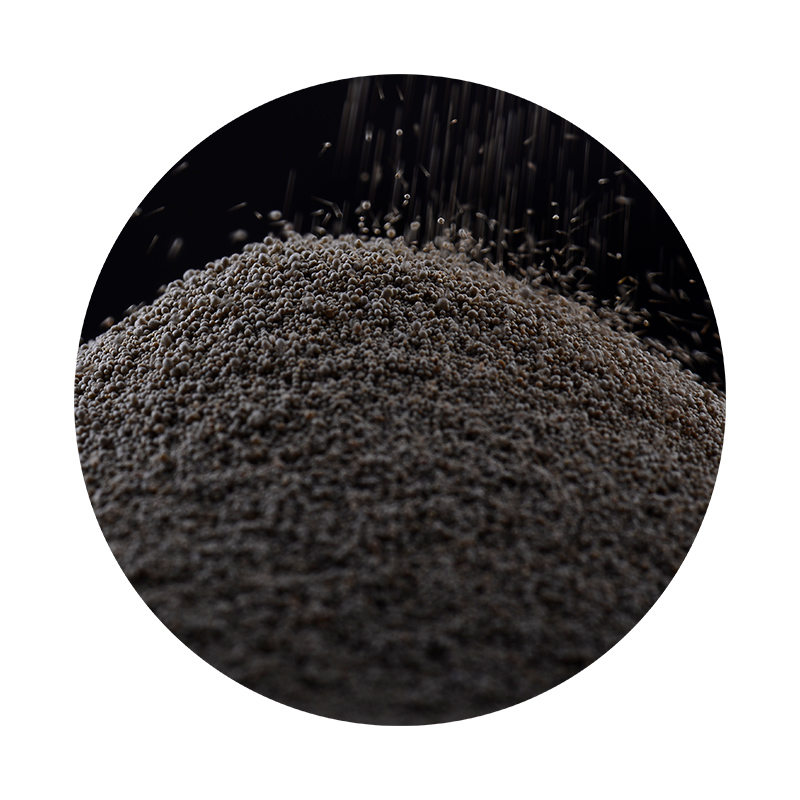
1. Pattern Creation The process begins with the creation of a pattern, which is a replica of the final part. Patterns can be made from various materials, including wood, metal, or plastic, depending on the size and complexity of the part. Patterns are typically oversized to account for metal shrinkage during cooling.
2. Mold Preparation Once the pattern is ready, it is placed in a mold box, and sand is packed around it. The sand used in casting is typically mixed with a binding agent, such as clay, to enhance strength and durability. After the sand is compacted, the pattern is removed, leaving an impression in the sand that will shape the final product.
3. Core Creation For parts with internal cavities, cores made from sand may be produced and placed within the mold. Cores ensure that hollow sections are formed in the final casting.
4. Melting and Pouring The metal intended for casting is melted in a furnace, reaching temperatures often exceeding 1,500°F (800°C). Once molten, the metal is poured into the prepared sand mold, filling the cavity and taking the shape of the pattern.
5. Cooling The molten metal is allowed to cool and solidify. The cooling time depends on the size and thickness of the part. It's essential to monitor this step closely, as cooling too quickly can lead to defects like cracking.
6. Mold Removal After the metal has fully cooled, the sand mold is broken away to reveal the casting. The casting may require additional cleaning and finishing processes, such as grinding or machining, to achieve the final dimensions and surface quality.
Applications of Sand Casting
Due to its versatility, sand casting is employed in numerous applications, including the manufacturing of engine blocks, transmission casings, and intricate machine components. It is widely used in the automotive industry, as well as in the production of sculptures and art pieces where unique designs are necessary.
In conclusion, the sand casting process is a vital manufacturing technique that offers numerous benefits, including flexibility, cost-effectiveness, and the ability to produce complex shapes. Its importance spans various industries, making it an essential method in modern manufacturing. As technology advances, the sand casting process continues to evolve, integrating new techniques and materials to further enhance its capabilities.
Post time:Lis . 24, 2024 15:09
Next:gold sands